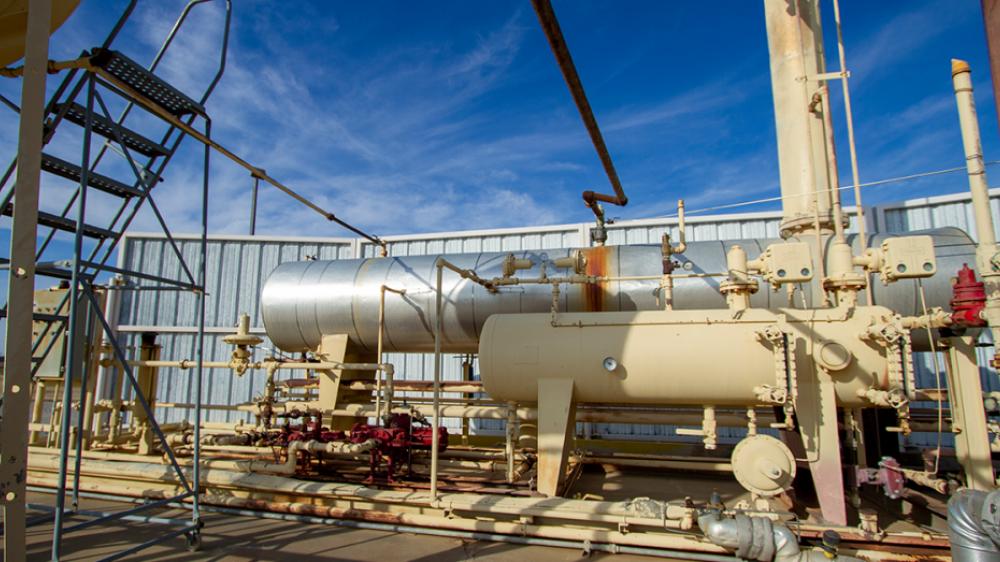
A flash separator is a critical piece of equipment in the natural gas dehydration process.
Producers use a flash separator to remove gas and condensate hydrocarbons from the glycol that was absorbed in the contact tower from the gas stream. "Flashing" refers to the process of liquid hydrocarbons immediately transitioning into a vapor phase when they move from high to low pressure.
What does a Flash Separator do in Natural Gas Dehydration?
After leaving the contact tower, the saturated or "rich" glycol will go one of three places: a glycol-to-glycol heat exchanger, a surge tank, or a glycol pump.
Contact Tower —> Heat Exchanger
The most common type of exchanger is a shell and tube. In this vessel, cool glycol from the tower travels through the tube, while hot glycol coming from the reboiler passes through the shell.
This heat transfer does two things:
- Warms up the glycol traveling to the flash separator, which helps the system separate the glycol from the other elements.
- Cools the glycol flowing into the contact tower, which helps the glycol absorb more water from the gas.
Contact Tower —> Surge Tank
Depending on the manufacturer, the glycol-to-glycol heat exchanger may be configured in such a way that the glycol return line coming from the tower coils through the surge tank before traveling to the flash separator.
The heat transfer takes place inside the surge tank, where the cooler "wet" glycol meets the hot "dry" glycol.
Glycol Pump
Whether it comes from the exchanger, surge tank, or directly from the contact tower, the glycol eventually enters the high pressure suction side of a glycol pump.
The glycol exits the pump on the low pressure side before entering the flash separator.
The pressure difference between the high suction and the low discharge sides of the glycol pump can be hundreds of pounds. The pressure in the tower (high suction side) can be as high as 2,000 psi, while the typical operating pressure of the flash separator (low discharge side) will be 30-50 psi.
The glycol pump is responsible for moving the glycol throughout the entire dehydration system.
How Many Phases are there in a Flash Separator?
The flash separator—which may also be called a "skimmer"—is most commonly a 3-phase vessel, meaning it separates three resources: hydrocarbons, glycol, and natural gas.
Hydrocarbons
Hydrocarbons and condensate separate from the saturated glycol, are "skimmed" off the top, and then fall into the condensate section of the vessel.
The condensate levels in this section of the vessel are controlled by a level controller and dump valve. The rich glycol travels under the condensate section and is dumped out of the bottom through the liquid outlet piping and dump valve actuated by a level controller.
Glycol
After leaving the separator, the glycol passes through a sock filter and removes solids and other impurities. It then travels through a carbon filter, which absorbs hydrocarbons, well chemicals and other impurities that the sock filter does not catch.
The separated gas travels along the top of the separator and passes through a mist extractor before exiting through a back pressure valve.
Natural Gas
The natural gas collected at this point can be sent to a flare to be incinerated or used as fuel for the burner in the reboiler.
If the gas is being used for the main burner fuel supply, it passes through a scrubber or volume pot to remove any remaining moisture, and then the gas travels through a supply gas regulator to reduce the pressure to accommodate the working pressure of the main burner.
Instrument supply gas will not normally be pulled from the flash separator because the gas quality is a concern. The instrument gas supply should always be as dry as possible. We recommend using the dry gas downstream of the contact tower for your instrumentation.
What is the Ideal Operating Pressure for this Separation Process?
When determining the operating pressure of the flash separator, you want to keep two things in mind:
- If the system pressure drop (back pressure) is too large on the glycol pump, the may pump to stall out. This back pressure can come from clogged filters, pipe fitting and elbows, operating pressure of the flash separator as well as any hydrostatic head pressure.
- More liquids will condense and fall out of gas when it is subject to higher pressure. Higher operating pressures in the flash separator will help to remove moisture from the gas. However, you must be aware that increasing the operating pressure of the flash separator will also increase the system pressure drop and may stall the glycol pump.
What Controls the Liquid Level in a Flash Separator?
Level Controllers
Producers use Float Operated Controllers to control both single-phase and interface fluids. The displacer senses level changes inside the flash separator and sends a pneumatic signal to a low pressure control valve ("dump valve") to make position changes in order to maintain your desired liquid level.
Low Pressure Control Valve
Low Pressure Control Valves typically used in this dump valve application are double acting, meaning there are two forces acting on the valve. The spring moves the valve stem to its fail position (closed), while diaphragm supply pressure coming from the level controller output moves it in the opposite direction (open).
Back Pressure Regulators
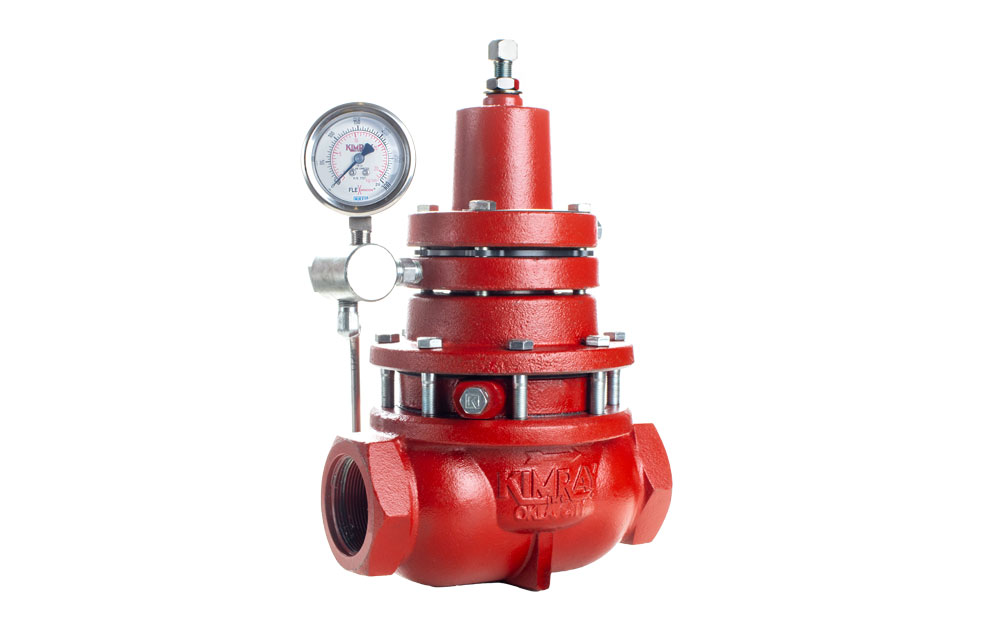
Back Pressure Regulators will monitor and control pressure upstream of the separator. This is located on the gas outlet piping, so it will control the pressure inside the vessel.
The set point is determined by how much tension is on the pilot spring. This can be set with the adjusted screw on top of the regulator. Putting more tension on the spring will increase the set point.