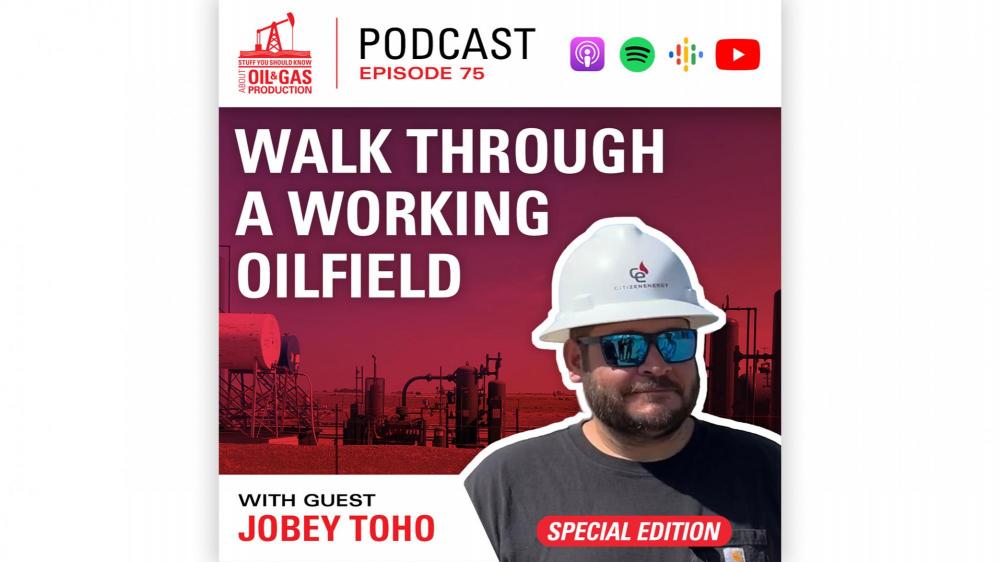
In this special edition of Stuff You Should Know about Oil and Gas, we travel to a working oilfield in Western Oklahoma and introduce you to a Production Superintendent named Jobey Toho, who explains how his operation is set up to produce, separate, and sell oil and natural gas.
Topics include:
- How Jobey's oilfield career got started
- What's a typical day for a pumper like?
- Equipment walkthrough
- What to look for when troubleshooting
- Where the resources go after they are separated
Where to listen online:
Transcription
Kyle & Curtis
On a sunny morning in early June, we grab our audio gear, jump into a red Kimray F150, and set out toward a well site about an hour west of our offices in Oklahoma City.
We're going to meet a man named Jobey Toho, who is a production superintendent for an energy producer in the so-called Scoop and Stack play.
Now, the Scoop and Stack is part of the Anadarko Basin where scientists tell us, a long time ago, organisms were trapped under layers and layers of rock. This bio-geological phenomenon is what has created fossil fuel—literally fuel that comes from the fossils of deceased plants and animals.
It’s sunny, and it will be hot later, but this early it’s not too bad, low 80s.
Oklahoma is a state in the middle of the country, where the rolling hills and towering trees of the eastern US flatten into the great prairies and plains of the west. As we drive, the ground grows progressively browner, and the trees fewer and farther between.
We meet at a gas station just off the highway, where trucks fuel up with the oil recovered from the earth underneath them.
Jobey spots us and waves us on, and we follow his white truck about 500 yards east of the gas station to a graveled area near three well heads.
After parking, we put on our hard hats and meet beside the trucks to shake hands.
Jobey
"How's it going? Morning, nice to meet you."
Kyle & Curtis
Jobey wears a black shirt, which matches his dark sunglasses, and a white hard hat.
We first asked him how he got started in the oil and gas industry, and you’ll hear in his answer there’s a kind of mystique about oilfield work in this area. It’s viewed as a place where you can make good money and form a solid career.
To get started, you just have to know a guy who knows a guy.
Jobey
When I was in high school actually my uncle was a lease operator, a pumper, and I thought, "Man, that guy has a great job. He gets to be outside and work with his hands." So I thought that's what I want to do.
I finally pestered the right person for long enough. After high school I'd call him every couple of weeks and say, "Hey, I'm ready to go to work."
Finally one day he called me back. "Hey, you ready to go to work?"
I said, "Yes I am."
So I became a lease operator 1 on December 15, 2008.
We pulled up on the first location and the guy training me explained we have water in this tank and oil in that tank.
I remember saying, "Wait, these things make water?" I didn't know. I was really, really green.
Kyle & Curtis
Jobey is a Production Superintendent, and he has several lease operators—or pumpers as he calls them— that work for him and oversee the production of various wells around the scoop and stack area.
His day begins before the sun.
Jobey
Unfortunately I get up about 5 o' clock every day. I go to the office and then looking in the morning at what the pumpers recorded the day before.
The way everything is now it comes out in excel spreadsheets and there are a hundred different reports. You're looking at target gas and target oil production.
It highlights the ones that are underperforming. And those are the ones you look at in the morning and try to figure out if it was just a one-time thing or a reoccurring thing and you have to troubleshoot so you can get your production back up where it should be.
So you troubleshoot, communicating with your guys.
We have a morning meeting with the other foremen and production staff and the guys above me. We review route by route, and I explain things like "We have these 2 well that are underperforming and this is what we did and what we're going to do to address it."
Kyle & Curtis
Jobey has about 6-8 people working for him at any given moment, and they are responsible for over 100 wells. Although that number fluctuates regularly depending on location and type of wells.
Jobey
Just on average there’s about 25-35 wells per route. And that just depends on the types of wells and geographically where they are located. It's not a hard number.
And the types of wells. If you have more compression versus free flowing you'll have more issues with compression and downtime, and you'll have to spend more time on those wells.
Same thing on dehydration units. You want to alot a pumper per well because it requires more time per well. You'll have to spend more time doing your walk around and equipment checks.
Kyle & Curtis
On an upstream oil-and-gas production site like this one, a lot has to happen before the resources downhole can be recovered, processed and sold.
Jobey walks us through everything that’s been done on this location up to this point.
First the well was drilled, then completed and plugged. After that, a roustabout crew installed the necessary piping and separation and processing equipment.
Then, a two-man flowback crew worked the well, managing the first volatile period after the well was opened, when sand still was a major factor before production began to normalize.
Jobey
Different companies do it different ways. I worked for a company before that they had a guy that specifically, all he did was flowback.
He was over the flow hands and, you know, really monitored the sand they were making and if they made gel and the equipment and got it going through the system.
And he was usually over that well for a month, six weeks, or two months, just depending on the amount of sand it made and the amount of attention the well needed.And his well count was fewer. So he could really isolate in on if there were 6, 8, 10, or 12 wells versus myself, where I have 90 to 120.
But we do things a little bit different here. We don't have 50 rigs going or, you know, astronomical numbers.
So, really the production foreman helped with the flowback quite a bit and we've used the same group of flow hands for quite a while. So they're all pretty in tune of how we as a company like things done and what we expect.
Kyle & Curtis
Jobey now begins to walk us through all that is going on at this location. We start where the well starts. He says it’s important to watch tubing and casing pressure gauges.
Jobey
This is your well head. You've got tubing and casing gauges that, that read kind of what's going on. And, and honestly, when it comes to troubleshooting, these might be some of the most basic "meat and potatoes" knowledge to look at—what your tubing and casing pressures are.
They can tell you a lot. If your tubing pressure's coming up, then you can start looking for some kind of obstruction in your choke or your flow line, or maybe just even line pressures up.
So these are real good basic tools just to keep an eye on.
But you know, as you're getting your product out of the ground, it's all mixed together. Here you're getting your oil, your gas, and water, and then you go down the line to your primary separator. Your primary scrubber.
We just run simple two-phase separators. Two-phase meaning you're just separating two things, your gas and your liquid.
Kyle & Curtis
Next to the three wellheads, there's a small tank and a pump that is sending something down hole into the wells at regular intervals. Kyle asks what it's doing.
Jobey
This is a corrosion scale inhibitor here. It's pumping down all three wells.
Normally after we start flowing the well back, we get most of our frack water back and we start feel like we're getting some water from the actual zone. We'll usually take a water analysis and then kind of go off there and see the tendencies of the water if they're more corrosive or scaling.
Then we'll try to pump down our casing. And it helps protect our surface equipment and our tubing as well. Especially in today's market when tubing prices—and just everything in general—is very expensive, you want to protect it. It's cheaper to treat it than it is to fix it posthumously.
Kyle & Curtis
We now walk east about 100 yards and approach the production equipment. There is a gravel berm about 2-3 feet high between us and the equipment, and it’s surrounded by a barbed wire fence to protect it from wildlife.
Inside the berm is a series of large and small cylindrical vessels, all painted matte gray. Some sit horizontally while others are vertical, and they are all connected by piping. Most of them also have small red valves on their outlets.
These vessels are used to process the resources that come from underground at the well head. This mostly involves separation.
Jobey explains what the various equipment is doing.
Jobey
From the wellhead, it all goes into the flow line. That goes across location and into our primary separator here, and this is where we separate our gas and our liquids from each other. And these are vertical separators.
There are many different types and brands and styles, and every company seems to kind of have their own way of doing things and what they like. But we use a lot of vertical separators and they really work out well for us.
Your gas flows out off the top, and from there it goes through a "last chance separator." So if you've got any liquids that blow by that your primary doesn't catch, you hopefully catch it in your last chance and it dumps back into the tanks as well.
From your last chance separator, liquids that are dumped out of the primary separator dump into a horizontal three-phase.
And we do run burners on ours, so it is nice during the winter if we have paraffin problems or, obviously, water freezes in the winter, we can run a little heat and we could try to keep our wells going in the winter by running self-contained vessels with heat.
That's where your separation of your oil and water occurs is in your three phase. From there it dumps—your water, obviously to your water tank, and your oil to your oil tank. We use kind of a box system with some weir nipples, so we can adjust those levels a little bit.
If we're getting a little bit too much water in our oil or oil in our water, it has a little bit of adjustment.
Kyle & Curtis
Jobey tells us what a pumper would do when he walks through to check a site like this.
Jobey
Primarily he'll start walking through the equipment. He'll check the dumps on the primary separator, start checking pressures. They'll tell you a lot of times if you have an obstruction anywhere.
You'll look at your liquid levels on your separators. If you have just, for instance, your primary separator, if you look up at your sight glass and there's not a liquid level in it, more than likely you've got some kind of trash in your dump, or your dump is washed or there's something keeping that dump from seating.
Because with normal operations, you would have a fluid level somewhere in that sight. So that's a pretty tell-tale sign that there's an issue going on with the dump or dump controller, or it needs rebuilt, or sometimes you can just hit it with a good shot of gas and flush it, and you get some rubber pieces or trash that come out of it.
Then the dump will start seating and you should start seeing your level come back up within a normal operating area.
Kyle & Curtis
We cross the stairway over the berm to get closer to a vessel called a three-phase separator. It’s a horizontal cylinder, and it looks like a really large propane tank—about 10 feet long and 5 feet in diameter.
He says on this separator the dump valve is really important to watch, but you can also watch your data and spot trends that may indicate a problem.
Jobey
Then from there they'll usually go through their three-phase equipment, and you could look at the same thing there too, because we've got two different dumps coming off it—one side for your oil and one side for your water.
So they're looking at levels there too and checking it to make sure their dumps are holding correctly. Because obviously if we lose pressure our dumps aren't going work because we have to have the pressure to force the liquid through.
We've had some issues before too, we'll cut a dump valve or something like that, and we'll lose pressure on our vessel. Then things aren't gonna dump and go where they're supposed to go, and a lot of times you can catch that through trends and data and reporting and looking at the fluid in your tanks.
For a water tank trend, you don't normally gain a whole lot of oil in it, but say you look at it one morning and you've gained three feet of oil in your water tank overnight. Well, that's probably a sign that you've got some separation issues caused by a dump controller, or even gel or foam.
From there it could be several different things, but it's a sign saying, "Hey, we're having troubles here."
Kyle & Curtis
So if they spot a problem, like too much oil in their water or visa versa, what’s the protocol? Would they have to shut down that particular vessel?
Jobey
We would probably continue running through it at that point, so we could see what it's doing or not doing.
If your vessel's still "alive" you can troubleshoot it.
A lot of times you'll walk up to your sight glasses and say, "Okay, well, I have no oil in the oil side of my vessel, so that's probably a sign that I'm losing gas through there."
And then, then from there, you can rebuild the dump valve or, you know, if the body's cut, you may have to replace it.
But say you walk up there and you have oil in both of your sight glasses, then you could look at maybe your weir nipple, or something like that is, is plugging up.
And out in this area, you know, there's a lot of issues with sand. So you'll get sand kind of clogging up stuff and sometimes you can, you know, gel and foam, you could do stuff chemically to treat it, but sometimes you have to isolate it, turn out of it and manually remove it.
Then you bring in some roustabouts or a crane, depending on how the vessels are positioned, or a backhoe. And it'll pull it out and you bring some trucks in, usually one with water to jet and another truck to suck it up and clean it up, and you'll manually remove all your sand.
Or it may, you know, sometimes it might be easier to chemically treat something, but it's more cost effective to manually remove it.
Kyle & Curtis
OK, now the oil, gas, and water have been separated. Jobey explains where these resources going.
He points to the massive storage tanks on the north side of site.
Jobey
They're going into tanks, and tanks come in several different sizes. We use a lot of 400-, 500-, and 800-barrel tanks for storage. And it's onsite storage.
And then from there you have a couple different ways of doing things. On this path specifically, our water actually goes into a water gathering system with a water transfer pump.
That works on a start and stop level that you could change. So you can set your pump levels to on and off, kind of whatever you want. And, and it goes into a gathering system that goes into a disposal.
Our oil is actually LACT here from our holding. We have a LACT unit on site that starts up, and it tests the quality of the oil. And then if it's good enough to send, it pumps it down a pipeline that goes really across country.
It ends up in Cushing, so it's nice, but not every site's like that, depending on geographically where they're at and how cost effective it would be to run your water transfer lines and your LACT lines.
We have a locations that are just trucked, just basic. You have a water truck come in and they get a load of water and leave.
Most of our water we share. Most of the water-hauling companies can see what the levels are in our water tanks, and it helps us out, not having to call in a bunch of stuff every day. And then it helps them be cost effective too.
A load of water is usually 120 or 140 barrels, so that way they don't show up and there's only 80 barrels here. You know, they can maximize their load.
We do call our oil in, because if your oil's not clear enough or you get a little too much water in your oil, they'll reject it and they charge you for that rejection.
So we check our oil manually before we call it in. How that works is there's a water-finding paste you can put on your gauge line, and it'll give you a really good idea of how much water is in your oil. You're allowed a certain tolerance of water in your oil, but that's very low and it all settles out.
Your water stays in the bottom and your oil sits on top, so you want to make sure that your oil is good enough to sell before you call it in.
Not only because if it is rejected it costs you money, but then you're also backed up. You know, you don't stop producing oil just because they don't come and get it.
Kyle & Curtis
In episode 2, we talk to Jobey about what technological developments Jobey has seen, seasonal differences, what he looks for when hiring a pumper, and what he enjoys most about his work.
Jobey
There's a lot of cool stuff you see being out here. You know, growing up I don't ever remember seeing bald eagles and, and nowI probably see one every two weeks.