Vertical separators are one of the most used vessels in the energy industry.
Scrubbers, knockouts, treaters, and gun barrels are all forms of separators.
In this video, we introduce you to the basics of two types of vertical separator:
- A two-phase vertical separator separates gas from liquids.
- A three-phase vertical separator separates the gas from oil, and oil from water.
How Does Separation Occur?
Separation happens in many ways and for a variety of reasons.
Resources come to the surface in many forms and combinations. Sometimes separation adds value to the resource, and sometimes we separate components for safety reasons.
Nature helps us in the separation process. Often, specific gravities of resources are all that is needed to facilitate separation. But they need enough time in a steady state to do so.
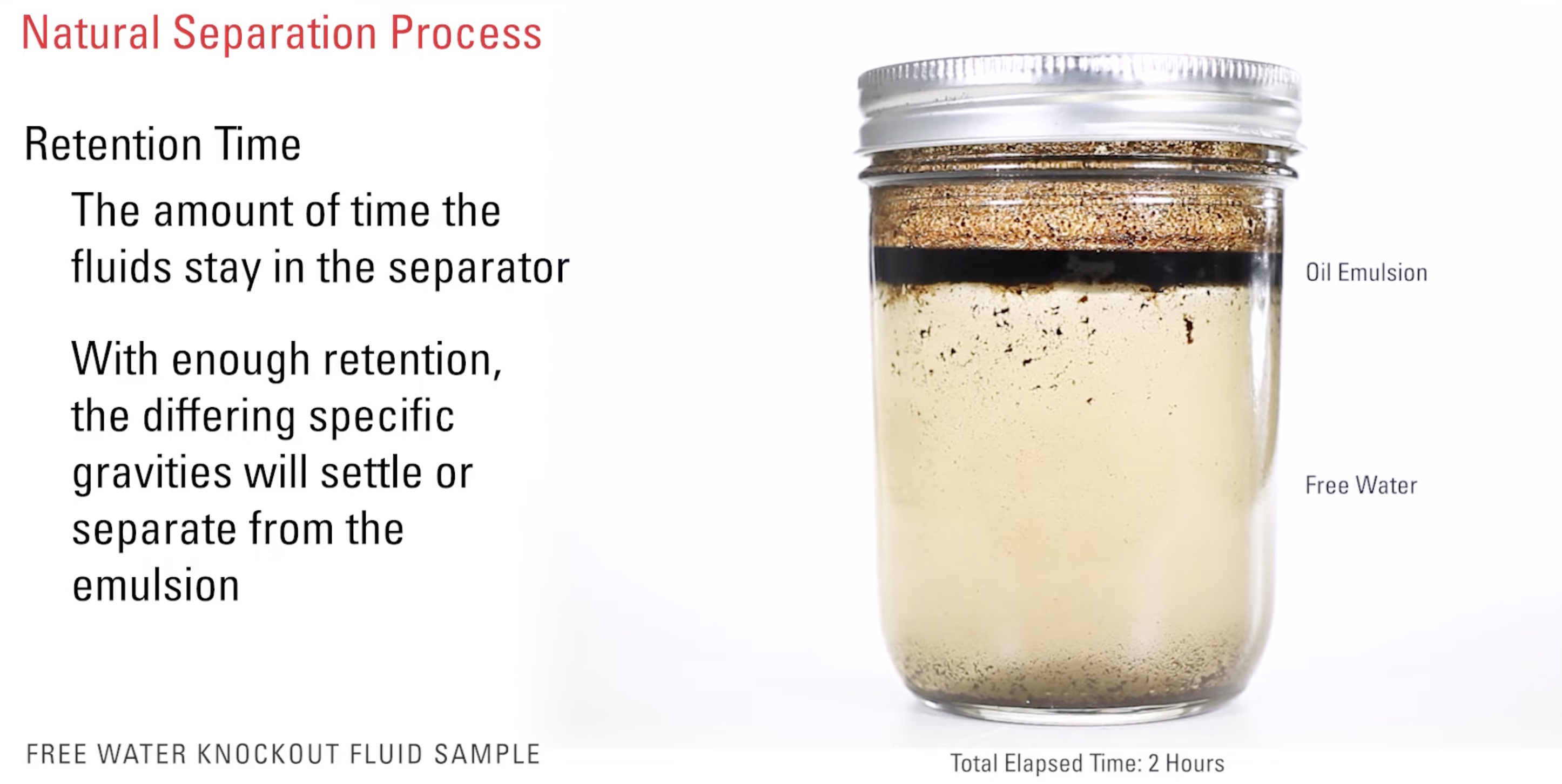
Retention time is a big factor in the separation process. Retention is the amount of time a fluid stays in a separator. With enough retention, the differing specific gravities will settle or separator from the emulsion.
Watch: 6 Ways to Separate an Oil and Water Emulsion
Over time, the fluids separate as they move from the inlet side of the separator to the outlet.
Sometimes producers may use devices like diverter plates, wave breakers, mist extractors, and weirs to encourage separation.
While initial separations happens in upstream production, all three sectors of the energy industry—upstream, midstream, and downstream–incorporate separation in their processes.
Size, Phases, and Pressures of a Vertical Three- and Two- Phase Separator
Producers consider size, separation capabilities, and accessibility to the internals when specifying separators.
Separation takes place when the makeup of a well stream is not meeting the customer's requirements. There are guidelines to help producers decide the extent of separation needed.
Here are a few pictures of a few styles of separators:
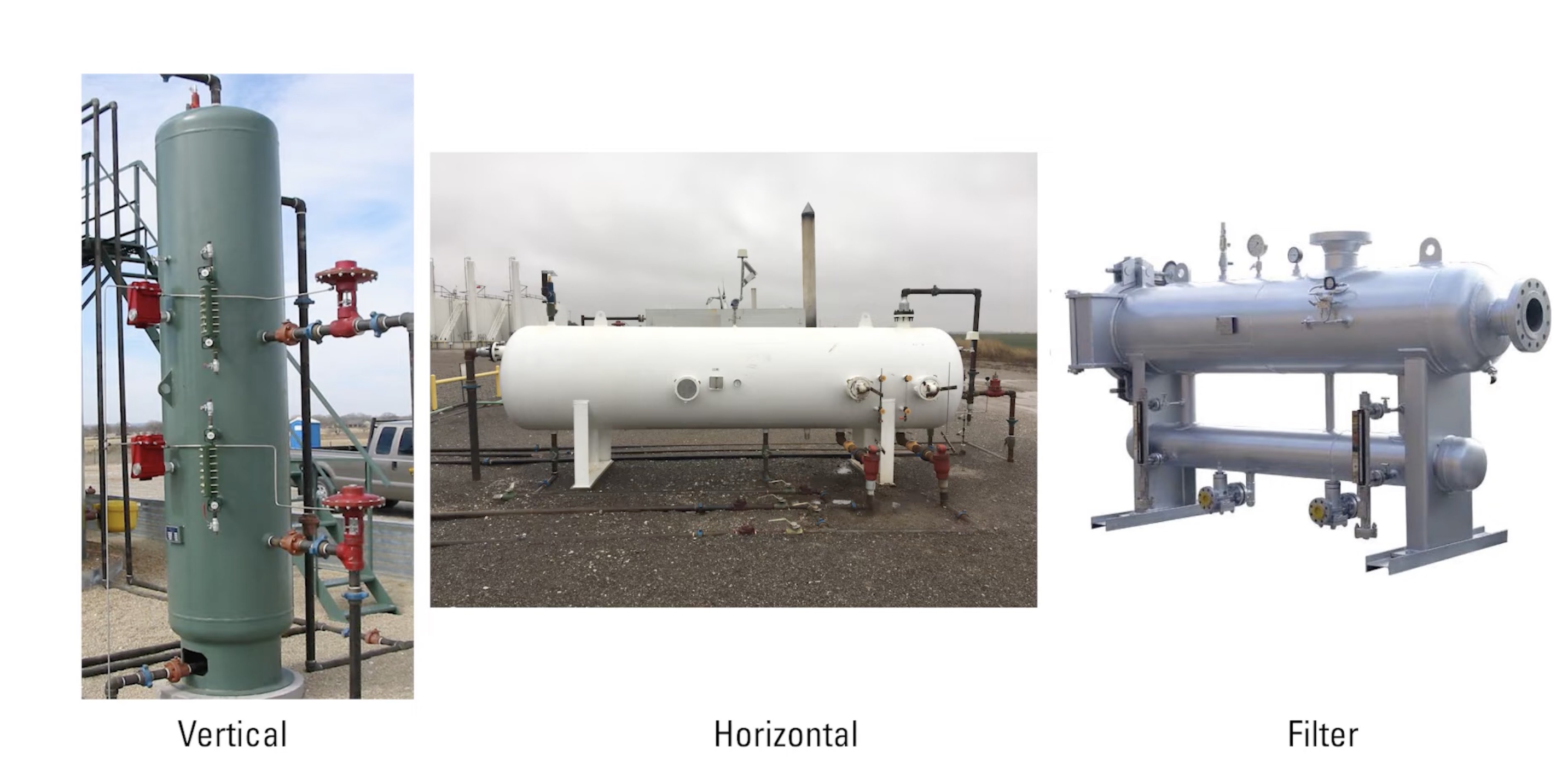
The customer's needs determine what type of vessel the equipment manufacturers make.
The size, working pressure, separation capabilities, accessibility to interns, and whether it's horizontal or vertical can all be factors that determine how a separator gets built.
Again, two phase means we are separating gas from liquids.
Three phase means we go a step further and separate:
- Gas from Oil
- Oil from Water
Separators may be high or low pressure. Anything under 500 PSI is considered low pressure, while anything above 500 PSI is considered high pressure.
Kimray provides different options for the controls on these vessels for both high pressure and low pressure.
Pneumatic Controls for Vertical Separators
Pneumatic controls use some form of gas to operate and control. These gases can be the natural gas produced from the well, air supplied by an outside source like a compressor, or compressed liquid nitrogen.
The quantity and quality of gas is important when choosing pneumatic controls. The process may also require pneumatics.
For example, metering fluids usually requires pneumatic controls to maintain a level of accuracy because they can be opened and closed quickly.
Mechanical Controls for Vertical Separators
If the operating pressure is low enough, mechanical controls are a great choice. We define mechanical controls as any device that uses levers and linkages to operate.
Mechanical valves don’t use gas to operate and therefore don’t emit gas under normal operation. This makes them a good option for operation in enclosed buildings or if you are looking to mitigate emissions.
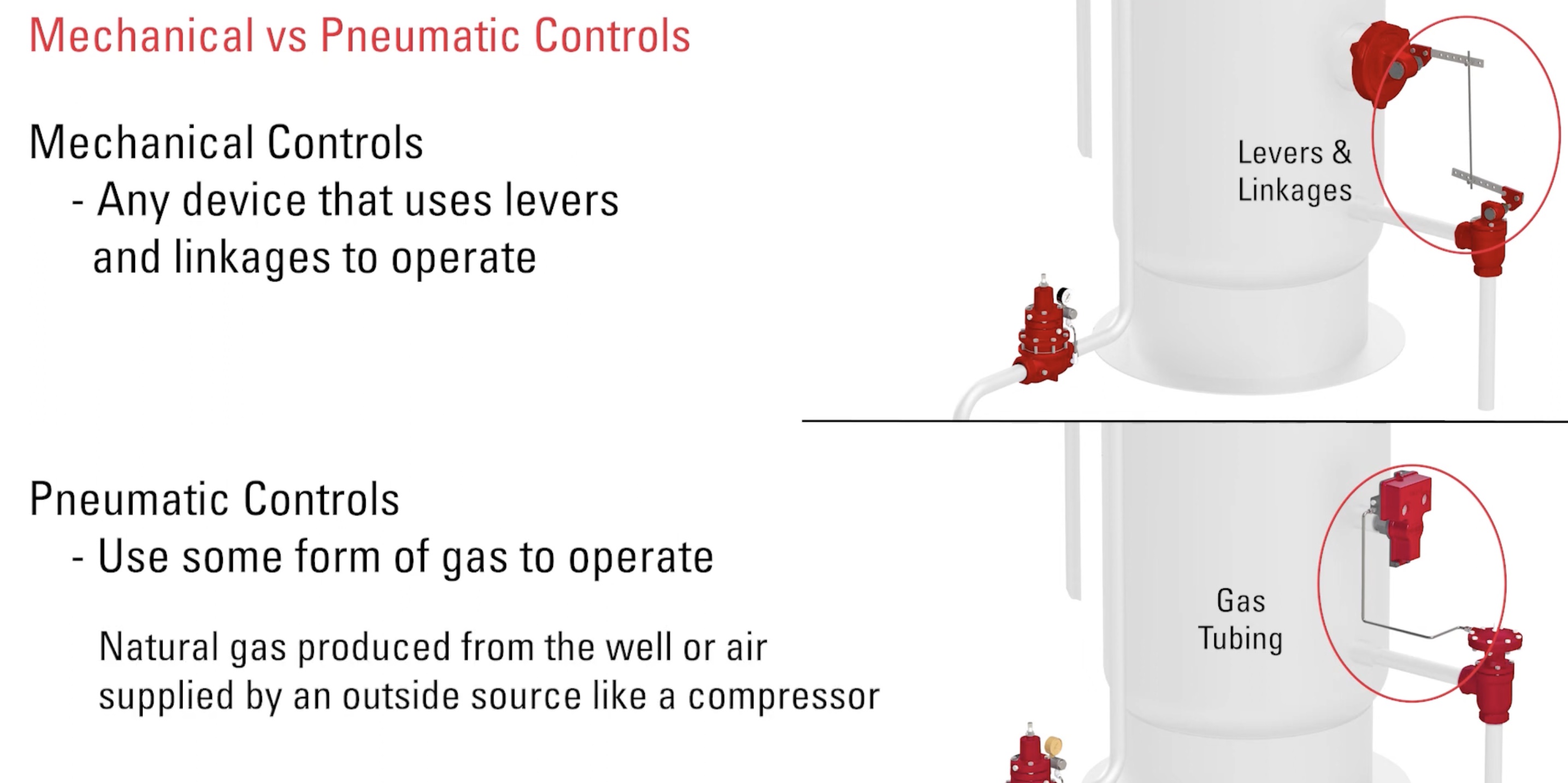
To speak with an expert about controlling your three-phase or two-phase vertical separator, contact your local Kimray store or authorized distributor.