Natural Gas Compressors work by mechanically increasing gas pressure in stages (or steps) until it reaches the desired delivery point. The starting pressure and the desired ending pressure will determine how many stages a compressor will have.
In the video above we cover the main types of natural gas compressors used in our industry and explain the differences between low and high pressure compressors.
Why Do We Compress Gas?
Gas compression is used in every sector of our industry when conditions do not normally exist for various processes to take place.
Producers compress natural gas for a number of reasons.
- Upstream: producers often use compression to inject gas back into the well to aid in lifting liquids to the surface. They also use it to compress low pressure gas off tanks, control devices and other equipment to help dispose of fugitive emissions (VRU).
- Midstream: In the midstream, compression is used to move gas from one location to the next through miles of pipe.
- Downstream: In the downstream sector, it aids in the removal of liquids to meet consumer and safety requirements.
Components of a High Pressure Single Stage Compressor
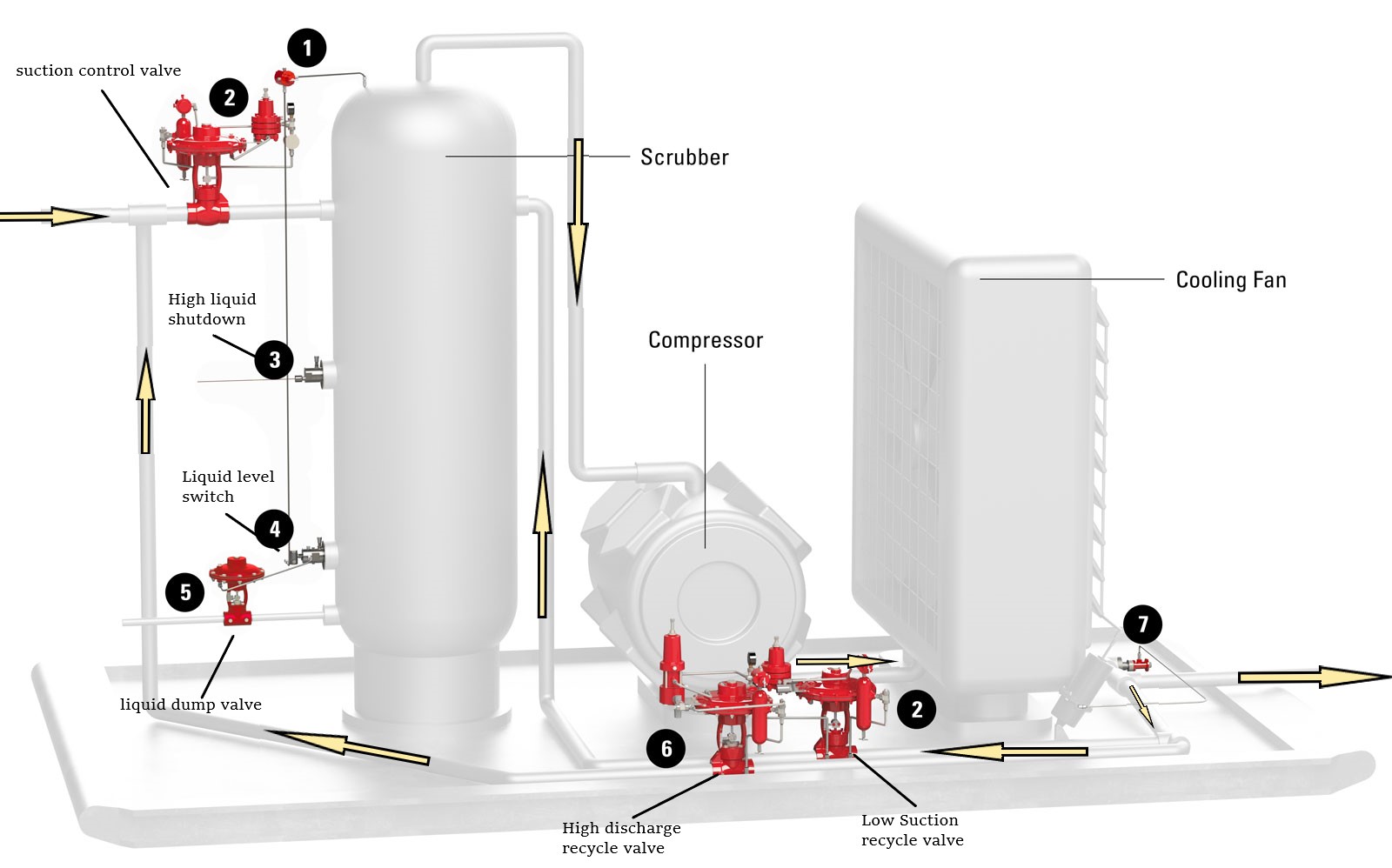
This is a simplified rendering of a high-pressure single-stage compressor. The red components are Kimray products that are used on a high pressure system—meaning anything with a working pressure above 300 PSI.
Gas flow comes in through the suction control valve and into the scrubber. From the scrubber it goes to the compressor then through the cooling fan and out the discharge.
If the suction pressure drops below setpoint, the low suction recycle valve will open and pressure will go to the scrubber.
If the discharge pressure goes above setpoint, the high discharge recirculating valve will open and send pressure to the upstream of the suction control valve.
What Types of Compressors Are Used?
The oil and gas industry uses two main types of compressors: reciprocating and screw.
Reciprocating Gas Compressor

The oil and gas industry uses two main types of compressors: reciprocating and screw.
A natural gas reciprocating compressor uses pistons and positive displacement to compress the gas. Gas enters the manifold, flows into the compression cylinder, then discharges at a higher pressure.
Flow Path
In the video, we show the inner workings and the flow path of a 3-stage reciprocating compressor. The inlet flow, or “suction side,” of the compressor starts at 30 psi and 80°F. It enters the inlet scrubber and any free liquids fall out. There are three stages of compression on a reciprocating compressor.
Compression Stage 1
At the first stage of compression, the pistons will compress the gas to 155 psi and the temperature will increase to 260°F. As it exits the first stage it goes into the intercooler. This cools the gas to down to 120° F. The heating and cooling of the gas along with the compression makes more liquids fall out of the gas. From here it enters another scrubber so that liquids can fall out.
Compression Stage 2
The second stage of compression increases the pressure to 490 psi and the temperature also heats up to 270°F. from there it’s back through the cooler to get the temperature back down to 120° F. with more pressure and cooling there’s more liquids that will fall out in the last scrubber.
Compression Stage 3
The third stage of compression gets the pressure up to 1200 psi and 240° F. Once again, the hot gas will go through the cooler and exit the at the discharge at 120°F. Some producers will run the compressed gas through one last scrubber to give any remaining liquids a place to drop out.
Screw Compressor
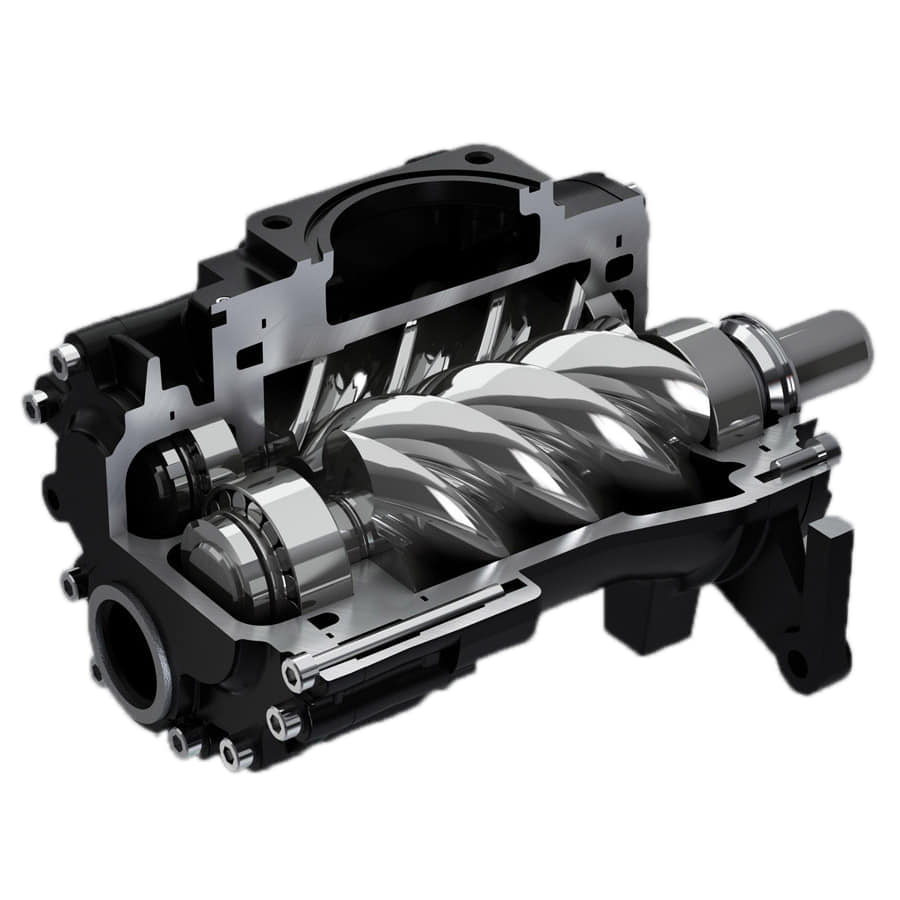
A screw compressor uses two meshing helical screws or rotors to compress the gas. Gas enters the suction side and moves through the threads. As it does it is compressed, and this compressed natural gas then exits at the discharge side at a higher pressure.
Screw compressors are typically used for lower pressure and lower volume like a VRU.
Natural Gas Compressor Sizes
Small Compressors
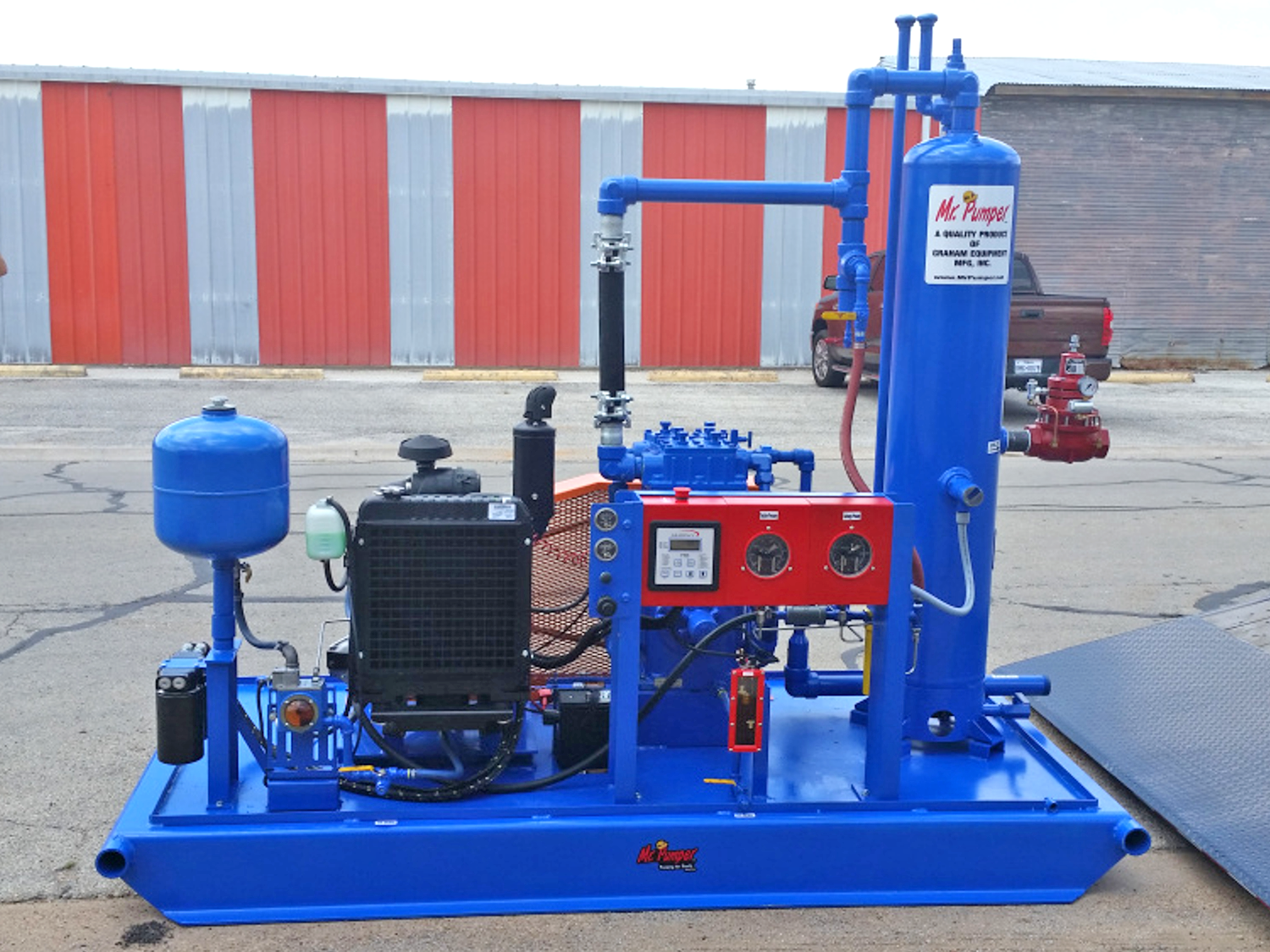
A small natural gas compressor like the single-stage compressor in the video may be used to gather fugitive gas and send it to the combustor or flare. It is known as a Vapor Recovery Unit or VRU.
Compressors aren’t only for natural gas. Many producers use air compressors to compress air and use it for instrument supply in order to reduce their gas emissions.
Medium Compressors
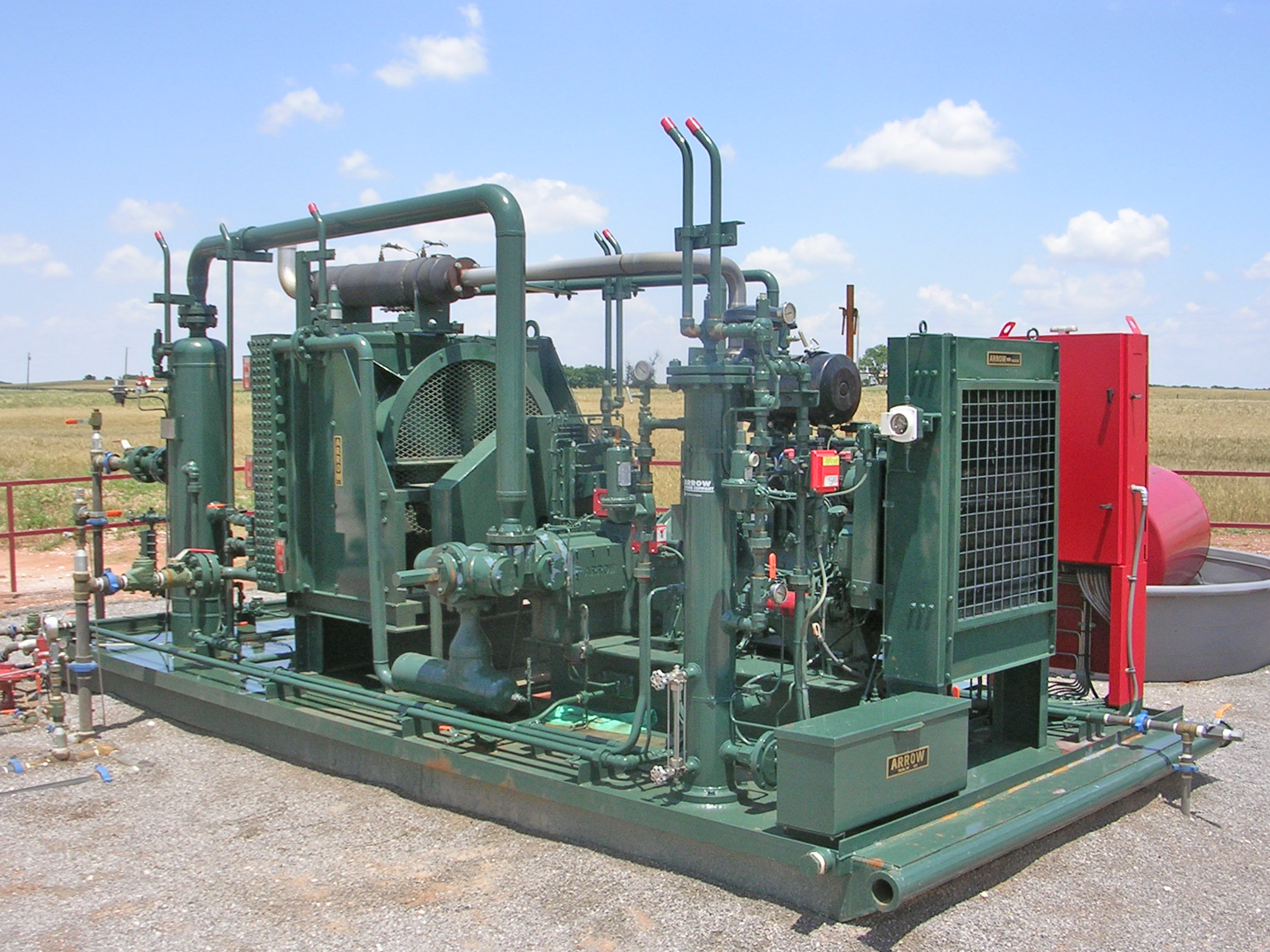
Medium-sized compressors may be found at wellheads (gas lift) or small gathering systems (pipeline), while compressor stations are the “engines” that power a pipeline. The size and number of compressors vary based on the diameter of the pipe and volume of gas to be moved.
Large Compressors
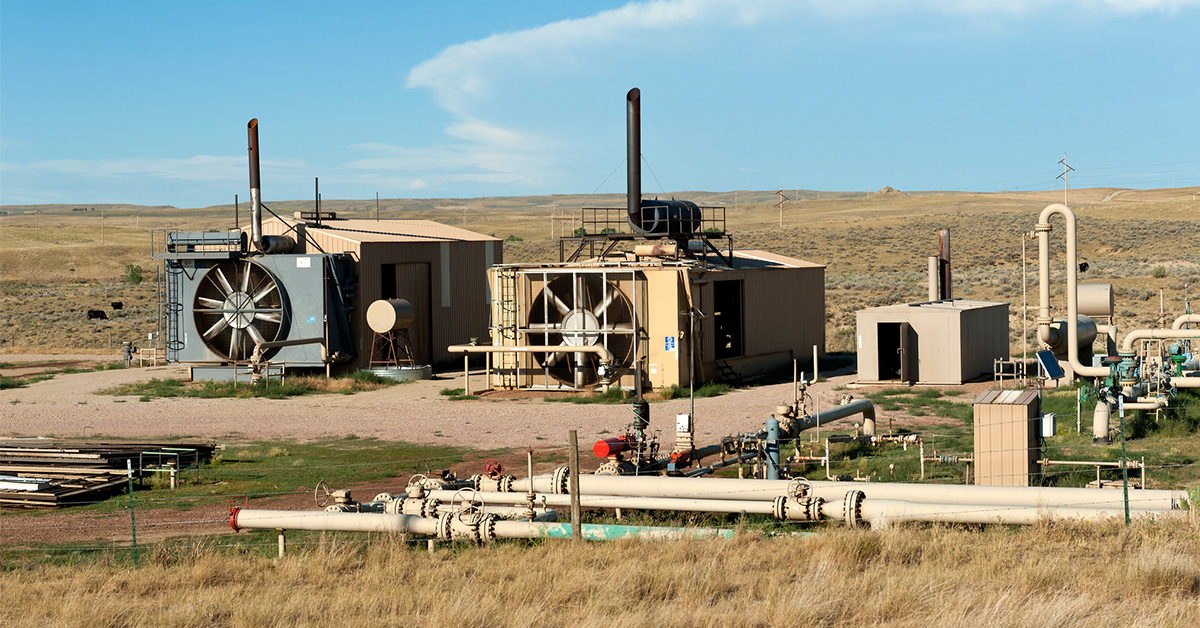
You’ll find the largest compressors at compressor stations. These are the “engines” that power a pipeline. The size and number of compressors vary based on the pressures and volume of gas to be moved.