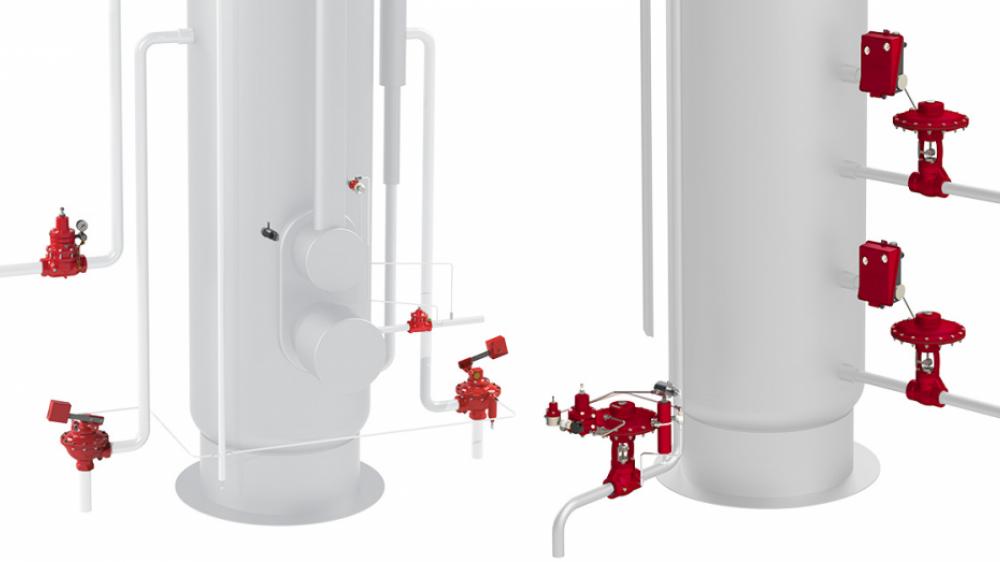
what is an Oil Separation System?
Drilled wells typically produce three elements: oil, gas, and water. Energy producers use a system of vessels, valves, pipes, and processes, to separate these elements.
In this article, we'll discuss 3 of the most common types of separation vessels:
- three-phase separators
- two-phase separators
- heater treaters
Three-Phase Separator
A three-phase separator separates process emulsion into three elements: oil, water, and gas.
This type of separator is often called a free-water knockout (FWKO), because it is used to “knock out” any water, which can cause problems such as corrosion. A liquid dump valve processes this water out, and it is either recycled or sent for disposal.
Three-phase separators come in vertical and horizontal orientations.
Two-Phase Separator
A two-phase separator separates the production emulsion into two elements: gas and liquid. A two-phase separator can be horizontal, vertical, or spherical.
The liquid (oil and water mixture) leaves the vessel at the bottom through a dump valve.
The gas leaves the vessel at the top, passing through a mist extractor to remove the small liquid droplets in the gas.
Heater Treater
When fluid enters a two-phase or three-phase separator, separation begins naturally due to the different specific gravities of the elements. A heater treater, as the name implies, introduces heat in order to accelerate this separation process.
A heater treaters houses an internal firetube, which uses supply gas to heat the produced fluid inside the vessel. Producers often use a low pressure control valve to regulate the temperature of the fluid. Heater treaters come in horizontal or vertical orientations.