An oil and water emulsion refers specifically to the fluid that comes directly from an oil and gas well.
When a well is produced, what comes to the surface is a mixture of crude oil, water, gas, and solids. After the gas has been separated from the liquid, the oil and water that remain must also be separated.
Emulsions in the oil industry are either classified as "water in oil" or "oil in water" depending on the ratio of the volume of liquids.
Gas brought to the surface is usually "wet gas" composed of dry natural gas like methane mixed with liquid natural gases like ethane and butane.
All these components are separated using multiple principles of separation to achieve the desired end products that are considered valuable.
In this video, we explain 6 principles used to separate an oil and water emulsion in the oil and gas industry.
1. How Heat Separates an Oil and Water Emulsion
When separating liquids from each other, heating to certain temperatures enhances separation. When the temperature of an oil and water emulsion is increased, the viscosity of oil is decreased. This lower viscosity allows the gas and water molecules to be more easily released. Heating oil emulsions also increases density between oil and water.
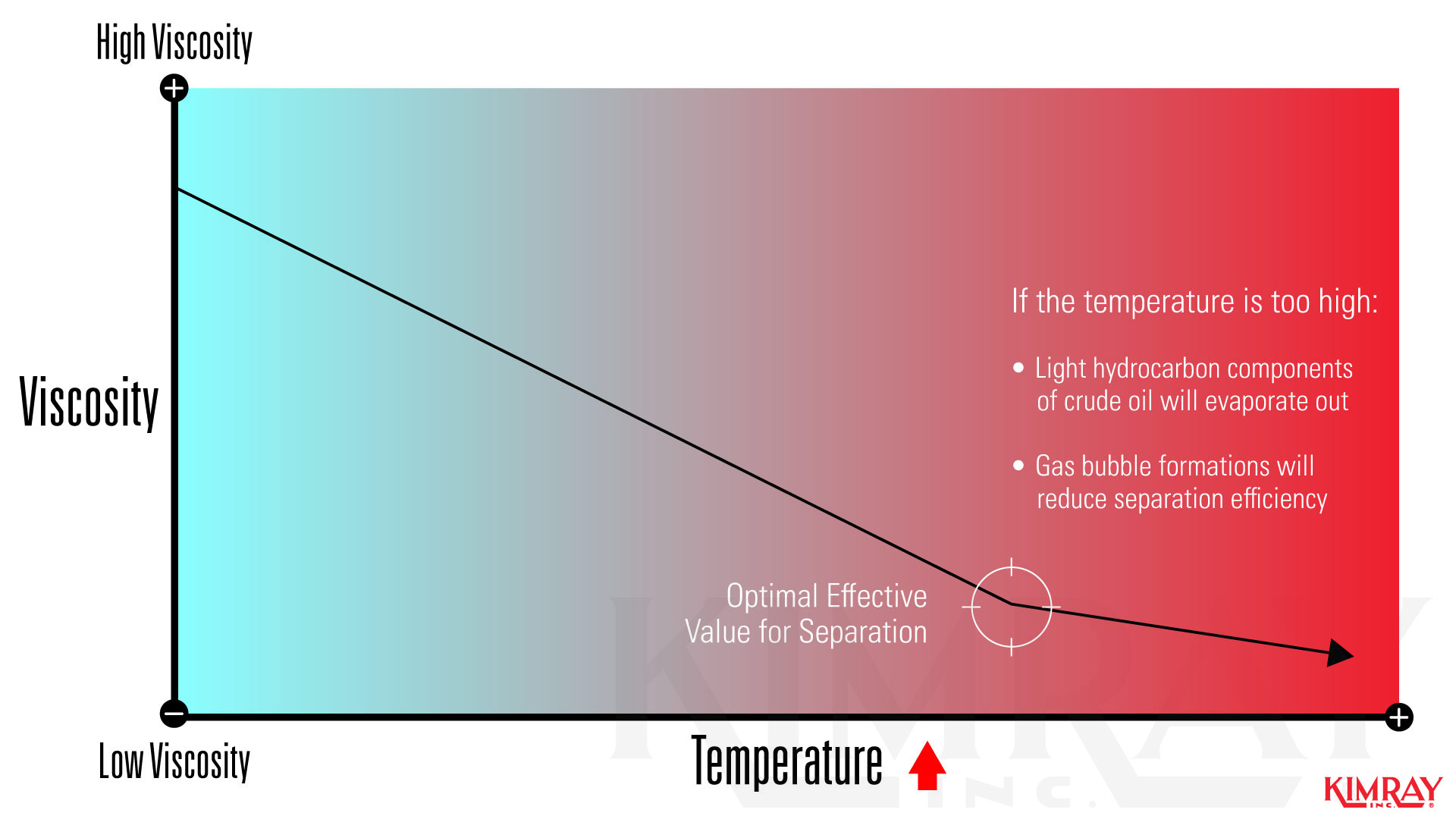
A heater treater is an example of a vessel which uses the principle of temperature change to aid in separation. For more on how a Heater Treater works, check out our Oil and Gas Equipment 101 learning path.
2. Gravity Separation
Gravity separation is the most widely used method for oil emulsion separation. The elements in the well stream such as oil and water have different gravities.
The density differences allow water to separate by gravity. With enough time in a non-turbulent state, the differing specific gravities will naturally separate into distinct layers.
To picture this, think of the emulsion as Italian dressing. If you let the dressing set, the ingredients will separate according to their different specific gravities. The olive oil will float on top because it is lighter than the vinegar, and the solids and other ingredients will fall to the bottom because they are the heaviest.
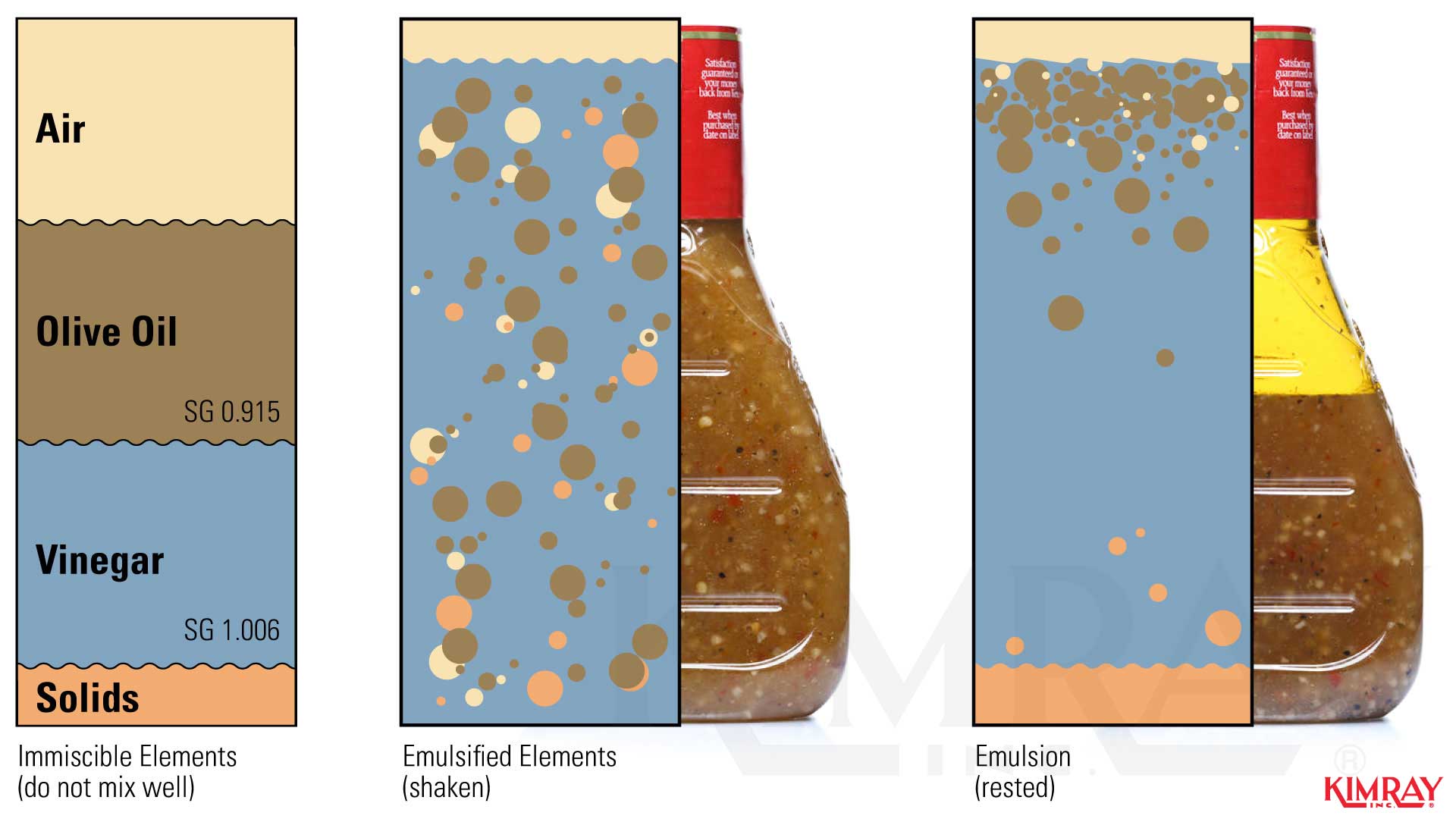
3. Retention Time
Separation occurs over time. When you reduce the velocity of a fluid, you allow the fluid a certain amount of time for it to be separated by gravity.
Retention time is the amount of time the fluid mixture stays in a steady or non-agitated state inside a separator. Longer retention time means more separation.
A larger-diameter or taller vessel will increase the retention time and allow more water to settle out by gravity.
In the video we show a sample of a mixture from a free water knockout, and you can see three layers: oil, water and solid, which separated over time.
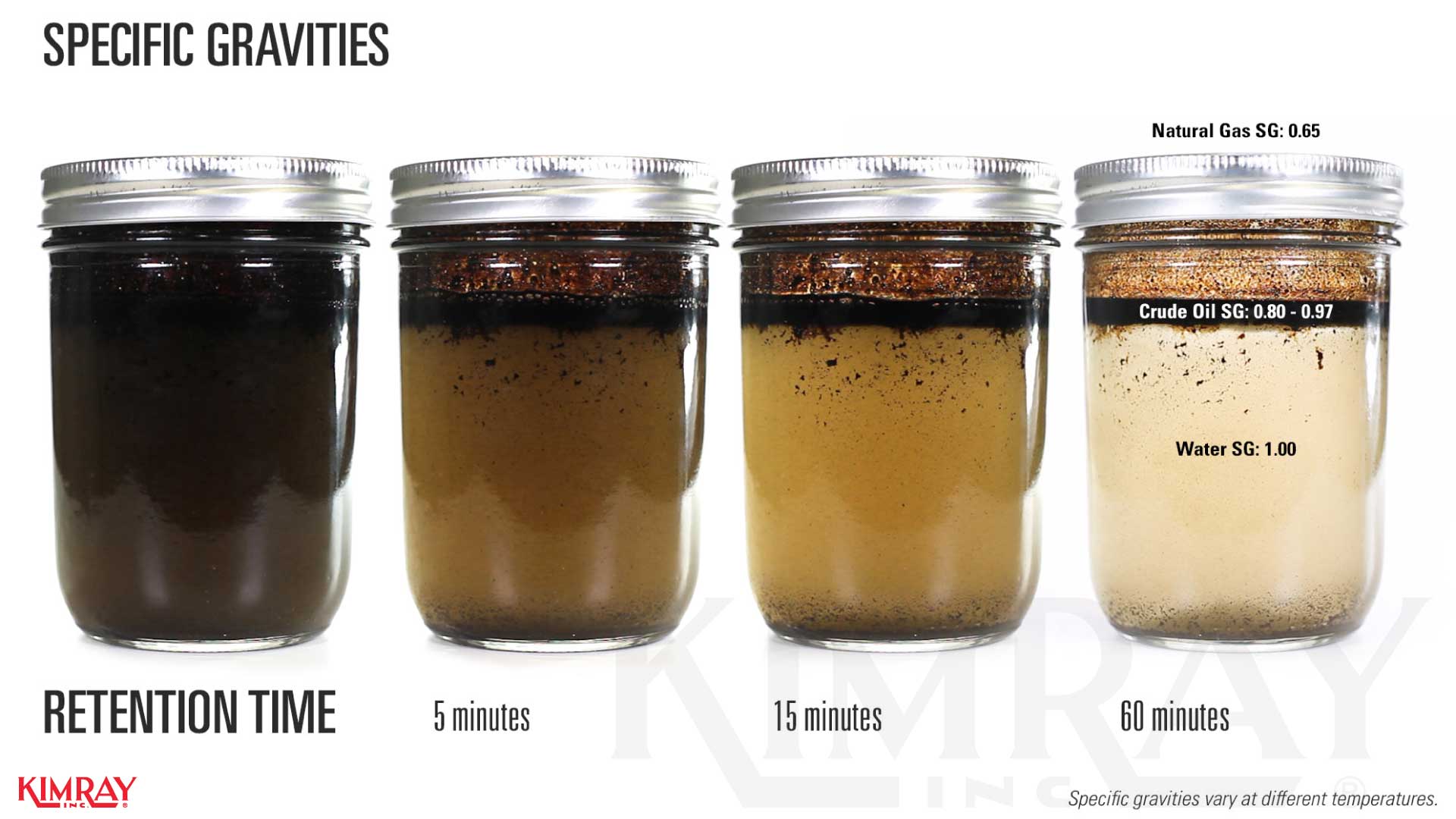
4. How Agitation Separates an Oil and Water Emulsion
A production fluid is agitated when it hits the diverter plate at the inlet of a vessel. The sudden impact on the plate causes a rapid change in direction and velocity which helps break the surface tension of the liquids and start the separation process.
There are many types of inlet diverters in separators, and the which is used depends on the attributes and volume of the well stream.
Agitation increases the probability that the liquid will coalesce and settle from the emulsion.
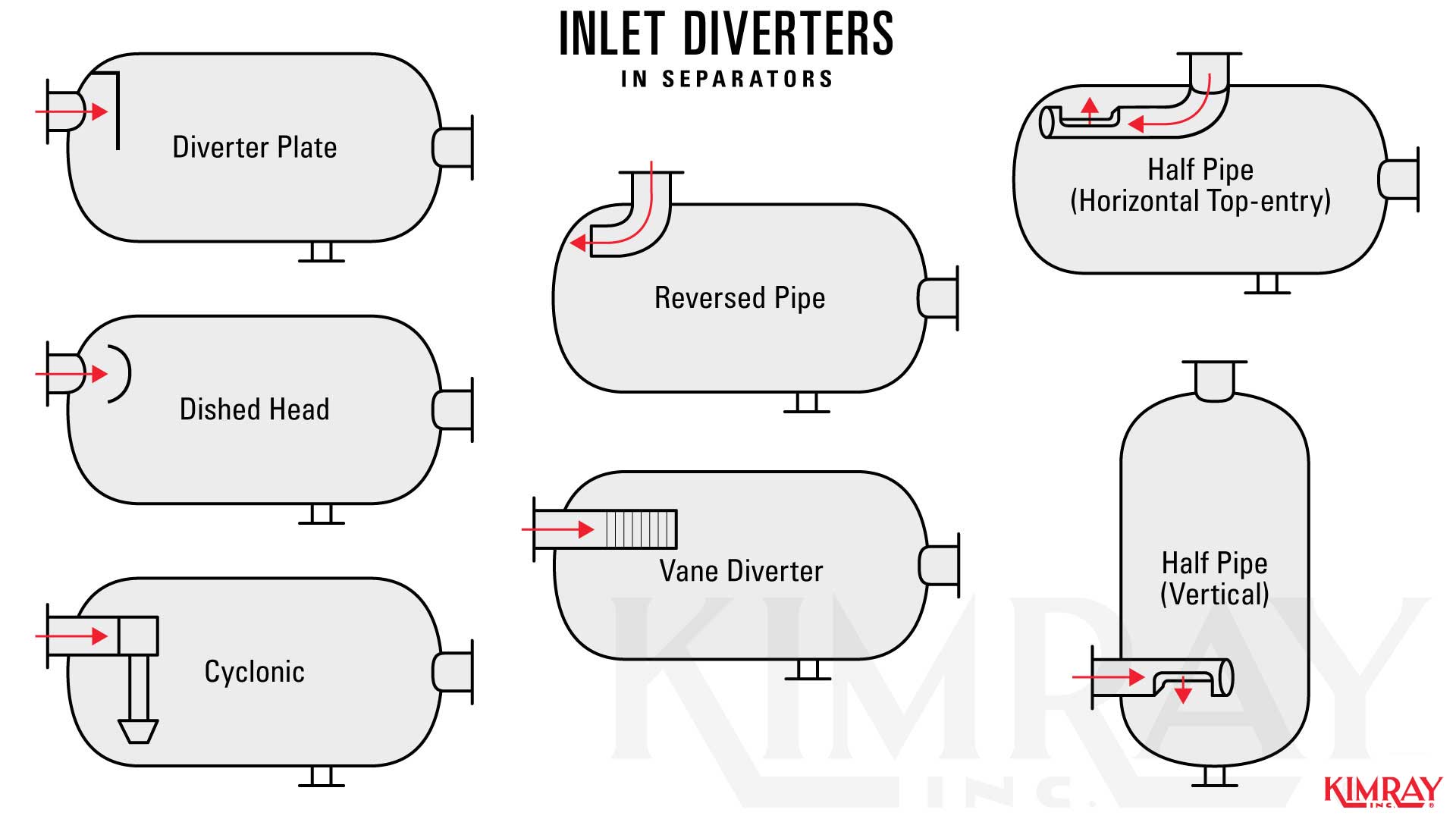
5. Coalescing
During coalescence, water droplets come together to form larger drops.
Picture yourself driving on a foggy morning. The fog tells us there is is a lot of moisture in the air, but it doesn't actually condense into liquid until it hits your windshield.
The same is true when gas hits a hard surface. This may be a diverter plate when it first enters the vessel, or a mist eliminator as it exits.
In vane-type mist eliminators, tiny droplets are removed from the vapor stream through inertial impaction. The wet gas is forced to change directions, causing mist droplets to strike the vanes and coalesce with other droplets, eventually falling.
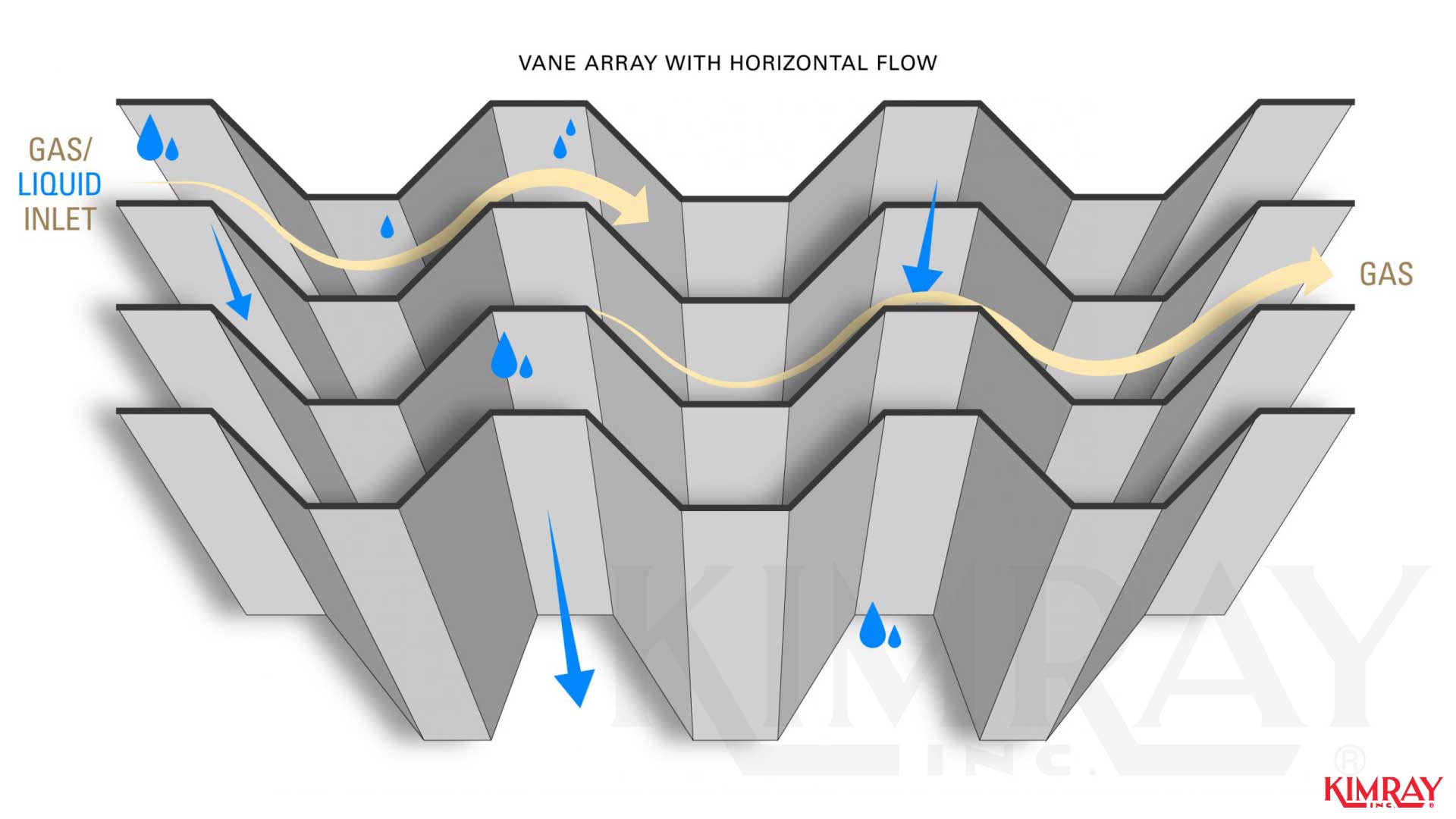
This inertial impaction also occurs in mesh-type mist eliminators.
Gas must flow around each strand of mesh, and when mist droplet strikes the filaments, they adhere and coalesce to form droplets large enough to fall.
Submicron droplets zig-zag through the close-packed fibers with "Brownian motion" and will eventually strike, adhere, coalesce, and drain.
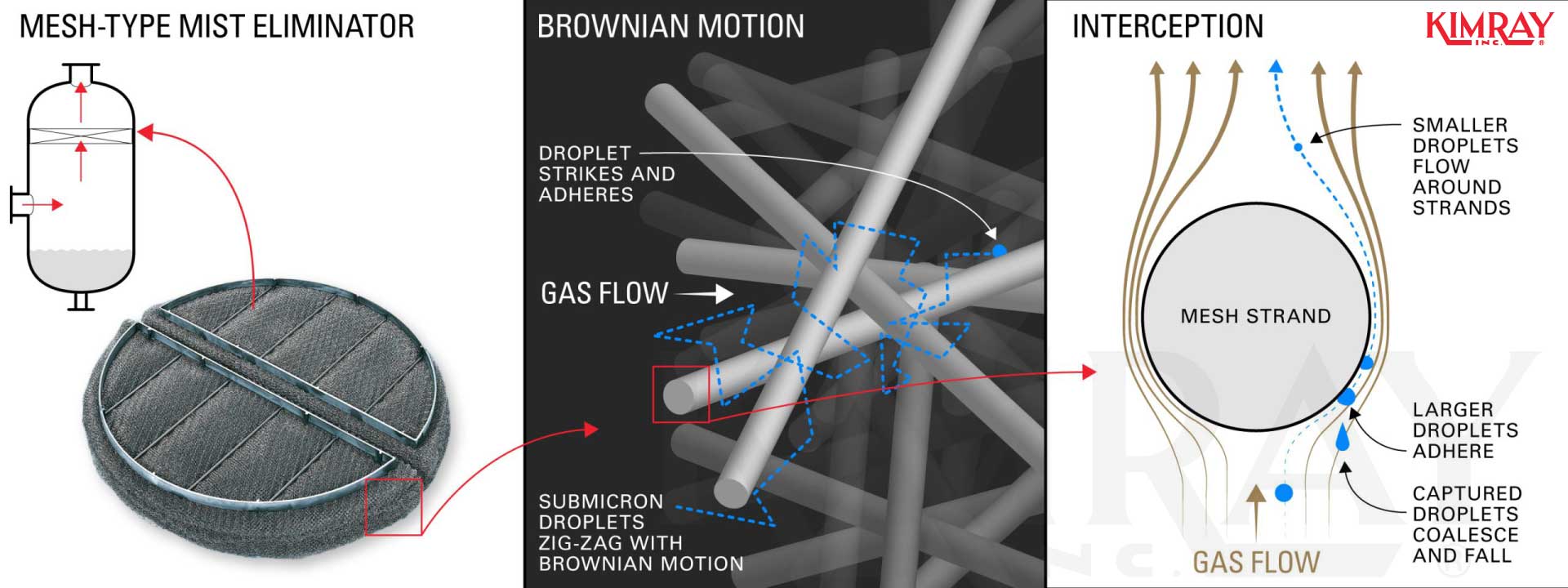
6. How Chemical Demulsifiers Separate an Oil and Water Emulsion
Treating fluids with demulsifiers aids the separation process. The chemicals move to the oil and water interface, weakening the surface tension and enhancing coalescence. Knowing which chemicals to use and the correct dosage can be complex, but the desired effect will minimize the amount of heat or retention time required for separation.