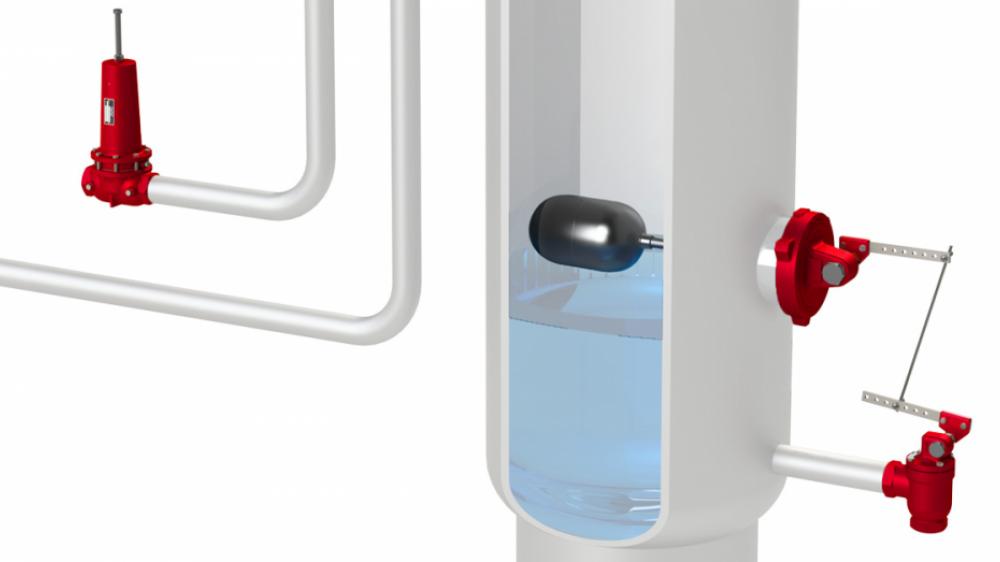
The Kimray Lever-Operated Liquid Dump Valve is designed to provide emissions-free liquid level control in vessels such as heater treaters, two-phase separators, three-phase separators, and free water knockouts.
In this article, we’ll explain how to adjust the dump valve and cover some troubleshooting scenarios. We’ll also provide a detailed torque calculator to help you select the correct size.
Adjusting the Dump Valve
A dump valve uses process fluid to balance upstream and downstream pressure. As part of a liquid level control system, the dump valve works with a trunnion assembly, float, and linkage rod.
Here’s how adjusting the linkage rod, lever bars, and float will affect the dump valve operation:
- Increasing L1 and/or Decreasing L2 will increase the amount of movement to the valve lever bar, but will decrease the torque applied to the valve lever bar
- Decreasing L1 and/or Increasing L2 will increase the opening and closing torque applied to the valve lever bar, but will decrease the amount of movement to the valve lever bar
- Increasing the Rod Length will increase both opening and closing torque applied to the valve lever bar, but will also increase the span of the liquid level (distance between high and low levels)
- Increasing the float volume will increase the opening torque applied to the valve lever bar
- Increasing the weight of the float will increase the closing torque applied to the valve lever bar
- Ideally the angle, θ, should be zero to maximize torque. The greater θ is, the less torque is applied to the valve lever bar for both opening and closing.
Troubleshooting: Dump valve is not opening or closing fully
The valve will either not open fully or not close fully due to the mechanical linkage or other physical impediment.
Solution 1
Make sure the float has full range of motion and is not being stopped short by the weld neck or any other obstruction. The best way to do this is disconnect the linkage rod and manually move the trunnion lever bar all the way up and down. If the weld neck is the obstruction, then you may need to have it cut to a shorter length.
Explanation: If the float is not able to travel its designed full range due to an obstruction, then the trunnion lever bar might not be able to move enough to fully actuate the valve.
Solution 2
If the valve is not fully opening, increase the distance between the two lever bars. Loosen one ball joint on the linkage rod and then move the lever bars slightly away from each other. Then re-tighten the ball joint. If the valve is not fully closing, do the same thing except move the lever bars closer to each other.
Explanation: Setting the lever bars further away from each other pushes the valve lever bar down further, causing it to close sooner. Setting the lever bars closer to each other lifts the valve lever bar up, causing it to fully open sooner.
Solution 3
If the float has full range of motion, change the connection points on each lever bar where the linkage rod is pinned in. Move the pin in the trunnion lever bar one hole over to increase L1 by 1?. Next, move the pin in the valve lever bar one hole over to decrease L2 by 1?. Keep doing this, one pin at a time, until it is enough to give full movement to the valve to fully open and close it.
Explanation: Increasing L1 or decreasing L2 increases the opening/closing travel of the valve compared to the up/down travel of the float inside the vessel. However, the drawback is that this will reduce the force applied to the valve from the trunnion.
Troubleshooting: Float isn’t floating
Even when the float is fully submerged in the bottom liquid, it won’t move up all the way, so the valve is not opening fully.
Solution 1
Change the connection points on each lever bar where the linkage rod is pinned in. Move the pin in the trunnion lever bar one hole over to decrease L1 by 1?. Next, move the pin in the valve lever bar one hole over to increase L2 by 1?. Keep doing this, one pin at a time, until it is enough to fully open the valve.
Explanation: Decreasing L1 or increasing L2 increases the opening/closing force to the valve. However, the drawback is that this will reduce the travel range, so the risk is that you won’t have enough movement to fully open or fully close the valve.
Solution 2
Replace the float with a larger volume float. Use the calculator to determine what size you need.
Explanation: More volume in the float creates more displacement in the liquid, which generates more upward force on the float to help push the lever down and open the valve.
Solution 3
Replace the float rod with a longer one, and/or lighter one. Use the calculator to determine what length/weight will work.
Explanation: A longer rod creates more leverage, so that the displacement force on the float generates more torque transferred to the valve. A lighter rod reduces the downward force on the float.
Solution 4
Add weight at the end of the trunnion lever bar to counterbalance the float weight. You may need to bolt on an additional lever bar to the end of the trunnion lever bar to get enough length that the added weight will generate enough counterbalance.
Explanation: Adding weight to the trunnion lever bar increases the closing force on the valve. However, the drawback is that it also decreases the opening force, so the valve might not open fully.
Troubleshooting: Dump valve is not closing
The valve isn’t fully closing even though the trunnion lever bar seems to be moving upward.
Solution 1
Change the connection points on each lever bar where the linkage rod is pinned in. Move the pin in the trunnion lever bar one hole over to decrease L1 by 1?. Next, move the pin in the valve lever bar one hole over to increase L2 by 1?. Keep doing this, one pin at a time, until it is enough to fully close the valve.
Explanation: Decreasing L1 or increasing L2 increases the opening/closing force to the valve. However, the drawback is that this will reduce the travel range, so the risk is that you won’t have enough movement to fully open or fully close the valve.
Solution 2
Add weight to the float or get a larger, heavier float. Use the calculator to determine what size you need.
Explanation: A heavier float generates more downward force on the float to help pull the trunnion lever bar up and close the valve.
Solution 3
Replace the float rod with a longer one, and/or heavier one. Use the calculator to determine what length/weight will work.
Explanation: A longer rod creates more leverage, which generates more torque transferred to the valve. A heavier rod increases the downward force on the float which helps close the valve.
Torque Calculator
Our easy-to-use Dump Valve Torque Calculator will help you determine what size controller, float, and valve you need for your specific conditions. Note that there are two tabs—one for two-phase operation and one for three-phase operation.
Download the Torque Calculator
For further questions regarding the Kimray Lever-Operated Liquid Dump Valve or any of our other products, contact your local Kimray store or authorized distributor.