Oil and gas producers use back pressure regulators to provide control of oil and gas production processes.
In this video, we’ll cover the ten most common applications for this regulator:
- 2-Phase & 3-Phase Separators
- Free Water Knockout (FWKO)
- Compressor: Low Suction Recycle
- Compressor: High Discharge Recycle
- Vapor Recovery Unit
- Dehydrator
- Flare
- Heater Treater
- LACT
- Back Pressure with Outside Supply
2-Phase and 3-Phase Separators
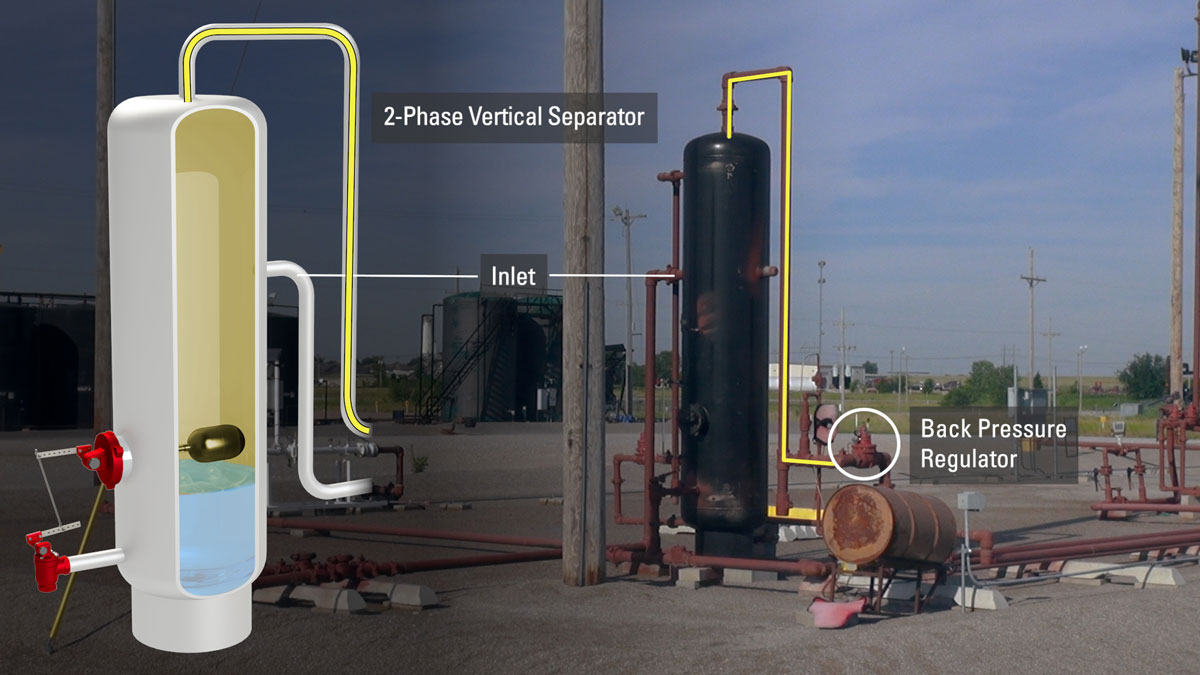
A 2-phase separator separates gas from all other liquids while a 3-phase separator separates oil, water and gas from each other.
Natural gas, being lighter than water and oil, rises to the top of the vessel where it begins to separate from the well stream. The natural gas flows through the outlet on the top of the vessel and into a Kimray back pressure regulator.
The back pressure regulator holds constant pressure on the vessel to allow it to move liquids to the next destination. Any gas pressure over the regulator's set point will be sent downstream for additional separation, gas treating or sales.
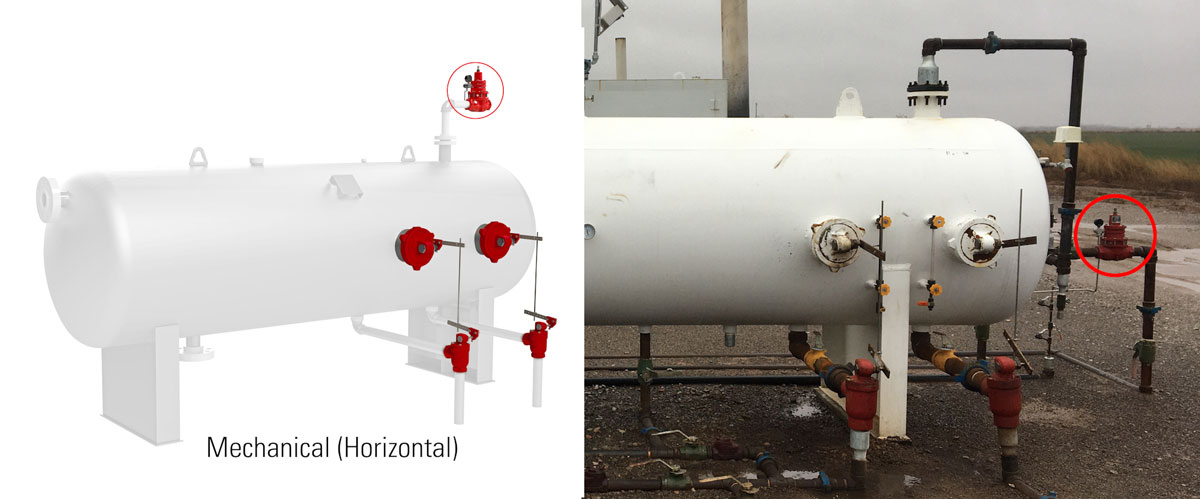
Free Water Knockouts (FWKO)
%20Oil%20Emulsion%20Outlet.jpg)
On a two-phase free water knockout, a spring loaded back pressure regulator can be used on the oil emulsion outlet. This is distinct from the standard back pressure regulator, which can only be used to regulate the flow of gas, not liquid.
On a three-phase vessel, a spring loaded back pressure regulator or standard back pressure regulator will be on the gas outlet.
In both situations, the Spring Loaded Back Pressure Regulator holds pressure on this vessel and allows the liquid to reach its next destination, making this a very important valve.
When the upstream pressure overcomes the spring tension in the regulator, the valve will open and send the oil emulsion downstream to be processed further.
%20with%20Kimray%20Products.jpg)
Low Pressure Compressors
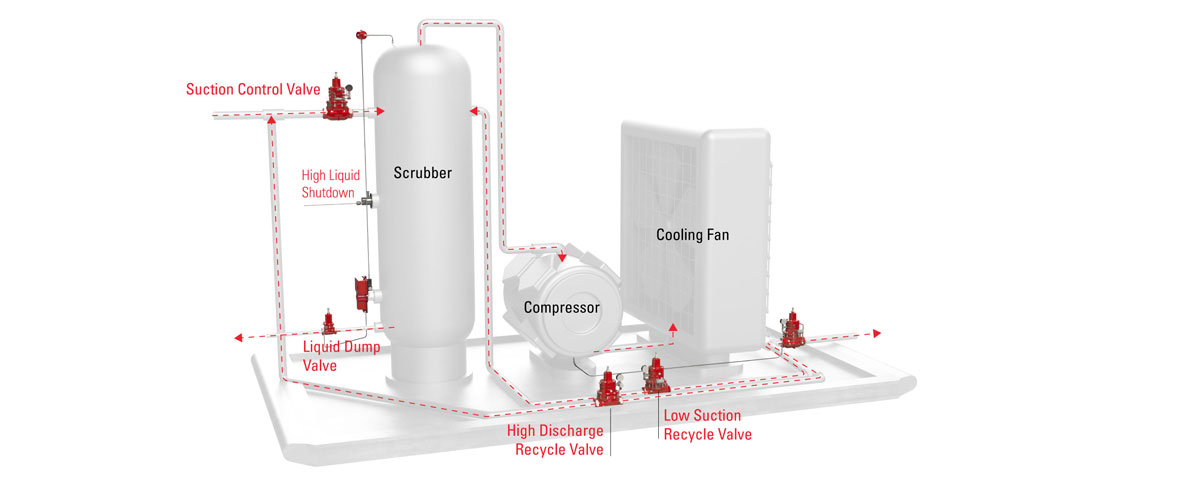
On a compressor, the back pressure regulator can be used as a Low Suction Recycle Valve or High Discharge Recycle Valve.
Low Suction Recycle Valve
If there is a shortage of volume or pressure of inlet gas, it can cause pressure to drop below the set point. When this happens, the low suction recycle valve will open, and pressure will travel from the compressor discharge back to the inlet side.
The compressor will continue to operate with the low suction recycle valve open until suction pressure returns. This low suction recirculation valve will prevent the compressor from shutting down due to low suction pressure.
High Discharge Recycle Valve
If the compressor discharge pressure rises above the set point of this regulator, the high discharge recirculating valve will open and send pressure to the upstream of the suction control valve.
This high discharge recycle valve will prevent the compressor from shutting down on high discharge pressure.
Vapor Recovery Unit (VRU)
.jpg)
The Back Pressure to Vacuum Regulator can operate with a vacuum on the downstream side of the regulator.
This vacuum is most commonly created by a Vapor Recovery Unit (VRU), which gathers gas from the low pressure vent lines of control devices. Producers use VRUs to lower gas emissions and increase efficiency.
Dehydrators
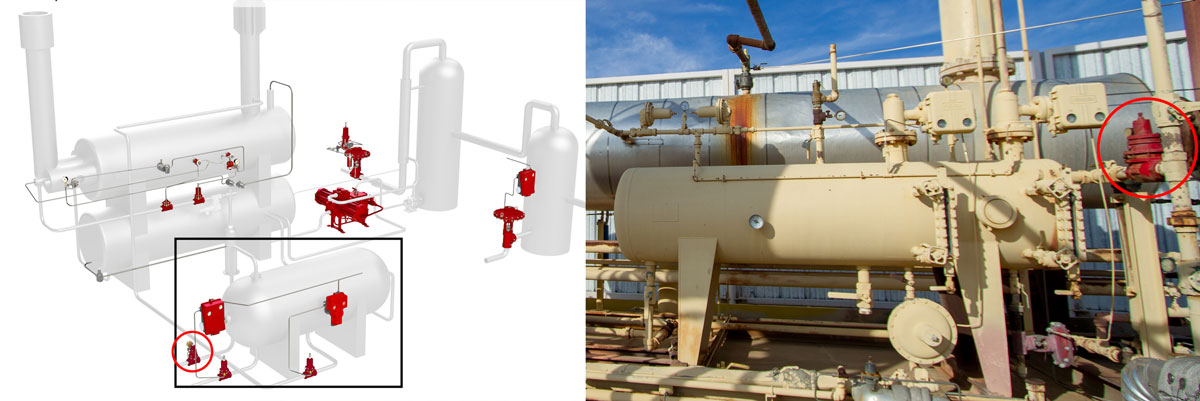
On a dehydration unit, the back pressure regulator can be used to hold back pressure on the flash separator. On a flash separator, the back pressure regulator is located on the gas outlet piping, meaning it will control the pressure inside that vessel.
Inside the flash separator, the separated gas travels along the top of the skimmer and passes through a mist extractor before exiting through a back pressure valve.
Flare Valves
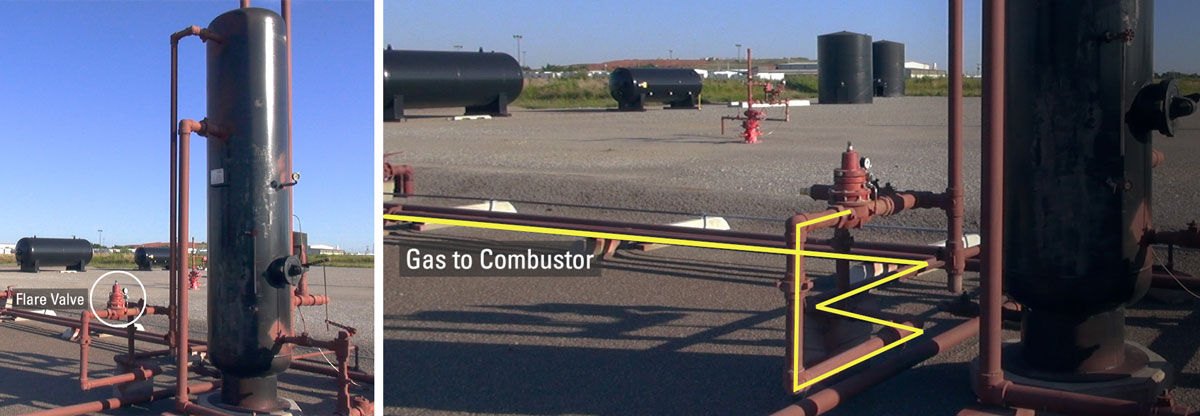
This back pressure regulator is installed in case there is maintenance on the sales line or if in the future they tie in a new well and pressure backs up on the existing location.
The flare valve is set at a higher set point than the sale valve. If that pressure set point is met, the valve opens sending the gas to a combustor or flare to be incinerated until the condition changes.
Heater Treaters
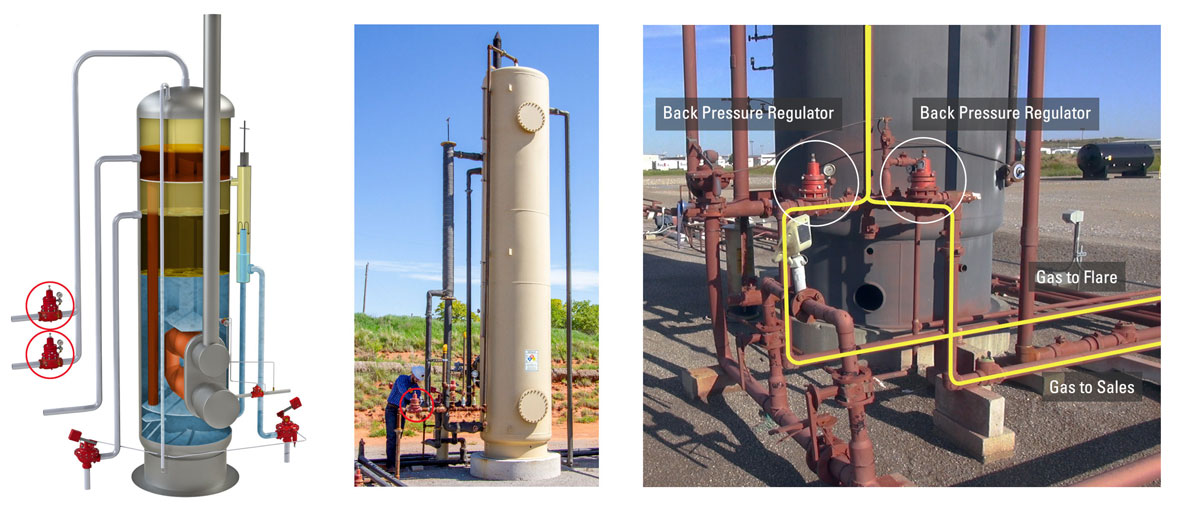
Back pressure regulators hold pressure on production vessels. This pressure creates the necessary force required to dump liquid out of the vessel and move it to the next process.
After separation of the oil emulsion occurs, the gas rises to the top of the heater treater, where it travels through the back pressure regulator. From this regulator the gas can travel to either a sales or flare line.
LACT Units
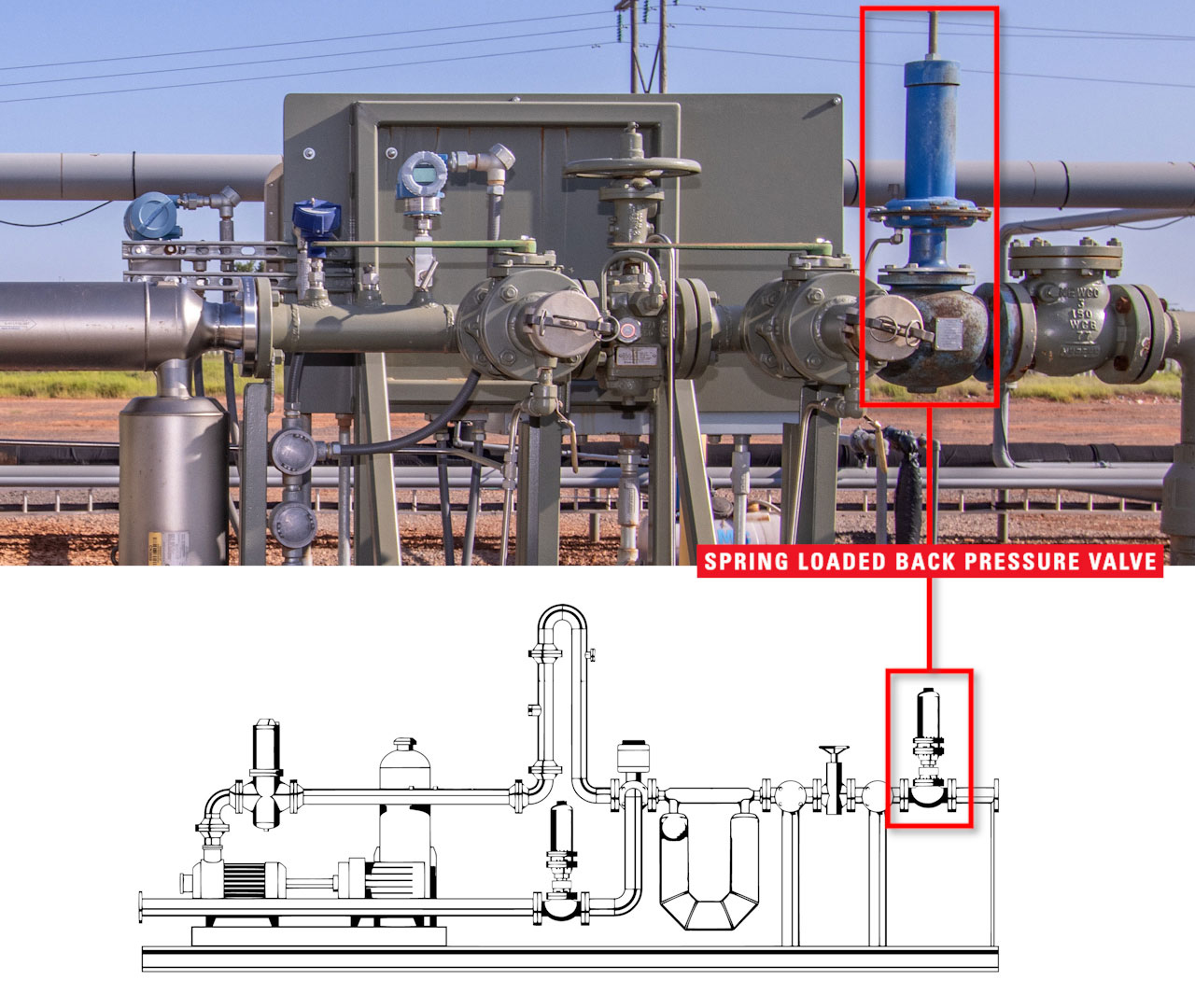
On a LACT Unit, a spring-loaded back pressure regulator can be used to hold pressure.
The oil moves through a back pressure regulator, which holds pressure against the LACT unit. This is typically a spring loaded back pressure regulator because it requires no supply gas to operate.
Kimray’s Spring Loaded Back Pressure Regulator can be used in this application but may be limited by its maximum set point and potential flow volume. Often, the oil travels into a midstream pipeline from the back pressure regulator and is operating at a higher pressure than what the Kimray valve can hold.
However, if downstream pressure is lower than the maximum operating pressure of the back pressure regulator, it’s a good option for this application.
Back Pressure with Outside Supply
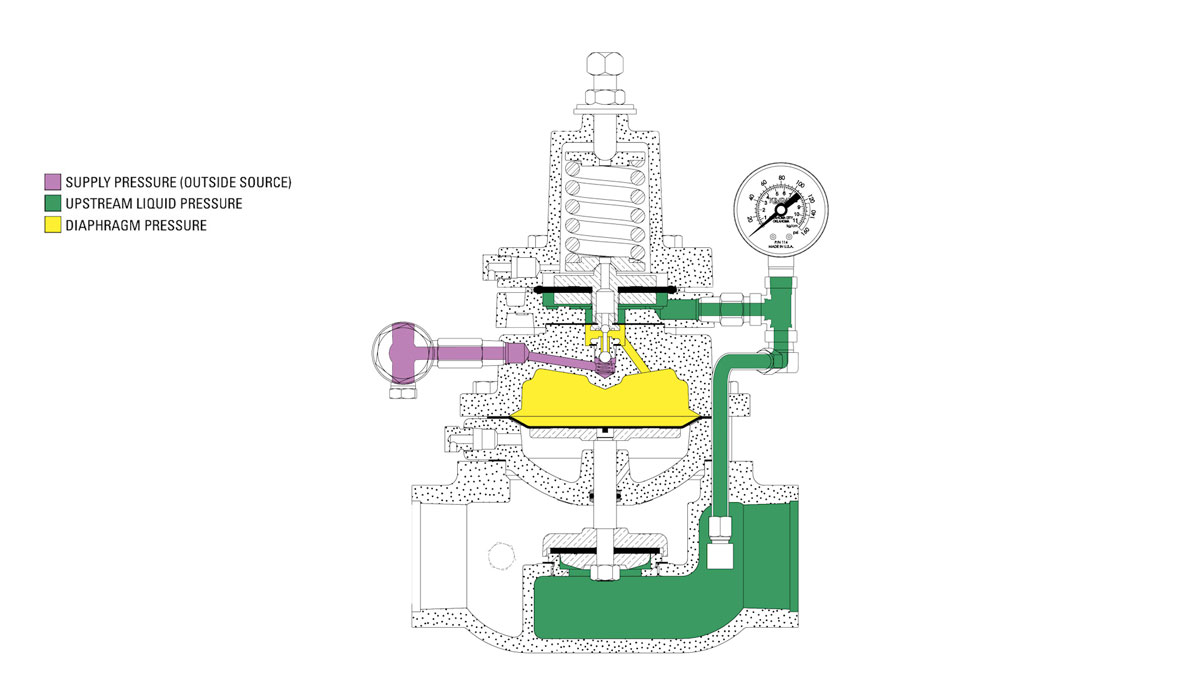
Where you are having issues regulating constant pressure with wet gas, you can replace the standard Back Pressure Regulator with our Back Pressure Regulator with Outside Supply in any of these applications, except the VRU. You may also hear this called a liquid back pressure regulator.
Using an outside source of supplied air or clean gas, this regulator can operate in wet gas conditions with no negative effects on the valve. The supply is completely isolated from the upstream and downstream sides of the regulator.
To speak with an expert about back pressure regulator applications, contact your local Kimray store or authorized distributor.