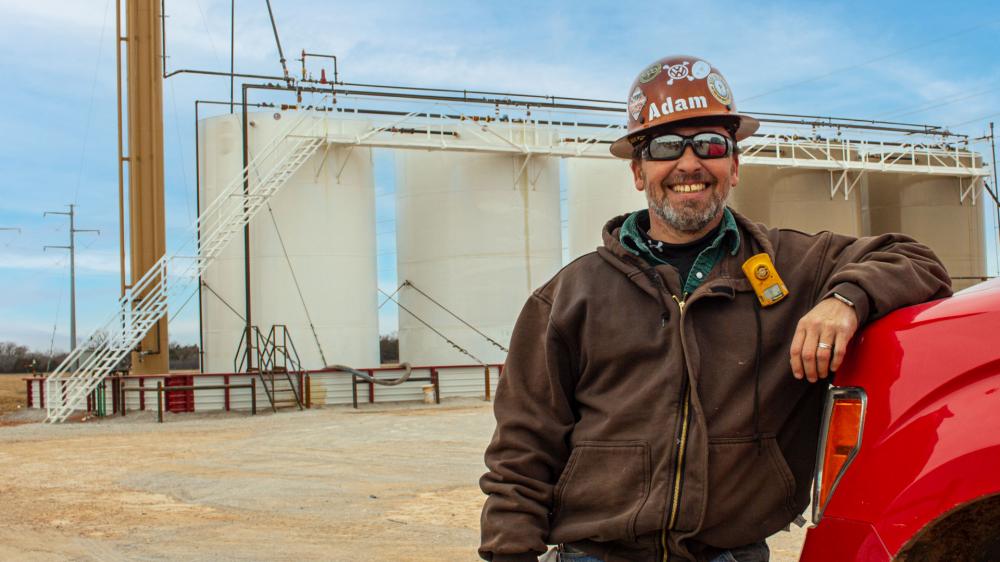
Shale Boom Creates Flowback Jobs
The practice of horizontal drilling and fracturing shale formations for oil and gas began growing in the U.S. in the early 2000s.
In September of 2014, this practice surpassed traditional methods and became the primary way companies produced energy.
Courtesy: eia.gov
After drilling a well the next step in the process requires a frac crew pumping high volumes of a mixture, proppant, into the well.
Proppant is a blend of sand, water, and additives designed to expand fractures in the shale. Installing a temorary plug is the next step after fracking the formation.
The plug will be opened when the construction crew has installed the flowback equipment and the flowback operators are on site and the well will be opened to flowback production.
The Job of a Flowback Operator
When a shale well first comes on, “flowback” is the first thing that returns. Flowback generally consists of a mixture of sand, crude oil, natural gas, and water.
A flowback operator’s job is to manage a well’s production during the first period of production, until the sand is relatively stable and the well is producing mostly oil and gas. One such operator is Adam Verrett.
Originally from a small town in South Louisiana—with a distinct Cajun-tinged accent to prove it—Adam Verrett has been chasing oil and gas jobs for the last 19 years. He’s currently a flowback operator working in the STACK in Oklahoma’s Woodford Shale.
“I knew to make the kind of money I wanted to, I had to leave home. In this industry I can make three times or more what I could back in my hometown.”
Adam has worked in the Eagleford in South Texas, the Utica and Marcellus in Ohio, and the Haynesville in Louisiana.
Living in a trailer on site, Adam works twelve-hour shifts seven days a week, rain or shine. And the well doesn’t stop for weekends, sick days, or holidays. “I haven’t seen a Christmas tree in four years,” he says.
The well site is approximately the size of a football field. At the center of it is the wellbore, out of which rises a wellhead, also called a “Christmas tree.” This is the piping, valves, and fittings connected to the top of a well that direct and control the flow.
Around the wellhead orbit the various vessels and equipment that separate the formation fluid into disposal, recycle, and sales routes.
“When the flow comes up from the well head, it runs through the Christmas tree and then to our sand separators,” says Adam. “Sand is heavier, so it gets processed out and sent to frac tanks.”
“From there, the flow goes through a choke manifold and then we send it down piping over to our separators.”
Flowback can be a very volatile period in production. Flowback operators specialize in managing this period, troubleshooting, and keeping everything flowing.
“There’s a lot going on in flowback—you have more pressure and more sand to deal with. That means there’s more opportunity for something to go wrong.”
It can take anywhere between 30 and 120 days for a well to clean up and the flowback operator to move on.
A Day in the Life
Adam’s alarm wakes him up at 3:00 a.m. After a quick coffee, he steps out of his on-site trailer to catch up with the overnight operator before his shift officially starts at 4:00 a.m.
Every hour he walks around the site, his boots crunching gravel, and checks his flow computers. He records the numbers in his tally book, to be typed into a spreadsheet later. This will give him a picture of what the well is flowing and how it’s changing.
“Sand is really a big key to this job. On this site here, sand hasn’t been as heavy as usual. I’m producing about 5-10 pounds per hour right now. A neighboring well not far from here is producing 90 pounds per hour. You just never know well to well what sand content you’ll see. You may have an idea based on what they pumped down, but even that doesn’t always tell you how much is going to be coming up.”
Sand can settle quickly on bottom of the separators and in the piping. To prevent clogging, Adam opens and checks dump valves regularly, and if needed he clears them out.
When his shift ends at 4:00 p.m., he heads to his trailer to check his numbers and make sure everything balances out. His final report is due every day at 5:30 p.m.
The Evolution of Well Site Operations
Adam says a lot has changed in oil and gas production since he got his start in 1999. For example, it hasn’t always involved spreadsheets and flow computers.
“When I was first starting out, my mentor told me if I wanted to really go places in the oil and gas industry, I needed to learn how to use a Sonney Flow Computer. It wasn’t really a ‘computer,’ but a slide chart that gave you tables of flow calculations. I still keep one with me in the truck. Every now and then I get it out and check it against the meters.”
Adam also learned to read Barton Recorders early on. “Each well had one. It was a chart with pins, like a polygraph, that would give you a readout of the well’s gas production.”
With modern monitoring equipment, production companies can see what a well is flowing without the Bartons.
“Nowadays, the guys in the office are always seeing what’s going on. They have about a 3-second lag between what’s going on here and what their computers tell them. There’s no way to get ahead of that. So I tell field guys, there’s no use making numbers up because they know what’s going on out here.”
Adam says things are certainly much safer now.
“In the ‘old oilfield’ that I grew up in, I once sat next to a separator for 34 straight hours. We were bringing on a new well, and I had to make sure it stayed online. I would lean against it and nap when I could. Then when I heard something change, I would wake up and figure out what needed fixing.”
Troubleshooting text messages between Flowback Operator Adam and Kimray Account Manager Kyle
Troubleshooting
On one of the separators in Adam’s field, a message reads: “Been fighting this thing all night!” It’s scrawled in white chalk just above a trunnion assembly of a liquid level control system.
“That’s from my night shift guy,” says Adam. “That’s why I called you guys.”
A few days prior, Adam had been working to weight his float, but any change he made didn’t seem to get the float to interfacing correctly. The last thing he wanted to do was shut in the separator and re-weight it.
He rigged up well head stud held on with string, to counter react a float that was too light. About 6 hours of adjusting to find the sweet spot got the valve working as designed.
“There’s a certain pride that comes with this job, so sometimes when we run into trouble we just deal with the problem and don’t communicate it until it becomes a huge issue. And when we do reach out, some guys tend to hoard their knowledge.”
“Fortunately I’ve got friends in this industry I’ve worked with 17 years ago. So I call them when I hit something I can’t figure out.”
Adam made a few calls about the dump valve, but was still having trouble. So he went online to see if there were any videos.
He ran into one of Kimray’s.
“Right after I saw that I texted Kyle Andrews and he got me one of the weights for the dump valve. Seems to be working now.”
The fix, before the parts arrived
Advice for a Potential Flowback Operator
Working in flowback since 2012, Adam has learned a lot about both the art and science of flowback operations.
“You have to look and listen in this job. You can hear a change sooner than you can see it. For instance, I can hear when the compressor loads. That means the oil is dumping and the gas is coming up. I don’t hear it dump but I know it is because of the compressor loading. When you use your ears, a lot of times you can catch an issue before it becomes a problem.”
Adam recommends aspiring flowback operators get started in operations. “There’s so much going on when a well is first opened, you have to know how to isolate problems and make decisions quickly. So I always suggest guys start in regular production operations. Build your troubleshooting skills doing production before you move to flowback.”
Adam also advises those interested in making a career out of it to count the cost of the lifestyle.
“I receive mail in a small town in South Louisiana, but it’s hard to call it home. I’m there about 30 days a year. The rest of the time this trailer and these fields are home.”
He’s very thankful for his family. “I’ve been married twenty-two years, and it hasn’t been easy. I’ve seen this line of work destroy a lot of marriages. You’re out away from home for long stretches and people get lonely.”
Life in the Oil Patch
On day 17 since turning on the well, production seemed to be steadying. Trucks were coming in multiple times a day to pump water and oil from the tank battery. Three frac tanks had left the day before and now only one remained.
“We’re down to about 5 gallons of sand a day. Yesterday we did 9 loads of oil; today we’re at 10. Probably another two weeks or so and this one will be cleaned up. I’ll make some calls and be ready to head to the next one.”
Adam knows his line of work is not for everyone. But it is for some. Those dedicated few who pull energy out of the ground for the world to run on.
While Adam won’t be home this Christmas, his wife and son are coming to join him.
“I’ll put in my shift and then hang out with them in the camper for a few hours before bed. It may not be a Hollywood Christmas, but this is the life we live. We have each other, and I’m doing what I do to put food on the table.”
Adam with a Christmas Tree donated by a reader