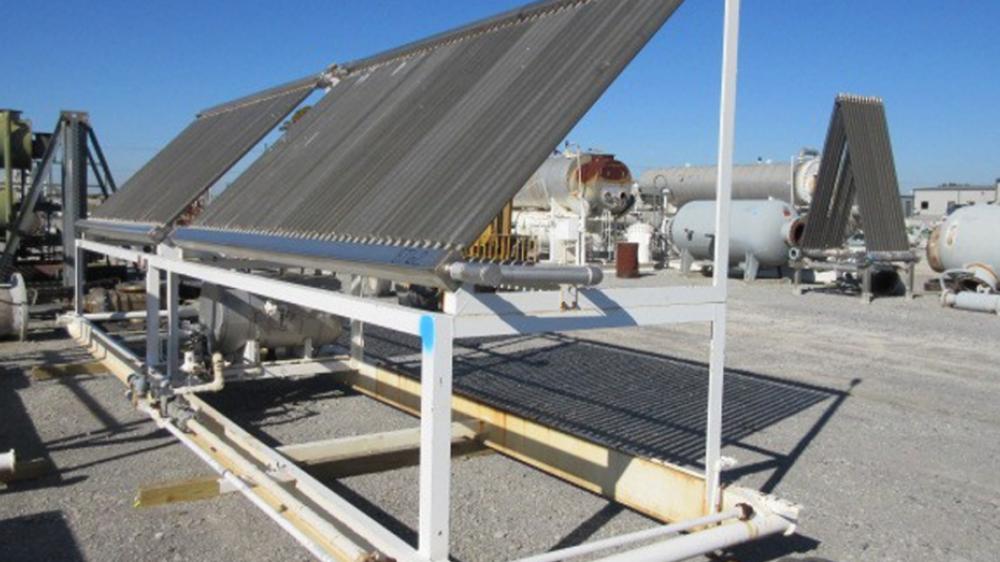
A BTEX Condenser Unit is an accessory of a natural gas dehydration unit. Producers use these units to condense four harmful vapors into liquid and dispose of them.
"BTEX" is an acronym that stands for Benzene, Toluene, Ethylbenzene and Xylene. These are naturally occurring elements found in crude oil and gas production.
What is BTEX Used For?
Producers use these units for safety, environmental, and regulatory reasons.
These units were not always used. However, as the industry learned more about what was coming out of this process and how harmful these vapors are to humans, they developed this process to capture and eliminate them so they aren't released to atmosphere.
While these systems can be challenging, the positives clearly far outweigh the negatives.
Is BTEX a Volatile Organic Compound (VOC)?
The BTEX compounds are classified as "Volatile Organic Compounds" (VOCs). VOCs are a natural result of the gas dehydration process and must be dealt with safely. VOCs can not only cause harm to the human body but also to the environment.
All oil and natural gases have some number of VOCs, but during the gas dehydration process, these VOCs are concentrated into a very potent mix of hydrocarbons called BTEX.
Prolonged exposure to BTEX compounds can lead to cancer and other series health concerns.
Where do Producers Use BTEX Condenser Units?
Producers install BTEX Condenser Units primarily in midstream operations, though some larger upstream companies use them.
A BTEX is located located off the still columns of reboilers, both at well sites and gathering sites. Producers can retrofit these units into a system that used to send these vapors to atmosphere.
How Does a BTEX Condenser Unit Work?
A BTEX Condenser Unit captures and cools steam. The steam is water vapor that is boiled out of water-saturated glycol that is used in the dehydration process. This steam used to come out from the sill column into the atmosphere.
There is airflow over the cooling fins. Many have A-frames with cooling fins that look like an A-frame house.
Airflow cools and condenses steam into a liquid, which drops down into a small two-phase separator. A pump then moves the condensed liquid into a storage tank for disposal.
We pipe the non-condensable gasses to the reboiler, and depending on manufacturer they go one of two places:
- The stack through a glow-plug in the stack and it combusts in the stack or
- A separate burner inside the burner assembly for incineration
Because the condensed liquids in this unit can be so corrosive, newer models are often stainless steel.
These units feature low pressure operation and a gravity-feed system. You may see relief valve on these systems that can be operating at 1-3 PSI.
With such little pressure, OEMs must design them properly to handle the amount of steam coming out from the still column.