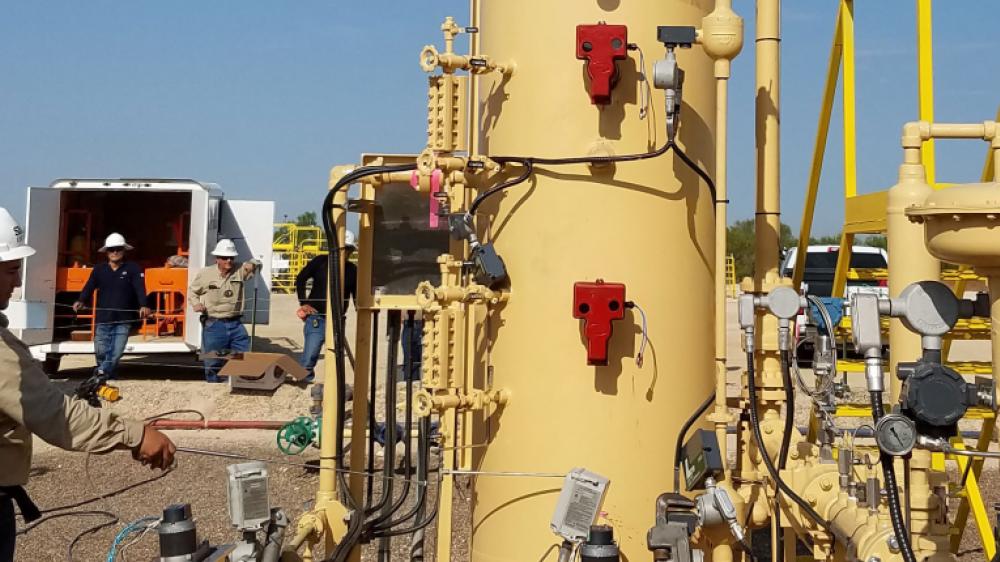
Recently, a producer ran into a problem in Catarina, Texas. As the Technical Development Engineer, he was responsible for keeping this field producing smoothly. But it seemed his liquid level controller wasn’t maintaining the proper interface of oil and water.
How a Separator Works
Oil and gas producers use separator vessels (like the one below) to separate a well stream into gas and liquid. Typically the installation of separator vessels is near the wellhead. They come in three styles: horizontal, vertical, or spherical.
Two-phase oil and gas separators separate the emulsion into gas and liquid. Three-phase separators go a step further to break the emulsion into gas, oil, and water. In this case, the producer was using a three-phase separator.
When fluid enters a three-phase separator, separation begins naturally. This is due to the different specific gravities of the elements.
- Gas rises to the top of the vessel and is released into a gas line for either further processing downstream or combustion.
- Oil settles at the middle level. When it reaches a specific height as set on the liquid level controller, it dumps to the production line. Then it is sent downstream to be further processed or sold.
- Water is controlled by another level controller. It's dumped into a separate line and sent to be recirculated or injected.
While this separation process does occur naturally, some producers choose to introduce heat into the vessel, which accelerates the process.
The problem with the liquid level
Because his liquid level controller was not holding the level he wanted, the producer closed the ball valve upstream of the separator and removed his liquid level controller from the separator.
Upon examination, it was clear that the displacer on the level controller was malfunctioning.
A displacer malfunctions when the process fluid doesn’t react well to the material of the displacer. This may be because the specific gravity of the fluid is lighter than the displacer is made for. It could also be because the fluid is so corrosive that it eats through the displacer.
This malfunction was leading to erratic, imprecise dumping of oil and water rather than steady dumping after the appropriate amount of separation occurred.
The Solution
His first step was to reach out to the original product manufacturer. He ran into delays attempting to solve the problem by phone, and grew frustrated due to the downtime.
He then contacted his corporate office in Houston to see about replacing the units. The Houston office contacted Kimray’s local team in Corpus Christi for help.
Since the site was running on electric actuation, the Kimray team recommended outfitting the separator with the Gen II Electric Level Controller. Kimray sent certified technicians to the site to install it.
Currently using a Gen II? Upgrade to the new Gen 3 - our all-new liquid level controller that's even easier for operators to install and adjust in the field.
After the 1-hour installation, the crew re-opened the ball valve and allowed the vessel to re-fill. They watched as the displacer rose along with fluid, activating the dump valves and processing the fluid correctly. The system was again fully operational.