In natural gas production, managing your gas pressure drops is critical. If mishandled, these drops can jam up your system and cause downtime.
In this blog, we're going to answer the following 6 questions:
- What is a Pressure Drop Across a Valve?
- Does Pressure Drop Reduce Flow Rate?
- Why is Choked Flow Bad?
- Does Partially Closing a Valve Increase Pressure?
- Which Valve has the Highest Pressure Drop?
- What is the Solution to Choked Flow?
1. What is a Pressure Drop Across a Valve?
A pressure drop across a valve means that the media is flowing the normal direction—from up to downstream. If you didn't have a difference in pressure between upstream and downstream—in other words, if those pressures were equal—there would be no flow across the valve.
Production fluid, be it oil or natural gas, naturally flows from high to low pressure. That’s how the flow is determined in any kind of separation equipment or system.
The pressure drop across a valve may also be called the "differential pressure."
How is Pressure Drop Set?
Pressure drop across a valve is determined by the control points both upstream and downstream of the valve. If the valve is in a dump application, the pressure drop will be determined by two things:
- The pressure held on the separator by the back pressure regulator
- The pressure controlled by the operating pressure of the downstream equipment
2. Does pressure drop reduce flow rate?
Pressure drop does affect flow rate, but does not always reduce it.
Again, every valve flowing media will have a pressure drop, which is what creates the flow. Whether the pressure drop reduces or increases flow rate depends on if the drop moves higher or lower.
Here's the general rule:
- Higher pressure drop = more flow.
- Lower pressure drop = less flow.
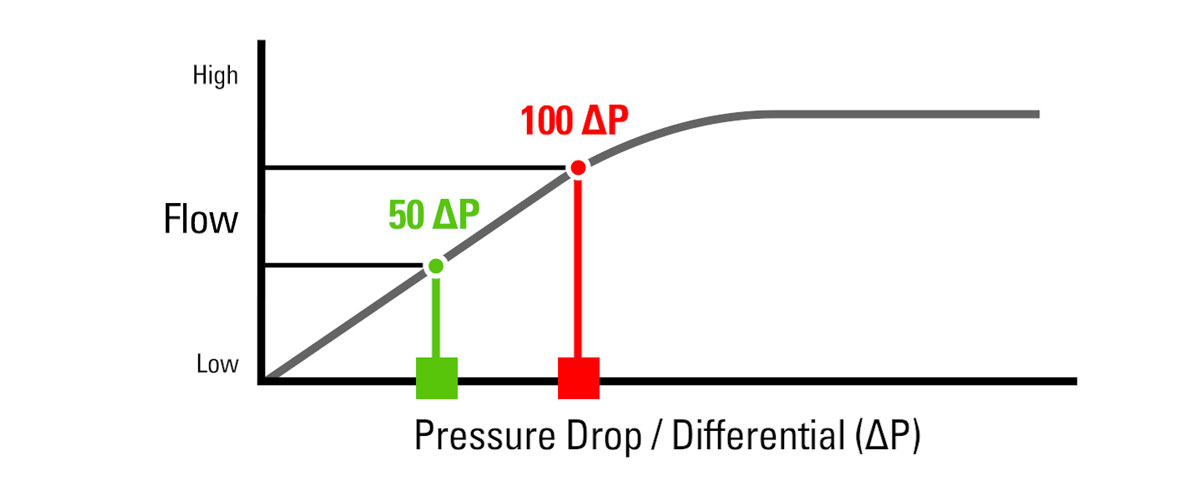
If the pressure drop gets higher (meaning there is an increase in differential pressure), there will be more flow across a valve (to a point).
If the pressure drop gets lower (meaning there is a decrease in differential pressure), there will be less flow across a valve.
For example: A 1” trim in a 2” stem guided valve would be able to flow more with a 100 PSI drop than if it had a 50 PSI pressure drop. This is because there’s more pressure in the flow media pushing on it to force it through the 1” trim.
Note, however, that this increased flow from increased pressure cannot go on indefinitely. At a certain point, you will reach what’s called choked flow, which we'll cover next.
3. Why is choked flow bad?
There comes a point where if you’re increasing the pressure drop by lowering the downstream pressure, you’re not going to increase the flow rate. The fluid will reach its maximum velocity at the vena contracta, and after that point, it will enter a state called "choked flow."
The higher the pressure drop is, the more flow you can get across a given orifice size. If you want to increase volume using the same valve and equipment you have, but you are in choked flow, you won’t be able to.
This creates problems in your system because you can't pass the amount of volume that you need. And depending on the application you might be starving another piece of equipment that needs volume to operate correctly.
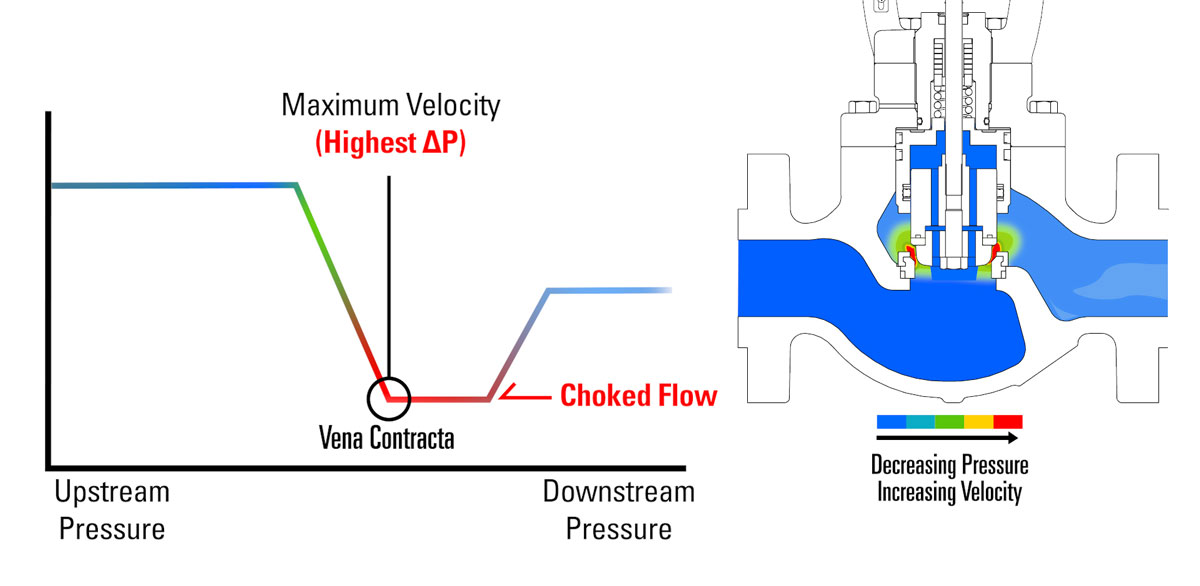
4. Does partially closing a valve increase pressure?
If you partially close a valve, would it increase the pressure? That depends on your volume.
- If you partially close a valve and you are flowing a relatively high amount of volume, upstream pressure may increase if it’s not opening far enough to release pressure.
- If the valve is partially closed and you are flowing a relatively low amount of volume, it could release enough volume so that pressure decreases.
5. Which valve has the highest pressure drop?
There are many variables that determine what your pressure drop is, including the application and the flow conditions the valve is exposed to.
That said, our Cage-Guided High Pressure Control Valve can handle higher pressure drops than many valves because of its balanced trim.
This is because with the working pressure of the valve, there is the potential of a high pressure drop, and the valve's operation allows it to work in those high pressure drop applications.
How it works:
- The flow through the cage-guided high pressure control valve comes from underneath the seat.
- The upstream pressure moves through the two communication holes inside the piston. This equalizes the pressure on the top and bottom of the piston.
- This means that the valve is balanced, so regardless of how large your pressure drop is, the valve can be opened or closed by a standard pressure of supply gas from the pilot.
To learn more see our video How to Operate the High Pressure Control Valve.
6. What is the solution to choked flow?
To get your valve out of choked flow, you must decrease the pressure differential. If you are worried about not passing enough volume through the valve in choked flow, you need to increase your valve trim size or you can increase your upstream pressure.
One important distinction to make: Once you’re in choked flow, decreasing downstream pressure to increase the pressure differential doesn’t do anything to increase flow rate.
If you increase upstream pressure, you’re adding more energy to push it across the valve so that can increase the flow rate because it increases the pressure drop.
In other words, when you’re in choked flow, you can push more production fluid or gas through but you can’t pull more through.
If you add pressure from behind (upstream), you can push more through, but if you take away pressure downstream to create a higher differential, it’s not going to allow more flow through the valve.
Bonus: cavitation, FLashing, and Staging Pressure drops
Cavitation is the formation and collapse of air or gas bubbles in a liquid.
The bubbles are formed when liquid undergoes a rapid change of pressure and falls below the vapor pressure. These bubbles collapse when the pressure recovers.
This can all happen in a very short span just after the vena contracta—the point in the valve where the diameter of the flow is at its smallest, and fluid velocity is at its maximum.
What are the symptoms of cavitation?
Because it happens inside a valve or pipeline, cavitation is not easy to spot. Here are two symptoms that may be caused by cavitation:
- Valve Trim Pitting. When the vapor bubbles collapse, it creates a strong force. When this happens over and over on the metal surface of the valve trim, the metal will begin to erode and pit.
- Water Hammering. If cavitation is occurring, your valve may repeatedly open and close sharply. This is called water hammering, and it can lead to an eventual compromise of the valve stem, coupling block and/or valve seat.
How Can I Prevent Cavitation?
There are three things you can do to prevent cavitation in your valves:
- Decrease the pressure drop across your valve.
- Install the valve in a cooler place in the process, thereby decreasing the vapor pressure.
- Make sure your valve is properly sized. Cavitation often happens in applications when a valve is oversized. For tips on how to size your valve, see our video, “How to Select a Valve.”
Cavitation happens a lot with high pressure drops and high velocities. If you’re experiencing a high pressure drop, another problem to watch for is flashing.
What is "flashing" in a control valve?
While cavitation is more common in liquid, flashing is more common in gas production.
Flashing happens when you reduce the pressure on a liquid hydrocarbons to the point that they "flash" into vapor.
For example: If you dump your oil emulsion quickly from a high pressure to low—say, 500 PSI down to 60 PSI—it can flash, meaning the rich, light, high-gravity oil condensate in your production vaporizes, and you lose that resource forever.
The pressure on your operation’s production vessels is what keeps this oil condensate in liquid form.
This is why producers drop gas pressure in “stages.”
What does it mean to stage gas pressure drops?
Staging is the process of reducing pressure in stages rather than all at once. Reducing pressure all at once can not only cause freezing, but cavitation and flashing. More oil and condensate can be recovered in liquid form and not be lost to vaporization when staging pressure drops.
This is usually a concern in gas-producing wells. These operations are usually labeled as “natural gas production”—meaning gas is the largest resource the producer is recovering by volume.
However, these wells still produce oil, sometimes called “white oil” because of its light color, and it can create significant revenue for these producers.
Many producers use a gas production unit (GPU) on their natural gas wells to heat the well stream before reducing the pressure, helping to mitigate freezing. In this set up, the oil and condensates can be recovered in the separator portion of the GPU.
The dry gas, meanwhile, flows out of the top of the vessel. The gas is sent downstream into a sales line. Some of the dry gas is used to power the instrumentation on the GPU.
Staging vs. Compression
Note staging is the reverse of the process of compression. The purpose of a natural gas compressor is to re-pressurize natural gas to push it downstream.
When the gas reaches a compressor, producers want the condensate to be “knocked out” so it doesn't damage the compressor.
To speak with an expert about how to maximize your oil and condensate recovery, contact your local Kimray store or authorized distributor.