Frozen control equipment can lead to significant production downtime and frustration.
In this video we explain what causes control valves to freeze and identify two solutions to help you prevent freezing at your operation.
Why Oil & Gas Equipment Freezes
There are two main causes of freezing in control valves, instrumentation, and sensing lines: ambient freezing temperatures and the Joule-Thomson Effect.
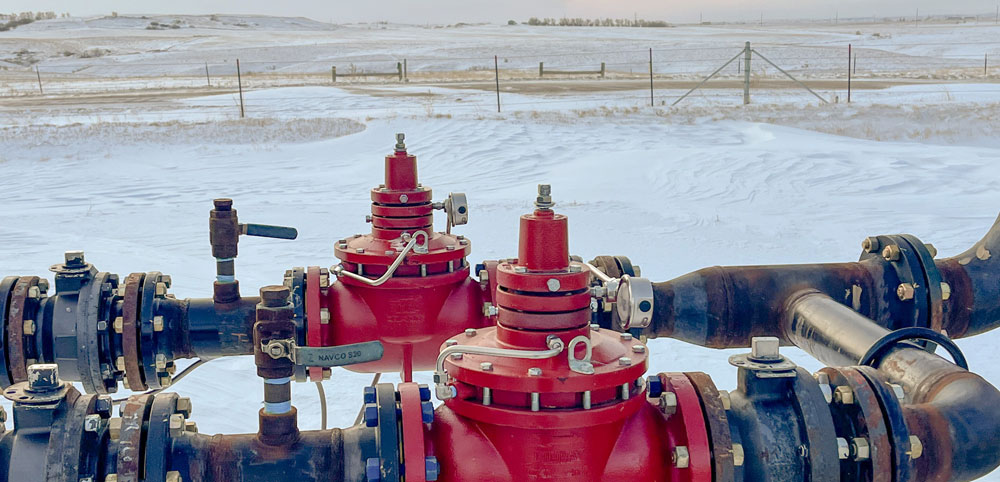
Ambient temperatures below 32°F (0°C) can quickly cause natural gas supply and sense lines to freeze because of the small volume of gas flowing through them as opposed to pipelines and control valves.
The Joule-Thomson Effect states that for every 100 PSI pressure drop, natural gas temperature drops 6-8°F.
Since natural gas carries some moisture in it, when there is a significant pressure drop, there is the potential for that moisture to freeze.
This means high enough pressure drops—even without freezing ambient temperatures—can cause equipment and pipelines to freeze anytime of the year and in any part of the world.
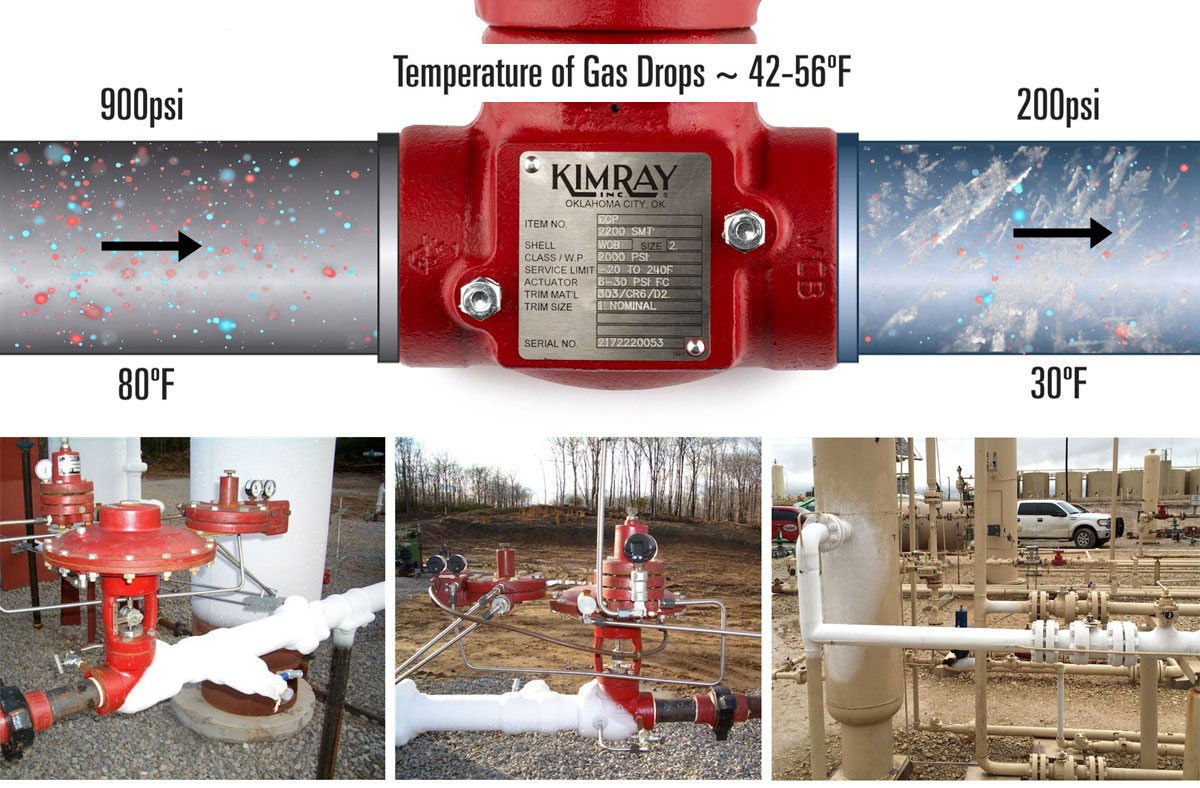
Solutions
Two solutions to prevent freezing are Insulated Covers and Catalytic Heaters.
Insulation Covers
Insulated covers conserve and prevent heat from escaping your process equipment and have been field-tested on pipes, valves, and vessels to ambient temperatures of -50°F without experiencing freeze failure.
We offer several covers uniquely designed to protect various Kimray valve types, sizes and end connections.
If you only need heat retention rather than heat generation, insulated covers are an effective, affordable and easy-to-use solution.
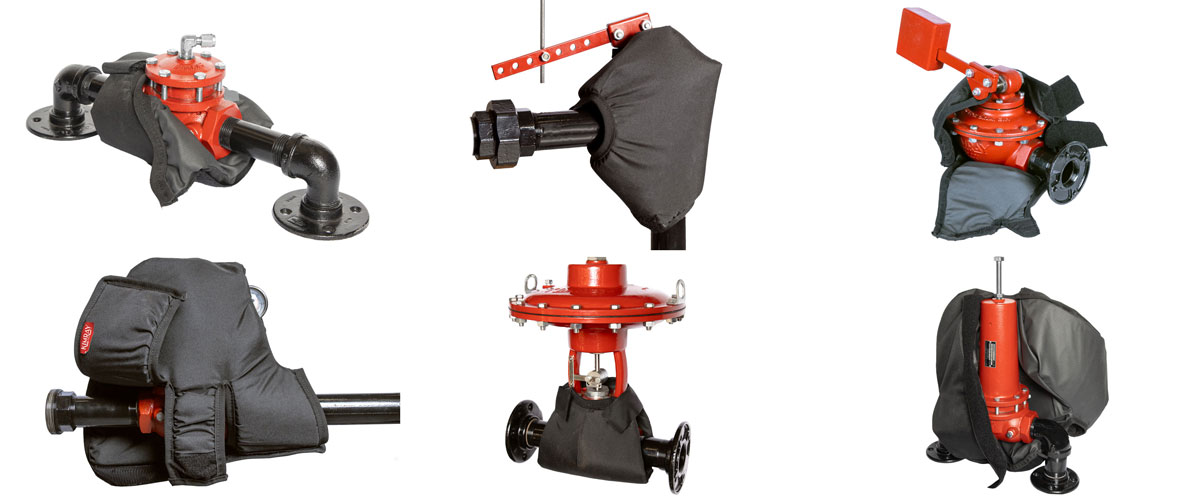
Catalytic Heaters
Another solution to prevent freezing equipment is catalytic heaters. Options in this category include space heaters, instrument gas heaters, and heated enclosure packages.
Sometimes freeze prevention is as simple as maintaining a warm environment. Catalytic space heating solutions can be used for metering, measurement, and analysis applications in equipment cabinets, housed units, and large buildings such as compressor stations.
Another option is instrument gas heaters, which can be used any time instrument gas or air supply is susceptible to freezing. Stainless steel heat exchange tubing passes through an insulated enclosure, and a catalytic heater raises the temperature of the gas or air flowing through it.
The most popular and usually most effective way to prevent freezing in regulators, valves, chokes, and other process control equipment is with Heated Enclosure Packages. These packages feature stainless-steel enclosures containing a catalytic heater, which directs safe, flameless, infrared heat at the valve body it is surrounding.
Different units are available depending on the type and size of the valve being heated, the required BTU per hour, and other factors.
Which Freeze protection is Best for Your Operation?
To help you decide which freeze-prevention solution is best for your operation, let's consider three factors:
- Startup Process & Operation
- Cause of Freezing
- Accessibility
1. Startup Process & Operation
Catalytic heaters must have CLEAN fuel gas to operate.
If the gas in your area is wet or sour, catalytic heaters may not be the best option. However, if you are in this scenario, you can use a propane tank to run these heaters. The only change you need to make is replacing the heater orifice with an orifice specifically designed to accept propane.
These heaters also must be manually started with a voltage jump, which can be provided by jumper cables connected to a vehicle or other battery source. However, they do not require a permanent electric supply.
Watch Video: How to Start Up a Catalytic Heater
Insulated covers, meanwhile, can be installed manually and require no start up or ongoing gas supply. Kimray offers covers that match our most commonly used valves to ensure the best coverage for your operation.
2. Cause of Freezing
Joule-Thomson Effect
If the JT effect from large pressure drops is the primary factor causing freezing of your valves, a catalytic heater on the valve itself is likely your best option. This is because the unit generates heat rather than only insulating existing heat.
Insulation alone will typically not solve this problem but only make it worse by keeping it cold inside the equipment.
Cold Weather
If freezing ambient temperatures are the primary factor causing freezing of your valves, insulated jackets can often provide enough heat retention to prevent freezing. A catalytic heater can be used to directly heat the areas of concern, but again requires clean gas and more effort in the start-up process.
3. Accessibility & Longevity
Heated enclosure units include a hinged door, which provides operators with easy access for valve maintenance or repair. With no moving parts, the heater will operate indefinitely as long as it has a clean fuel supply.
Insulation covers can be quickly installed with the industrial Velcro® joints. When you need to perform maintenance, inspections, or LDAR scans, they can be removed just as quickly.
Reach out to your local Kimray store or authorized distributor today to discuss freeze prevention for your operation.