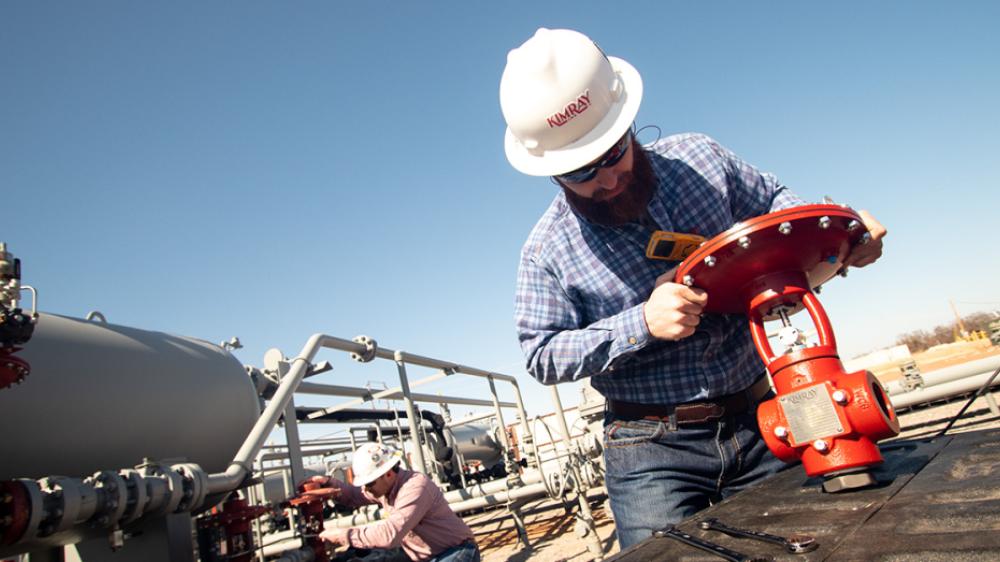
A control valve is a device that controls the flow of liquid or gas.
What are the different control Valve Types?
Types of control valves include:
- High Pressure Control Valves
- V-port Ball Valves
- Segmented Ball Valves
- Butterfly valves and gate valves
Note that regulators are also sometimes referred to as control valves. The main difference between a control valve and a regulators is control valve control flow, while regulators control pressure. Learn more about regulators here.
What are some Control Valve applications?
Control valves are used in oil and gas production to controls the flow of liquid or gas. Oil and gas producers use High Pressure control valves in the following applications:
- Liquid Dump Valve on a separator or treater
- Gas Back Pressure on any production vessel
- Pressure Reduction on a compressor
How does a Control Valve Work?
To “control” the liquid or gas, a control valve can open or close fully (on/off), or slightly (modulating).
Modulating valves can open or close slightly. They do this in order to change the size of the opening through which the media is flowing. They may also be moved to fully closed or fully open.
However, a valve by itself will not do anything. In order to open or close, the valve actuator must receive a signal from an outside source. This is provided by one of the following:
- Pneumatically actuated control valve: a pneumatic pilot or liquid level controller
- Electrically actuated control valve: an electric pilot, Programmable Logic Controller (PLC), or Remote Terminal Unit (RTU)
How Does a Control Valve Hold Back Pressure?
Here's how a pneumatically actuated High Pressure Control Valve installed on a separator holds back pressure:
- Pneumatic Pilot—The signal is provided by a pneumatic pressure pilot. The pilot on this package senses upstream pressure and sends a corresponding signal (typically processed supply gas) through tubing into the actuator of the valve.
- Pneumatic Actuator—The actuator reacts to this pilot signal by either closing or opening the valve.
- Electric Pilot—In the case of an electrically actuated High Pressure Control Valve installed on a separator to hold back pressure, the signal is provided by an electric pilot (or PLC). The electric pilot receives an analog 4-20mA signal from a sensor, which represents a process condition. The pilot then conditions this signal and sends a corresponding signal (4-20mA loop) to the electric actuator of the valve.
- Electric Actuator—The actuator reacts by either opening or closing the valve.
What are the Important Control Valve Parts?
Here is a look at some of the key internal parts of our pneumatic Stem Guided High Pressure Control Valve.
These are linear valves that have a stem that guides the ball into the seat. They can operate in modulating control or on/off applications.
They key parts of a control valve are as follows:
- Bonnet: The bonnet is the top of the valve, which houses the diaphragm and actuator spring.
- Spring: The spring holds tension on the stem, keeping the valve in its fail position.
- Control Valve Actuator: The control valve actuator receives a pneumatic signal from a pressure pilot or another pneumatic controller and adjusts the valve position accordingly. This actuator can be disassembled and inverted to convert the valve from fail-closed to fail open or visa versa.
- Stuffing Box Assembly: The stuffing box assembly houses the valve packing. The valve packing provides a seal that prevents leakage from the stuffing box while allowing the stem to move up and down as needed to open and close the valve.
- Yoke and Travel Indicator: The yoke and travel indicator give a visual identification of the valve's position at any given moment.
- Stem and Seat: The ball and seat are what block off the flow through the valve. These are vital pieces and also the items most susceptible to wear and tear from contact with abrasive or corrosive production.
To learn more about control valves and how they can help your operation schedule a training session with your local Kimray store or authorized distributor.