The Kimray Electric Glycol Pump is an efficient, emissions-free solution for gas dehydration systems.
Like with all equipment, regular maintenance is key to extending the pump’s life and optimizing the efficiency of your system.
In this video, we’re going to show how to perform routine maintenance on the Electric Glycol Pump, including changing the oil, replacing diaphragms, and installing a complete valve kit.
Repairing the Electric Glycol Pump
As long as it is isolated from production, the Electric Glycol Pump can be repaired on site and does not need to be separated from the motor. As long as you have enough space below the pump to collect the used oil, you may choose to leave it in place. Note that we will not be repairing the motor in this video.
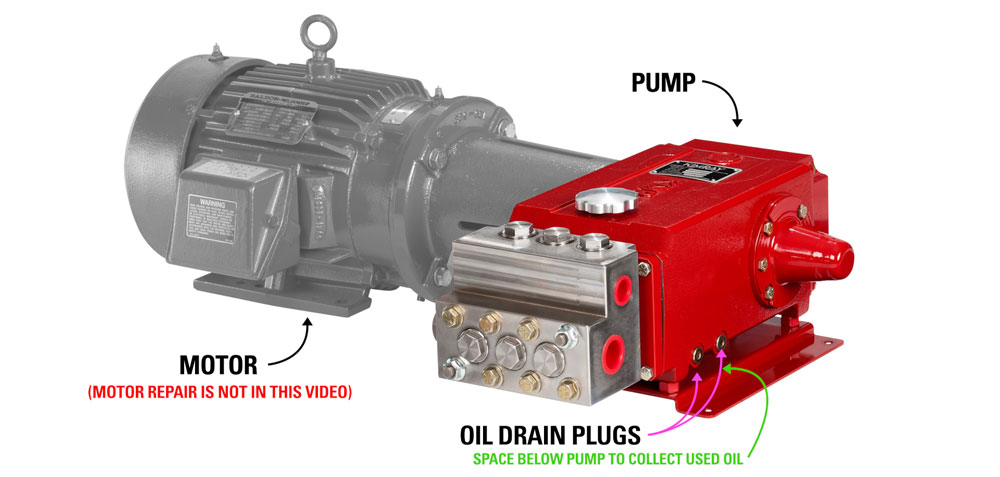
The front of the pump is the fluid end. The large center portion is the hydraulic section and the back of the pump is the crankshaft end. We will only be working on the fluid end. If you need help with the hydraulic section or the motor, contact Kimray Field Services.
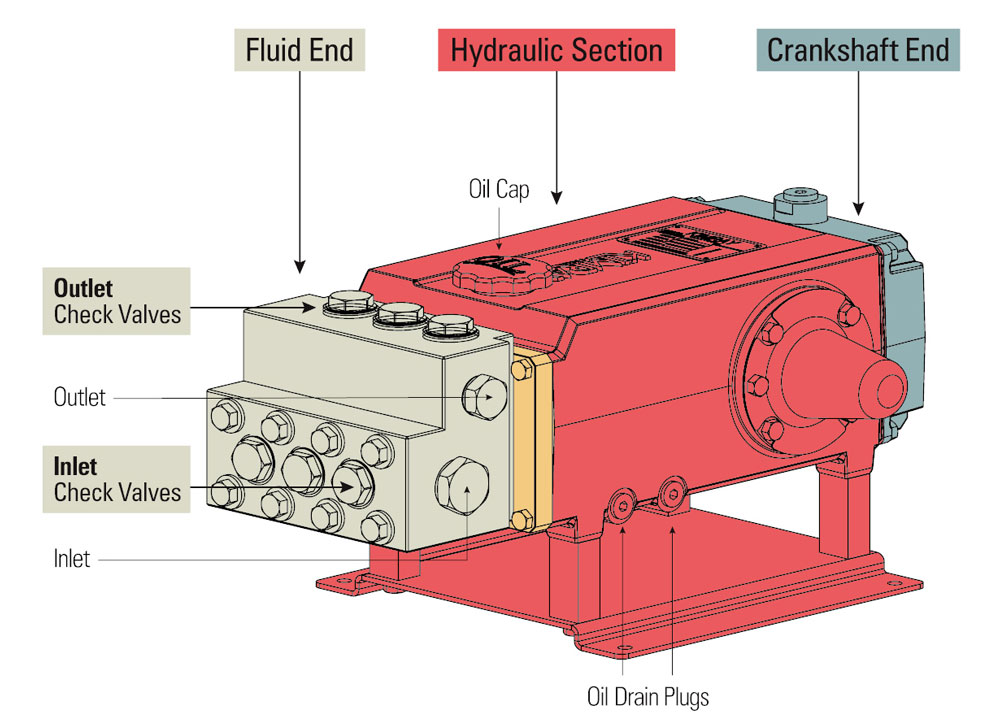
Important: This Fluid End Service is non Kel-Cell versions. Kel-Cell versions are indicated by a “K” in digit 5 of the pump model number. Non Kel-Cell versions are indicated by an “A” or “D” in digit 5 of the pump model number.
Tools
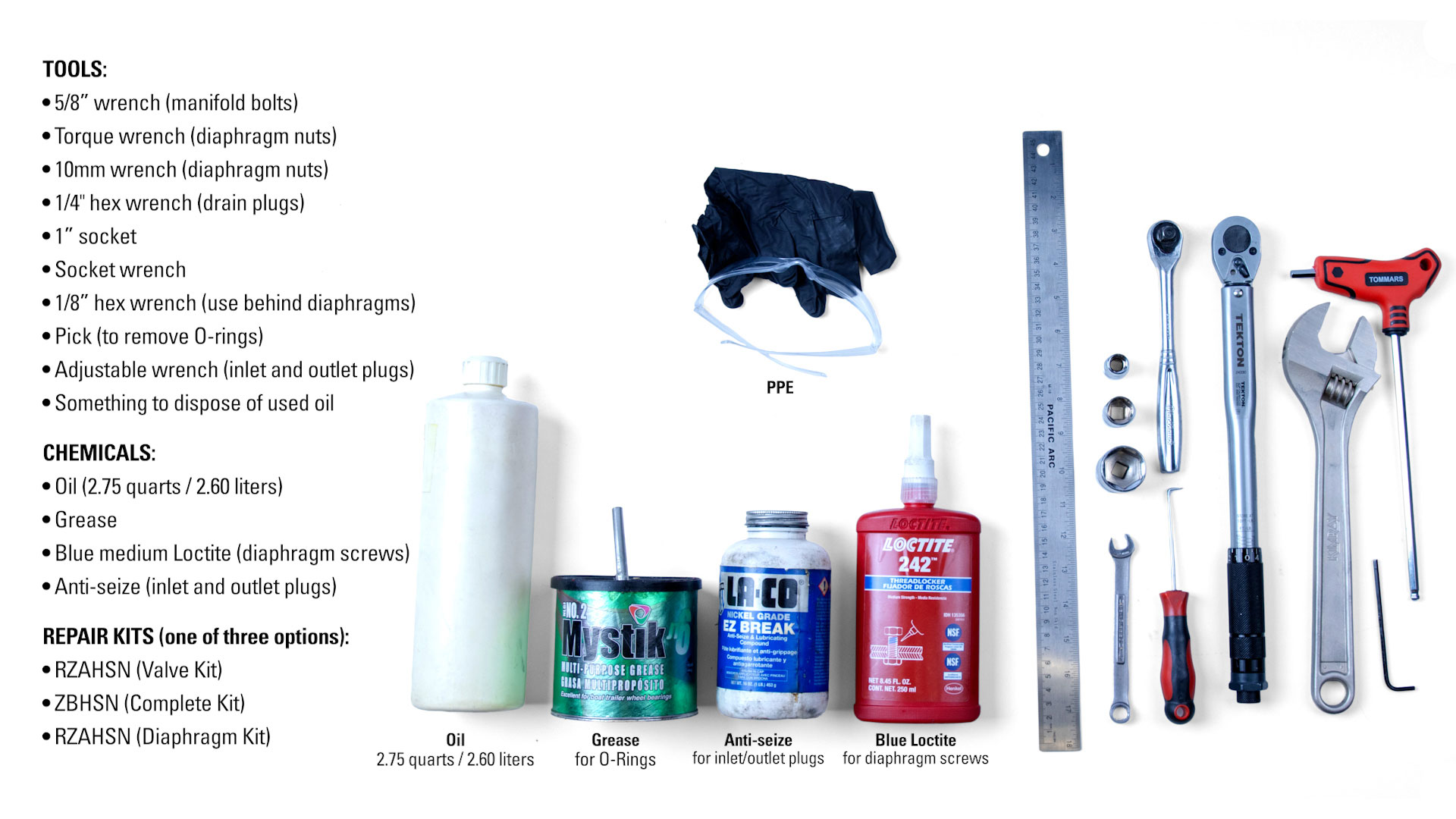
- 1/4" hex wrench (oil drain plugs)
- 5/8” wrench (manifold bolts)
- 10mm torque wrench (diaphragm nuts)
- 1/8” hex wrench (to hold shaft behind diaphragms)
- 1” socket wrench (or adjustable) (inlet and outlet plugs)
- Pick (to remove O-rings)
- Something to collect used oil
Chemicals
- Oil (2.75 quarts / 2.60 liters)
- Grease
- Blue medium Loctite (threads of diaphragm screws)
- Anti-seize (threads of the inlet and outlet plugs)
Repair Kits (3 Options)
There are 3 repair kits. In the video, we use the complete repair kit (RZBHSN). It includes the contents of both the Valve Kit and Diaphragm Kit.
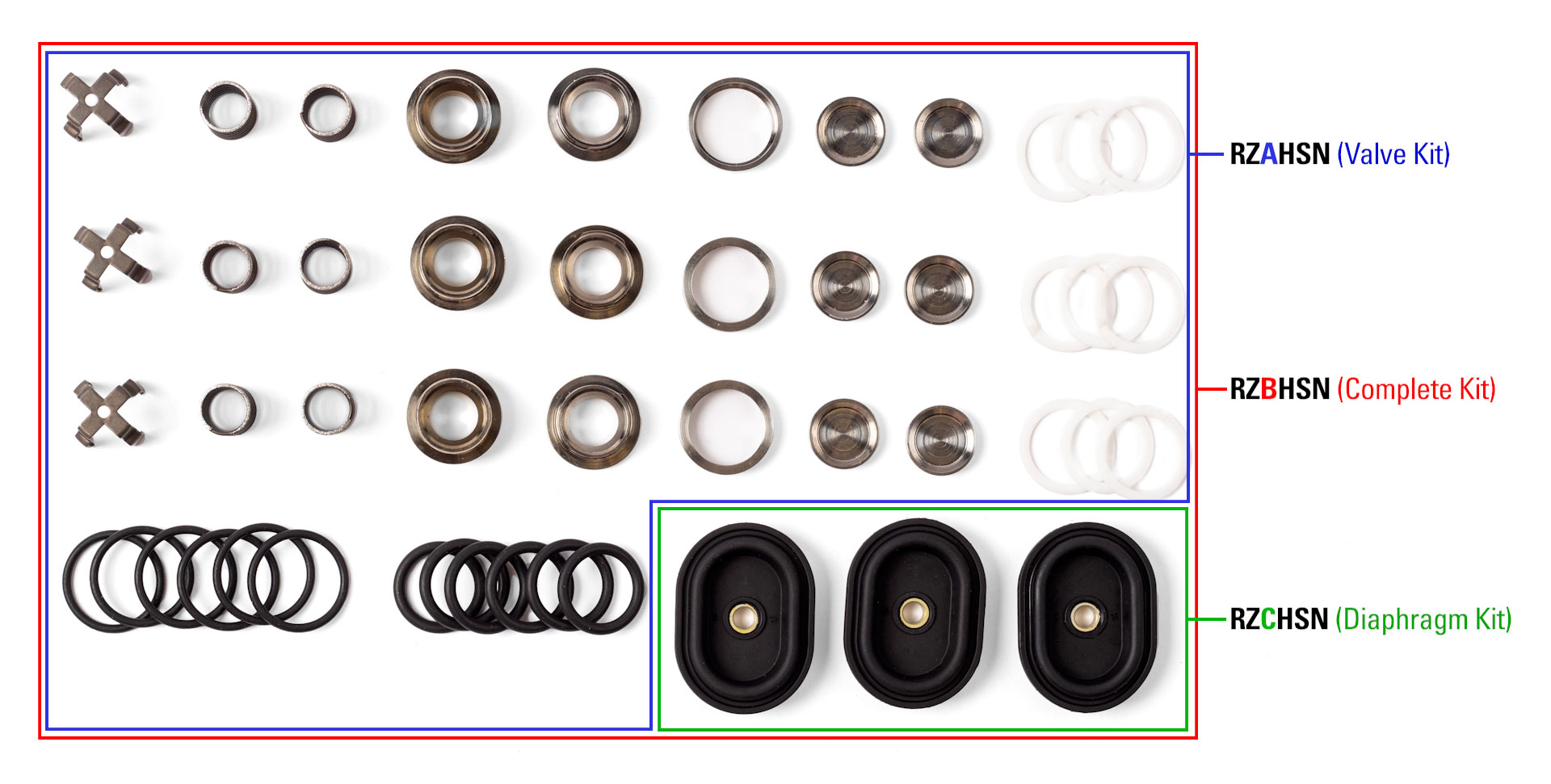
Changing the Oil
We recommend changing the oil after the first 500 hours of operation, and then according to the guidelines below.
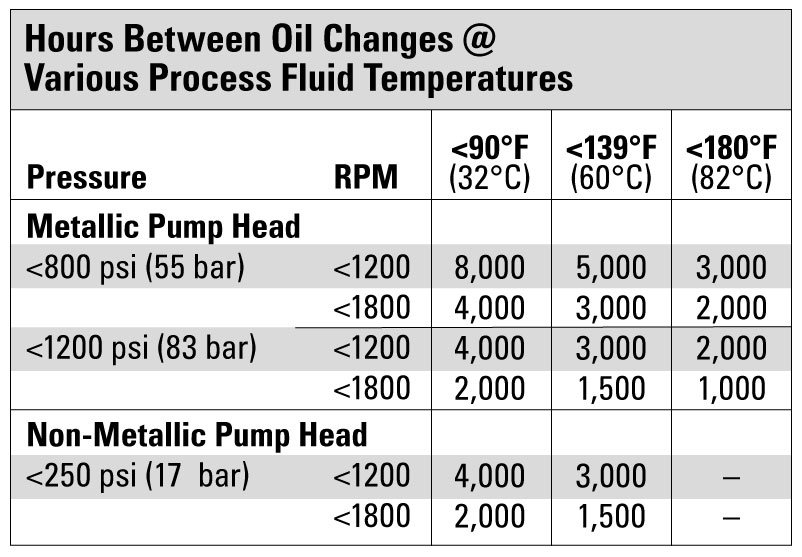
Changing the oil is simple.
- Secure the pump. We are using a clamp on the table.
- Place an appropriate vessel under the drain plugs to catch the used oil.
- Use a ¼" hex wrench to remove the two drain plugs.
- Then open the top cap to accelerate the flow.
- Once the oil has drained, replace the drain plugs and fully tighten.
- Replace the cap for now to keep contaminants out of the body while we finish the repair. We’ll add the new oil last. If you are only performing an oil change, you can add 2.75 quarts (2.60 liters) of oil now.
Disassembly: Removing Check Valves
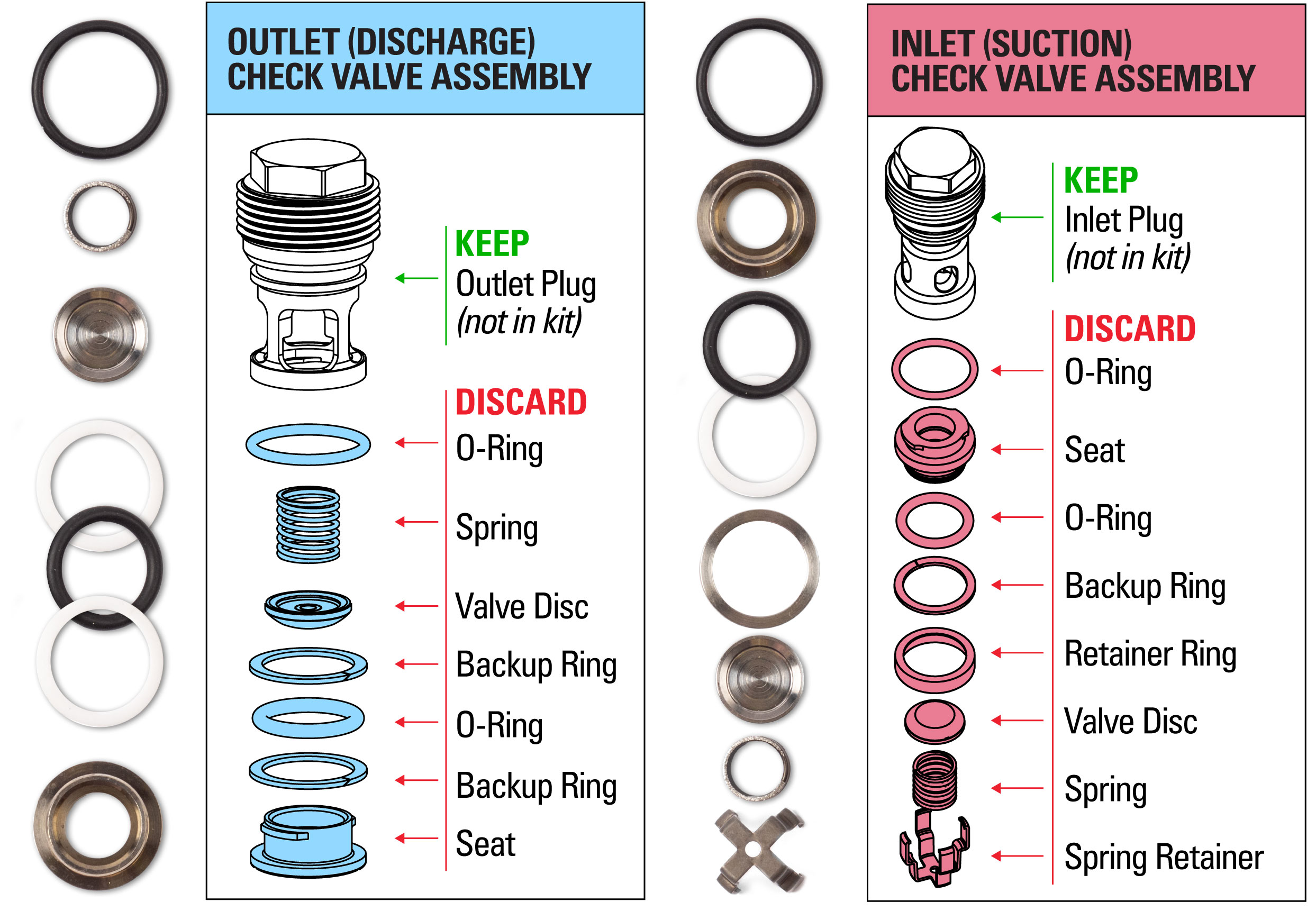
We'll start by removing the discharge (outlet) and suction (inlet) check valves.
If you are only replacing the diaphragms from the diaphragm kit (RZCHSN), you can skip this step and begin with removing the manifold.
- Use a large adjustable wrench or 1" socket wrench to remove the three discharge (outlet) check valves.
- The valve outlet assembly twists off and separates from the plug. Discard the assembly but keep the plug.
- Remove and discard the O-ring from the outlet plugs.
- Use a large adjustable wrench or 1" socket wrench to remove the three suction (inlet) check valves.
- The valve inlet assembly twists off and separates from the plug. Discard the assembly but keep the plug.
- Remove and discard the O-ring from the inlet plugs.
Disassembly: Manifold
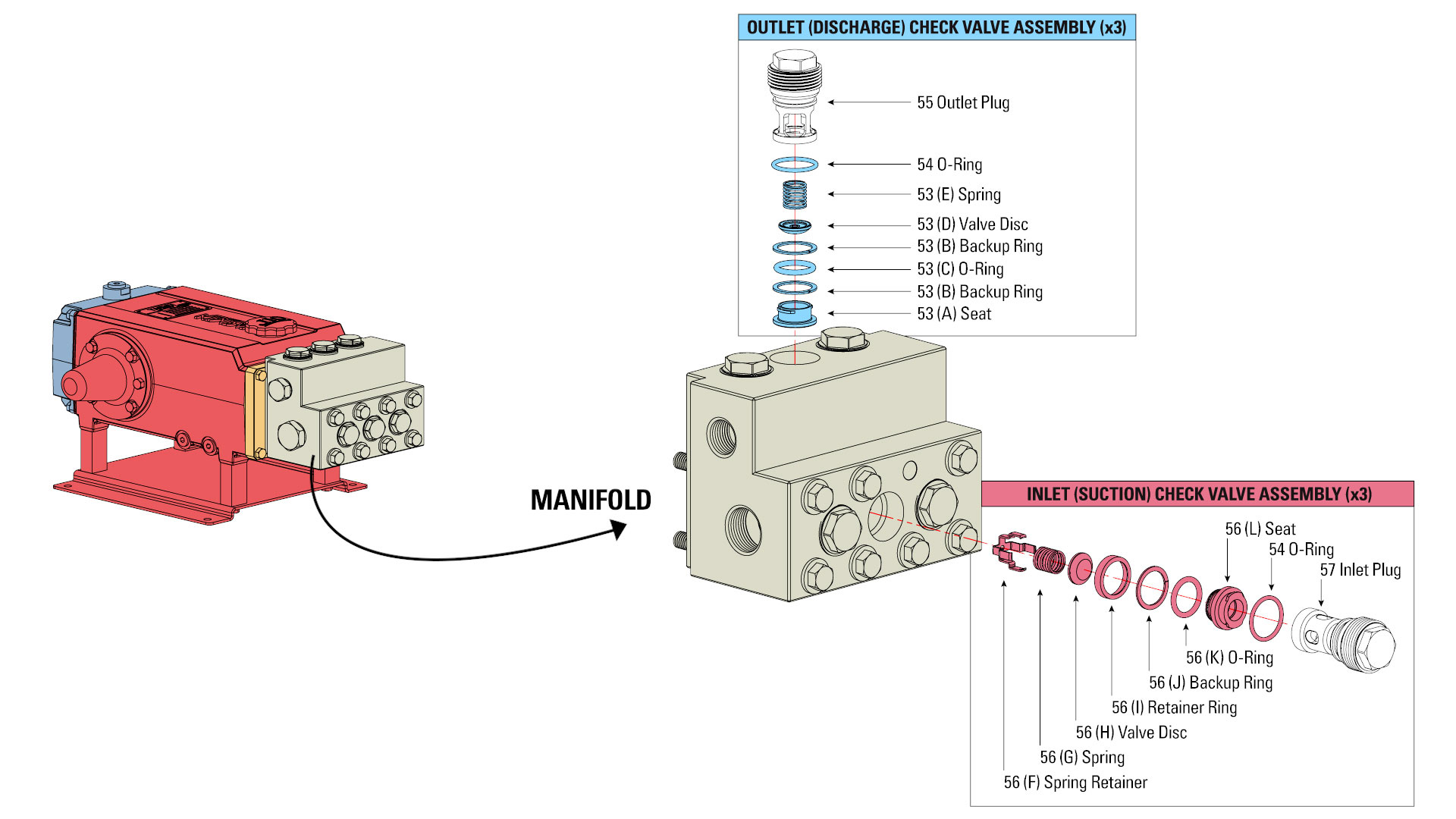
- Next, use a 5/8” wrench to remove the 8 bolts around the manifold, then remove the manifold.
- Inspect the manifold for signs of excessive wear. Place a straightedge across the surface to check for warping. A worn or warped manifold should be replaced.
- Blow air or brake cleaner through the inlet and outlet holes to clear any debris or buildup.
Disassembly: Diaphragms x3
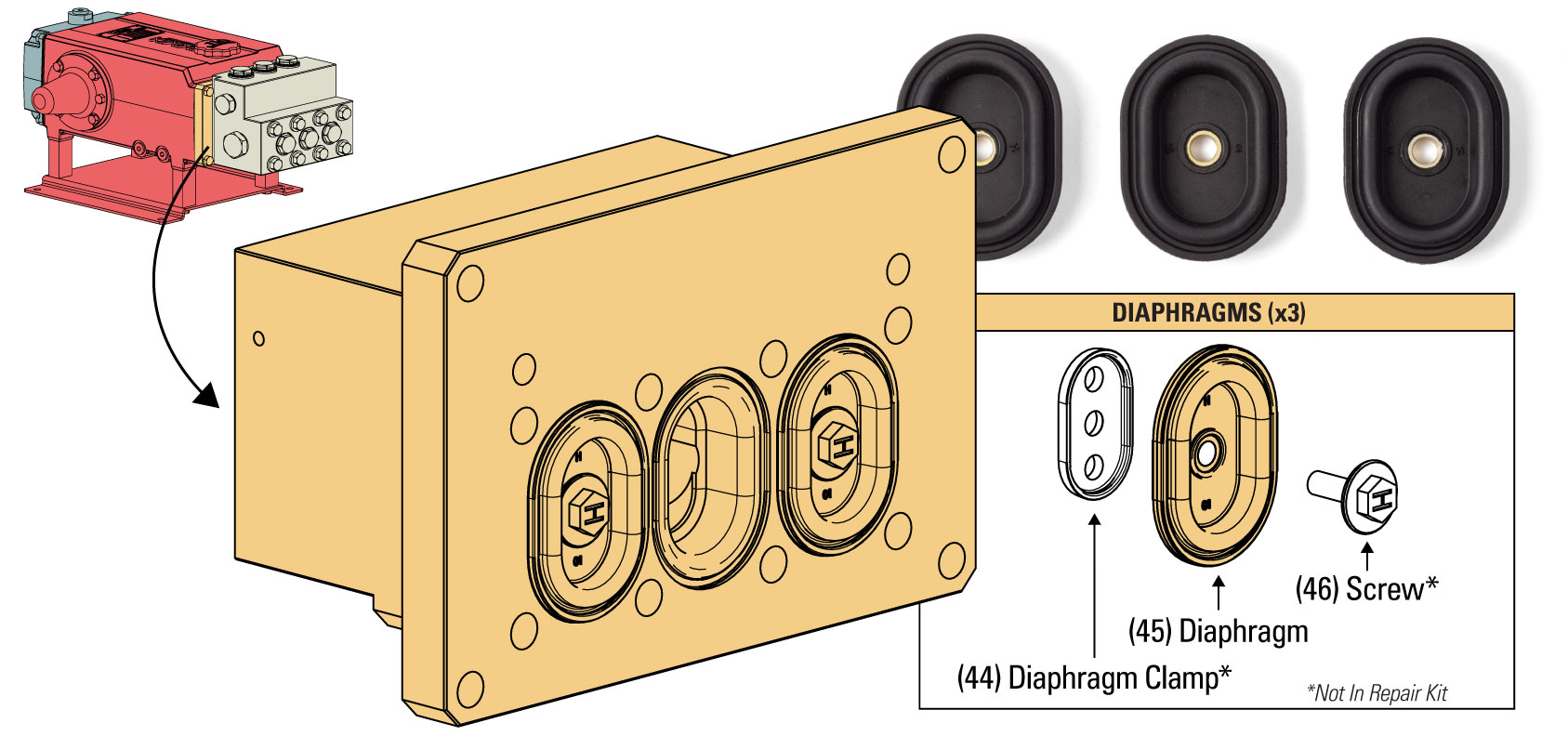
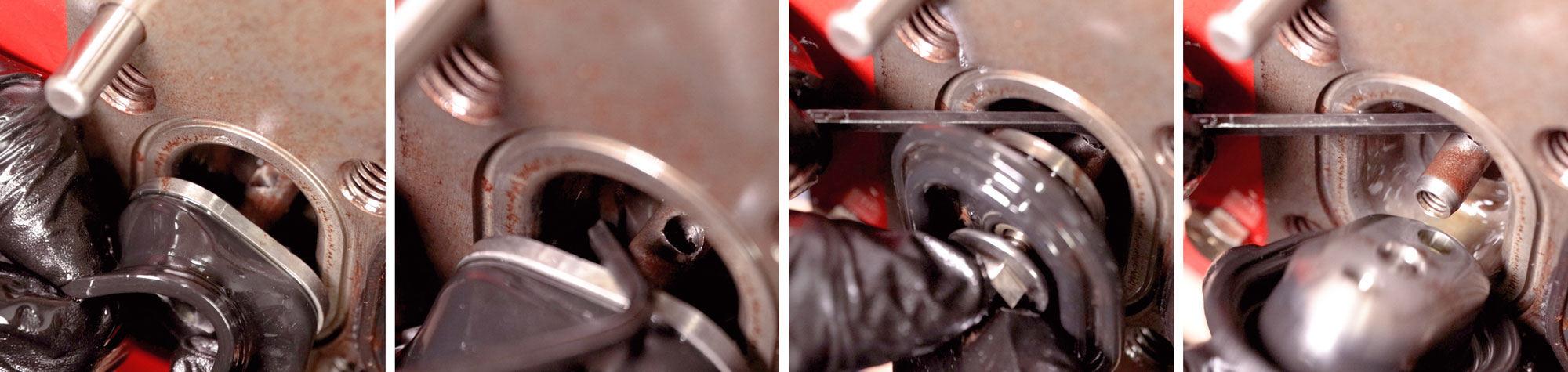
Next, we’ll remove the diaphragms.
- First, use a 10 mm wrench to loosen the screws. You’ll need to stabilize the shaft behind the diaphragm before you’ll be able to fully remove the screw.
- To do this, lift an edge of the diaphragm to expose the hole in the shaft behind the diaphragm.
Note: you may need to manually turn the pump shaft to move the diaphragm out farther to reach the hole.
- Insert a 1/8” hex wrench through the cross hole to keep the rod from spinning.
- Unthread the screw fully and remove the diaphragm.
- Keep the diaphragm clamps and bolts but discard the diaphragms.
- Repeat this for all three diaphragms.
Assembly: Diaphragms x3
- Place the diaphragm clamps on the new diaphragms.
- Apply blue medium Loctite on the screw threads and start it by hand.
- Use a 1/8” hex wrench to hold the shaft in place and tighten with a 10 mm socket to 60-in lb (5 ft lbs).
- Make sure the diaphragm is seated in the machined groove.
- Repeat this for all three diaphragms.
Assembly: Manifold
- Insert the eight bolts with washers into the manifold and tighten by hand.
- Start with the four center bolts and move outward in a crisscross pattern.
- Torque bolts to 50-ft lbs.
Assembly: Discharge (Outlet), Check Valves x3
- Place a backup ring over the outlet seat.
- Install the O-ring.
- Then the second backup ring. Make sure the cut portion of both backup rings are flush together.
- Place the outlet seat onto a slip-resistant surface and stack the valve disc and valve spring on top. The valve disc should be beveled side up.
- Align the tabs between the outlet plug and seat. Lock the pieces together by pushing them down firmly and then rotating the plug clockwise.
- Verify that the cut portion of both backup rings are still flush together and apply grease.
- Install the final O-ring on the plug.
- Apply anti-seize to the threads of the plug.
- Insert the assembly into the top of the manifold. Tighten until solid contact occurs.
- Repeat with all three outlet check valves.
Assembly: Suction (Inlet), Check Valves x3
Next, we’ll assemble and replace the inlet check valves.
- Place the retainer ring onto the seat.
- Add the valve disc, bevel side down, followed by the spring.
- Snap the spring retainer onto the seat under the groove.
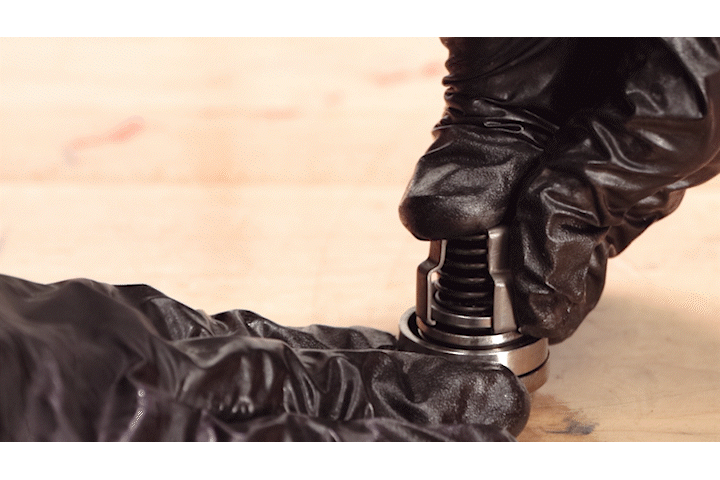
- Slide an O-ring over the seat
- Slide the retainer ring against the retainer and place a backup ring around the inlet seat.
- Next, install the O-ring on the inlet plug
- Add grease to the O-rings.
- Attach the valve inlet assembly to the inlet plug by twisting them together.
- Apply anti-seize to the threads of the plug.
- Insert the assembly into the front of the manifold. Tighten until solid contact occurs.
- Repeat with all three inlet check valves.
Oil & Start Up Procedures
Lastly, remove the oil cap and add 2.75 quarts (2.6 liters) of oil. Be sure the oil cap is clean before replacing it.
Before restarting the pump, be sure to follow all initial start-up instructions as listed in the technical documents for your model of pump.
For questions on this process or anything else about the Kimray Electric Glycol Pump, contact your local Kimray store or authorized distributor.