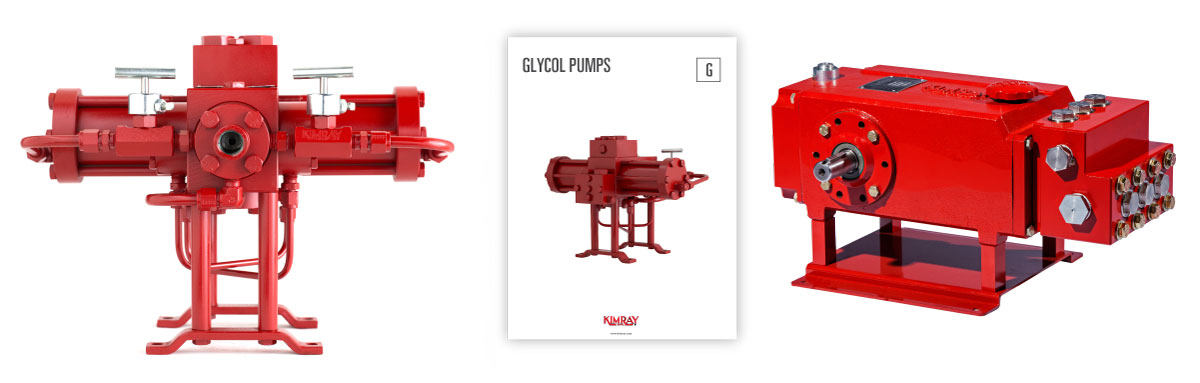
In this video, Kyle dives into the technical details of two vital components in the natural gas dehydration process: the Energy Exchange Glycol Pump and the Electric Glycol Pump.
These pumps are critical in ensuring the efficient operation of natural gas dehydration systems, which are essential for producing market-ready gas.
Understanding Natural Gas Dehydration
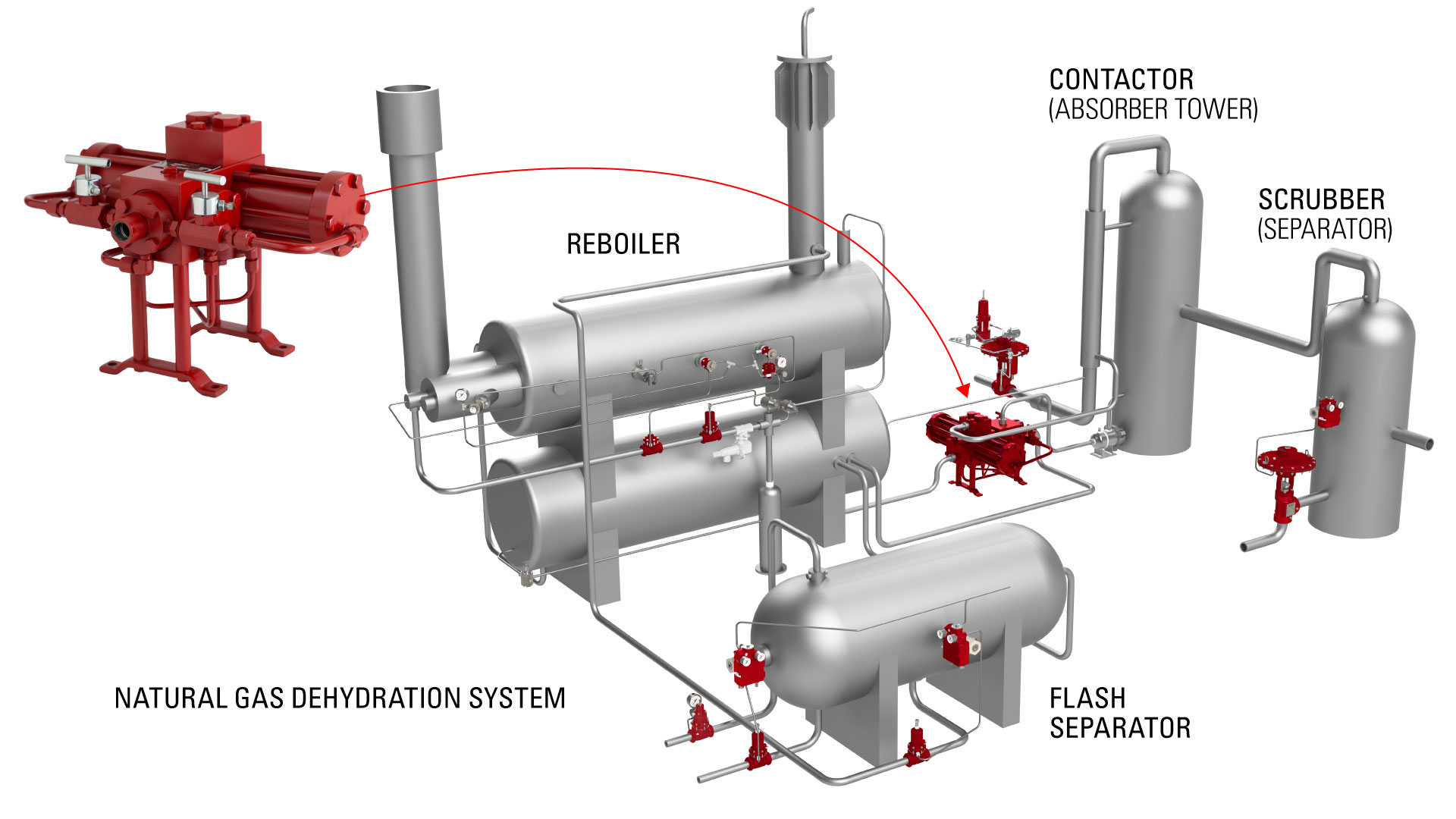
Natural gas dehydration is a crucial process in the treatment and preparation of natural gas for pipeline transportation and final use. The primary objective of this process is to remove water vapor from the gas stream. Water vapor in natural gas can cause several issues, including pipeline corrosion, hydrate formation, and reduced heating value.
These problems not only impact the safety and efficiency of gas transportation but can also lead to significant maintenance costs and operational downtime.
To avoid these issues, natural gas must be thoroughly dehydrated before it reaches the pipeline. This is where glycol dehydration systems, and more specifically glycol pumps, come into play.
Glycol dehydration is the most widely used method for removing water from natural gas, making the performance of these systems critical to the overall efficiency of gas processing operations.
The Energy Exchange Glycol Pump
Role in Natural Gas Dehydration
The Energy Exchange Glycol Pump is a key component in a natural gas dehydration system. It is designed to circulate triethylene glycol (TEG) through the system, enabling it to effectively remove water vapor from the gas stream.
TEG is a hygroscopic compound, meaning it has a strong affinity for water. When TEG is circulated through the dehydration system and comes into contact with wet, saturated gas, it absorbs the water vapor, thereby drying the gas.
How the Energy Exchange Pump Operates
The Energy Exchange Pump operates by utilizing the pressure in the contact tower to drive the movement of the pump and circulate glycol throughout the system. This pump is unique in that it does not require any external power source to operate. Instead, it harnesses the pressure from the contact tower to drive the pump, making it an energy-efficient option for natural gas dehydration.
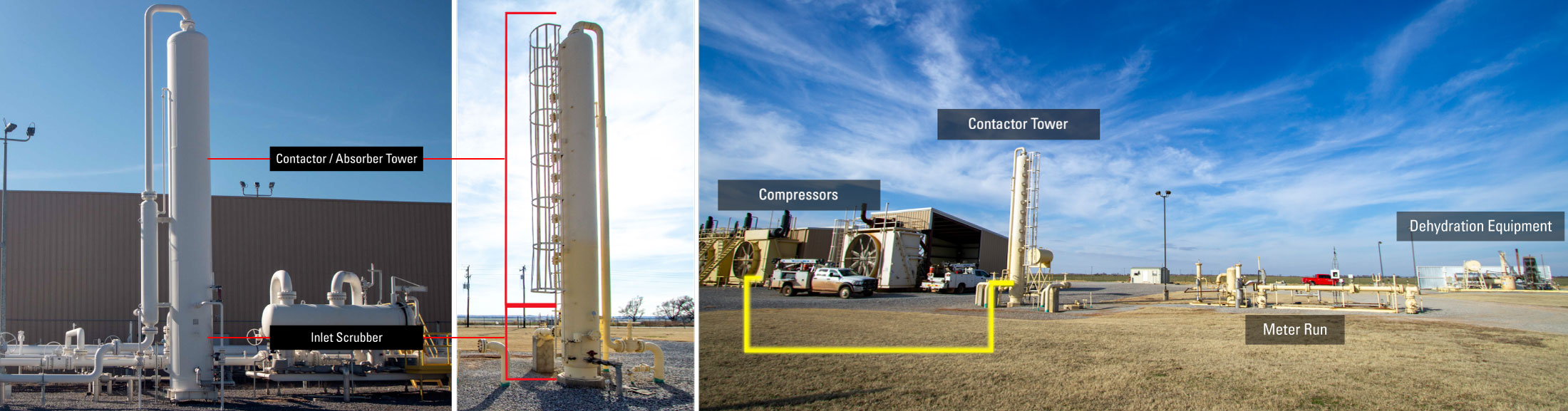
The pump works by exchanging the pressure in the contact tower for mechanical movement, which in turn circulates the glycol. This process is crucial because it ensures continuous circulation of glycol, which is necessary for maintaining the efficiency of the dehydration process.
The TEG absorbs water vapor from the gas stream, and the now water-rich glycol is then regenerated to remove the absorbed water, allowing the glycol to be reused in the system.
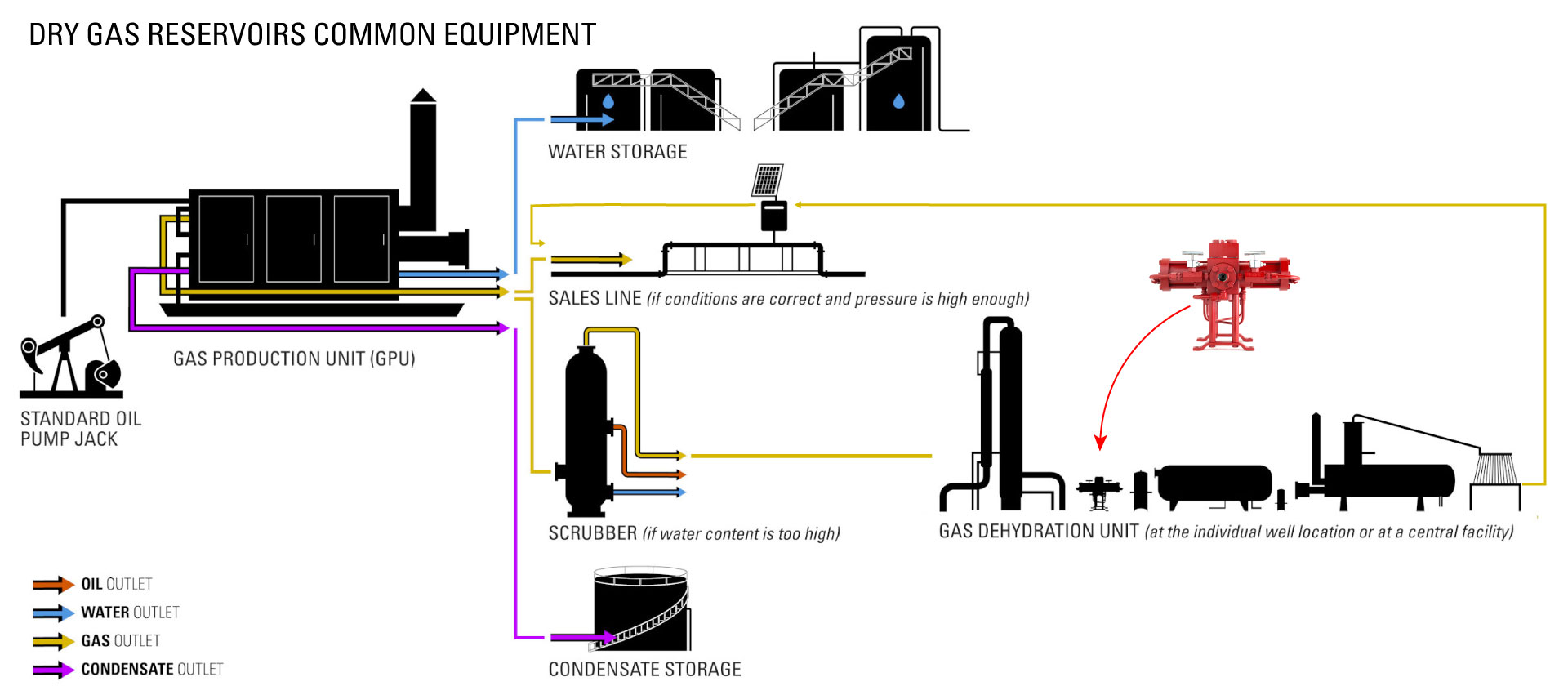
Components and Equipment
The Energy Exchange Glycol Pump is just one part of a larger system designed to remove water vapor from natural gas. The system typically includes several key components:
Inlet Scrubber
The inlet scrubber is the first piece of equipment that the gas encounters in the dehydration system. Its primary function is to remove any free liquids or large particles from the gas stream before it enters the contact tower. This step is crucial in preventing damage to the downstream equipment and ensuring the efficiency of the dehydration process.
Contact Tower
The contact tower, also known as the absorber, is where the actual dehydration process takes place. The gas flows through the contact tower, where it comes into contact with the circulating TEG. The TEG absorbs the water vapor from the gas, effectively drying it before it exits the tower.
Flash Separator
The flash separator is used to separate the gas that is entrained in the glycol from the liquid phase. This step is important because it helps to reduce the amount of gas that is carried with the glycol as it moves through the system, minimizing emissions and improving the efficiency of the dehydration process.
Glycol Regenerator
After the TEG has absorbed water vapor from the gas stream, it needs to be regenerated before it can be reused. The glycol regenerator removes the absorbed water from the TEG, allowing it to be recirculated through the system.
energy exchange flow graphics
System Configuration
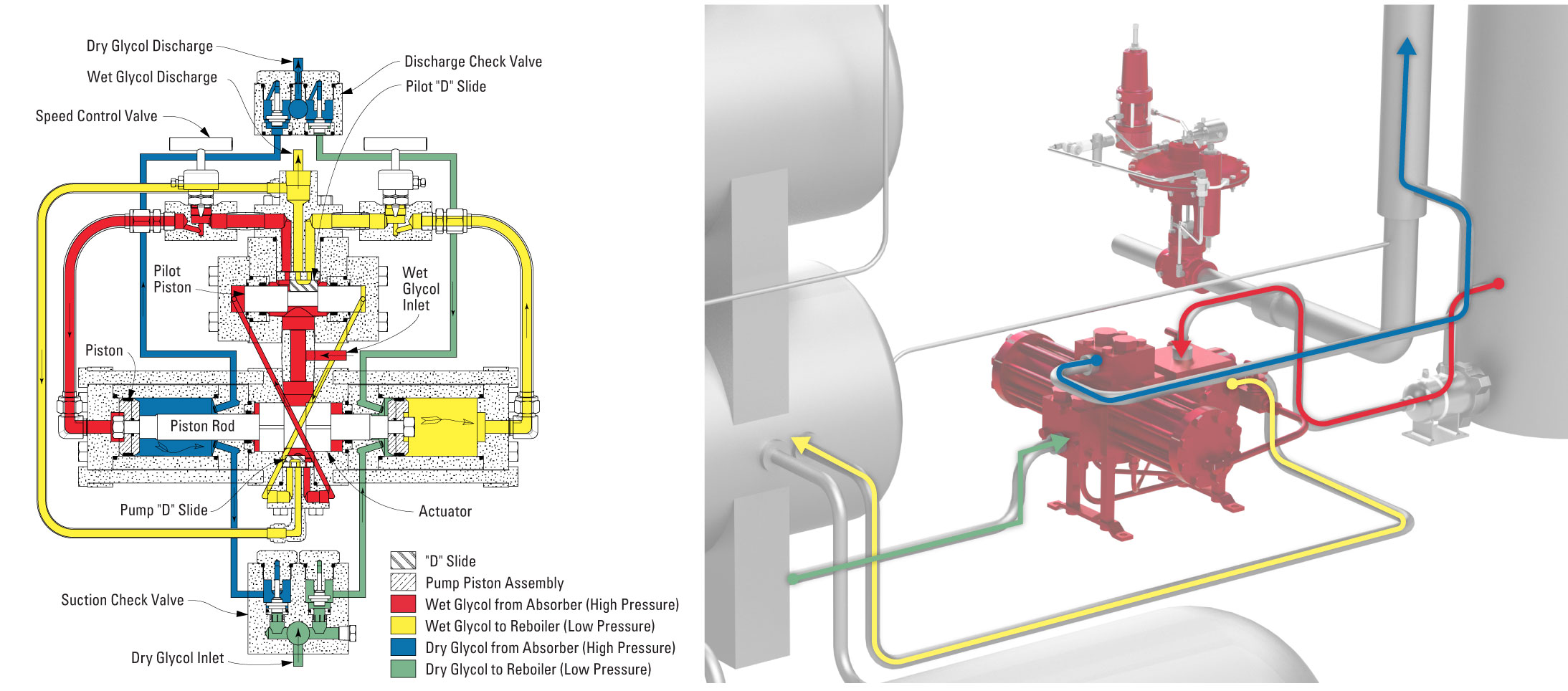
The configuration of a natural gas dehydration system can vary depending on the specific application and the amount of gas that needs to be processed. In some cases, the equipment is installed directly at the well location, with one dehydration system per well. This setup is common in areas where the gas production is relatively low and the equipment can be kept compact.
In other cases, the dehydration system is part of a gas gathering system, where gas from multiple wells is collected and processed at a central location. These systems are typically larger and can handle much higher volumes of gas. The size of the system can range from handling as little as half a million cubic feet of gas per day to as much as 30 to 40 million cubic feet per day.
Regardless of the size, the basic principles of operation remain the same; it is the scale of the equipment that changes to accommodate the volume of gas being processed.
Operating an Energy Exchange Glycol Pump
Pressure Dynamics and Pump Operation
Pressure Exchange Mechanism
The Energy Exchange Pump is called such because it utilizes the pressure from the contact tower to drive the pump. This pressure exchange mechanism is what makes the pump so efficient, as it does not require any external power source to operate. The pressure in the contact tower forces the glycol through the system, driving the pump's mechanical components and ensuring continuous circulation of the glycol.
Operating Pressures and System Compatibility
Our PV Energy Exchange Pump is capable of operating at pressures up to 2,000 PSI. This makes it suitable for a wide range of natural gas dehydration systems, from small, low-pressure systems to large, high-pressure systems. For lower pressure applications, we offer the Small Cylinder (SC) Pump, which operates at pressures below 500 PSI.
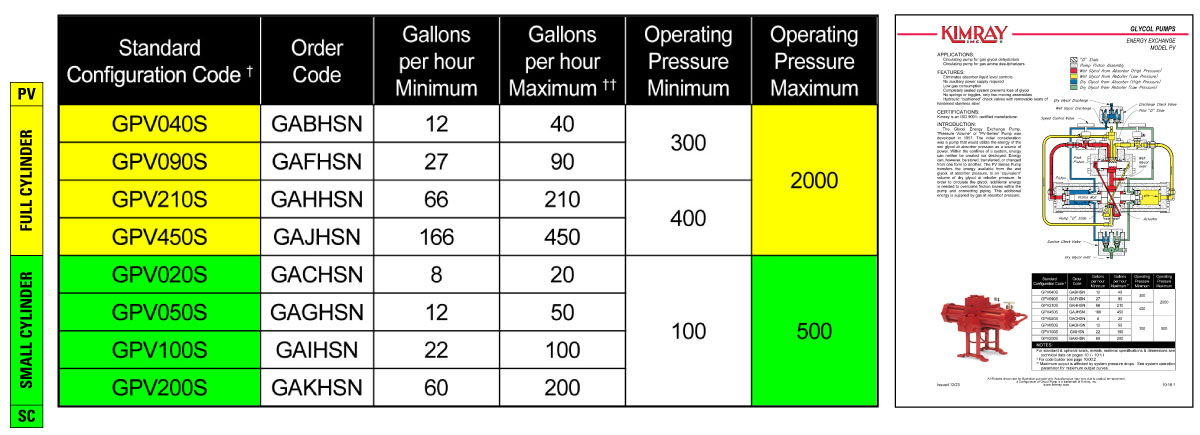
The typical operating pressure for a natural gas dehydration system is around 1,000 to 1,500 PSI. This pressure is sufficient to drive the pump and circulate the glycol through the system, ensuring efficient dehydration of the gas. The choice of pump depends on the specific operating pressures of the system and the volume of gas being processed.
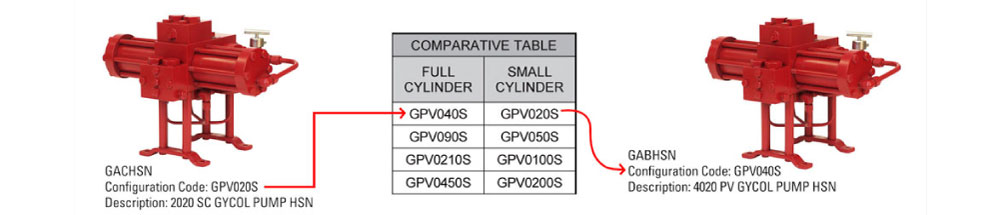
Gas Consumption and Emissions
Understanding Gas Consumption Rates
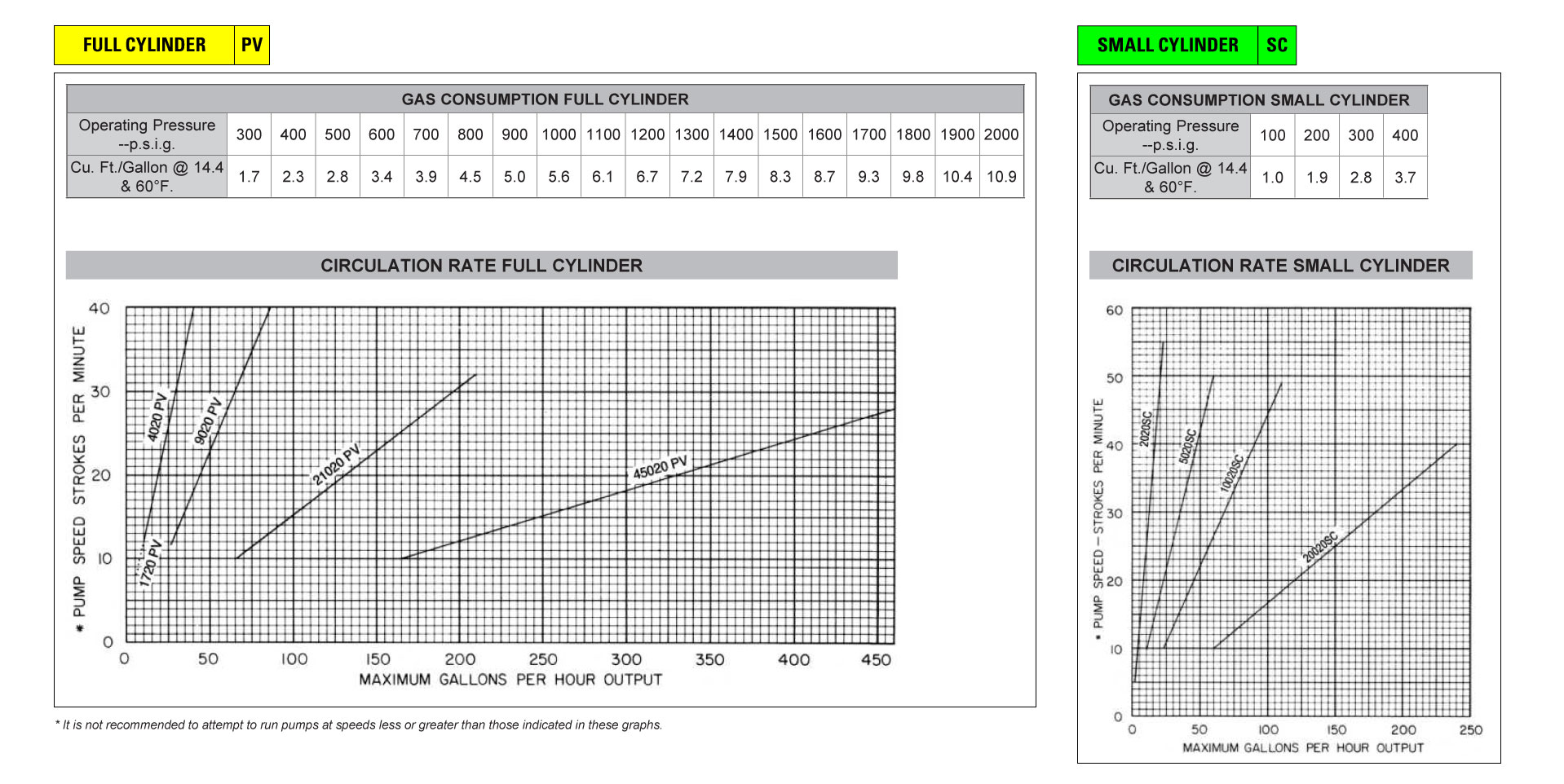
One of the critical factors to consider when operating the Energy Exchange Glycol Pump is the gas consumption rate. Each pump size has a different gas consumption rate, which refers to the amount of gas that is used by the pump to operate. This gas is typically entrained in the glycol and is later separated in the flash separator.
Understanding the gas consumption rate is important for several reasons.
First, it impacts the overall efficiency of the system. The more gas that is consumed by the pump, the less gas is available for sale, which can affect the profitability of the operation.
Second, the gas that is consumed by the pump must be accounted for in emissions calculations, as it may be vented or flared during the process.
Managing Emissions
Gas emissions are a concern in many natural gas processing operations, particularly in regions with strict environmental regulations.
The gas consumed by the Energy Exchange Glycol Pump is typically vented or flared after it is separated from the glycol in the flash separator. However, some operators may choose to capture and recompress this gas for use elsewhere in the system, reducing emissions and improving overall efficiency.
To help operators manage emissions, we provide charts that detail the gas consumption rates for each size of Energy Exchange Glycol Pump. These charts allow operators to calculate the expected gas consumption for their specific system and plan accordingly.
Sizing and Adjusting the Glycol Pump
Sizing Considerations
Factors Affecting Pump Sizing
Proper sizing of the Energy Exchange Glycol Pump is critical for ensuring efficient operation of the natural gas dehydration system. Several factors must be considered when sizing the pump, including:
- Operating Pressure in the Contact Tower
The pressure in the contact tower is one of the primary factors that determine the size of the pump. Higher pressures typically require larger pumps to handle the increased volume of glycol that needs to be circulated.
- Allowable Water Content
The allowable water content in the gas stream is another critical factor. This is typically measured in pounds of water per million cubic feet of gas. The lower the allowable water content, the more glycol needs to be circulated to remove the required amount of water.
- Glycol-to-Water Ratio
The glycol-to-water ratio is a measure of how much glycol is required to remove a given amount of water from the gas stream. Newer, more efficient glycol may require less circulation, while older or contaminated glycol may require more.
- Gas Temperature
The temperature of the gas at the contact tower also affects the sizing of the pump. Higher temperatures may require more glycol circulation to achieve the desired level of dehydration.
Using the Glycol Sizing Calculator
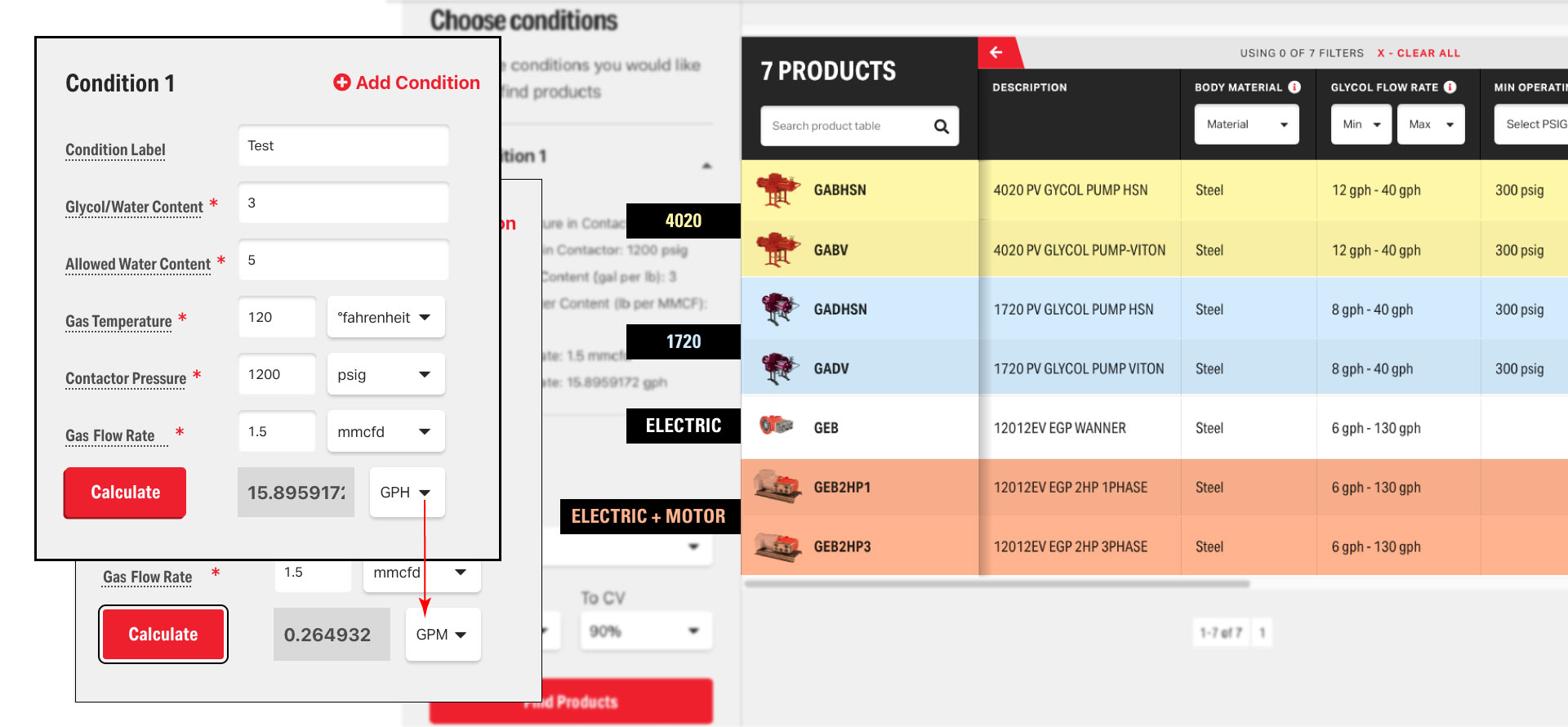
To assist with pump sizing, we offer a Glycol Sizing Calculator that takes these factors into account. By inputting the operating pressure, allowable water content, glycol-to-water ratio, and gas temperature, the calculator provides a recommended glycol flow rate.
This flow rate is typically expressed in gallons per hour (GPH), which can then be converted to gallons per minute (GPM) if needed.
Once you have determined the required flow rate, you can use our product finder to select the appropriate size Energy Exchange Glycol Pump. Our pumps are labeled with their maximum flow rates in gallons per hour, making it easy to match the pump to your specific needs.
Adjusting Pump Speed and Flow Rate
Speed Adjustment Valves
The speed of the Energy Exchange Glycol Pump is controlled by two needle valves located on the pump. These valves allow you to adjust the speed of the pump, which in turn adjusts the flow rate of the glycol. It’s important to adjust these valves evenly to ensure that the pump operates smoothly and without issues.
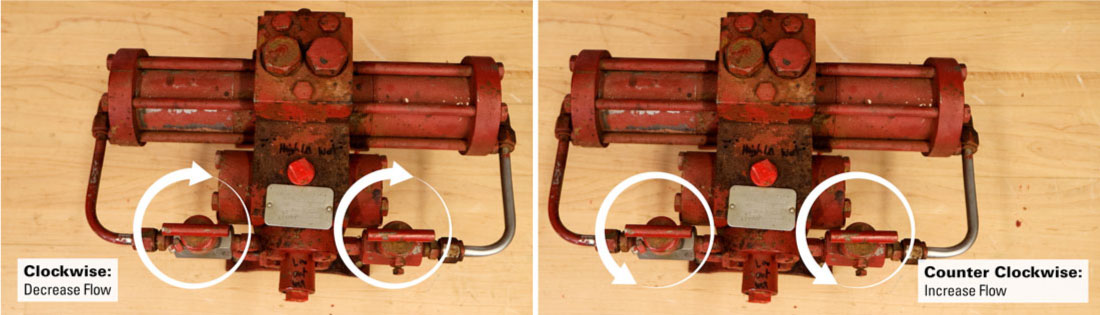
If the valves are adjusted unevenly, it can cause the pump to stroke unevenly, leading to excessive wear and tear on the pump components. Over time, this can result in decreased efficiency and potentially costly repairs.
Monitoring and Adjusting for Optimal Performance
Once the pump is installed and operating, it’s important to monitor its performance regularly. This includes checking the pressure in the contact tower, the flow rate of the glycol, and the condition of the pump components.
If you notice any issues, such as a decrease in flow rate or an increase in noise from the pump, it may be necessary to make further adjustments.
One of the most common issues that can arise is the pump stalling. This can occur if the operating pressure in the contact tower drops below the minimum required pressure for the pump, or if there is excessive friction loss in the system.
If your pump stalls, you should check the filters, pressure drops, and overall system health to identify and resolve the issue.
The Importance of Filtration in Dehydration Systems
Protecting Your Equipment
Filtration is a crucial aspect of maintaining the health and efficiency of a natural gas dehydration system. The TEG that circulates through the system not only absorbs water vapor but can also pick up contaminants from the gas stream.
These contaminants can include solid particles, hydrocarbons, and other impurities that can cause damage to the pump and other components if not properly filtered out.
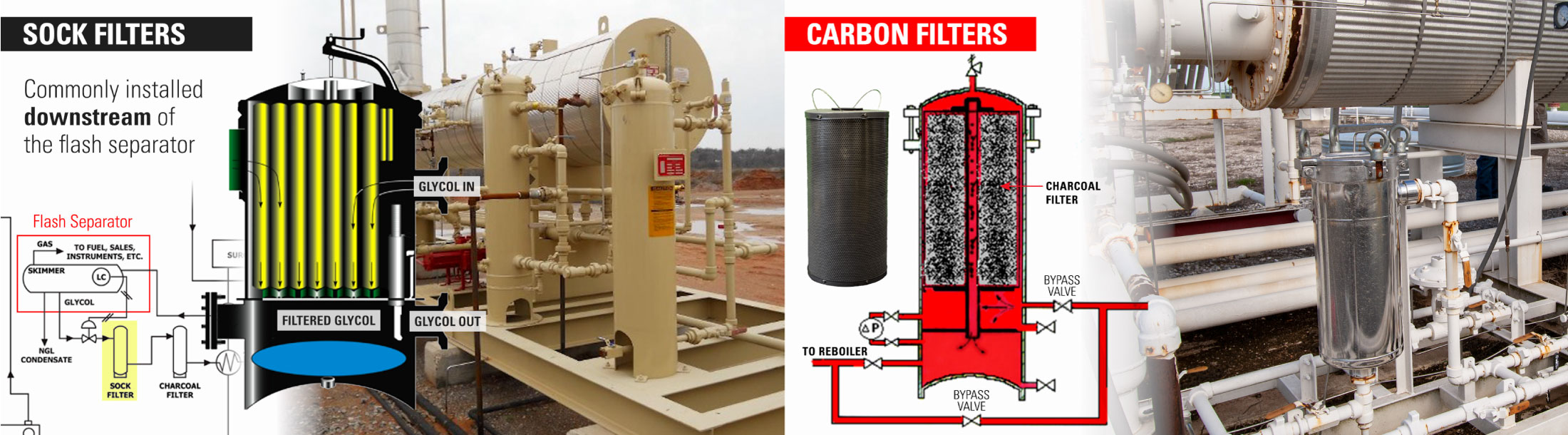
There are several types of filters used in a natural gas dehydration system:
Solid Particle Filters
These filters are designed to remove solid particles from the glycol, such as sand, rust, and other debris. Solid particles can cause abrasion and wear on the pump components, leading to decreased efficiency and potential failure.
Hydrocarbon Filters
Hydrocarbon filters are used to remove hydrocarbons from the glycol. Hydrocarbons can contaminate the glycol, reducing its effectiveness in absorbing water vapor and potentially causing damage to the pump and other components.
Coalescing Filters
Coalescing filters are used to remove fine droplets of liquid from the gas stream. These filters help to ensure that only dry gas enters the contact tower, improving the efficiency of the dehydration process.
Maintenance and Replacement
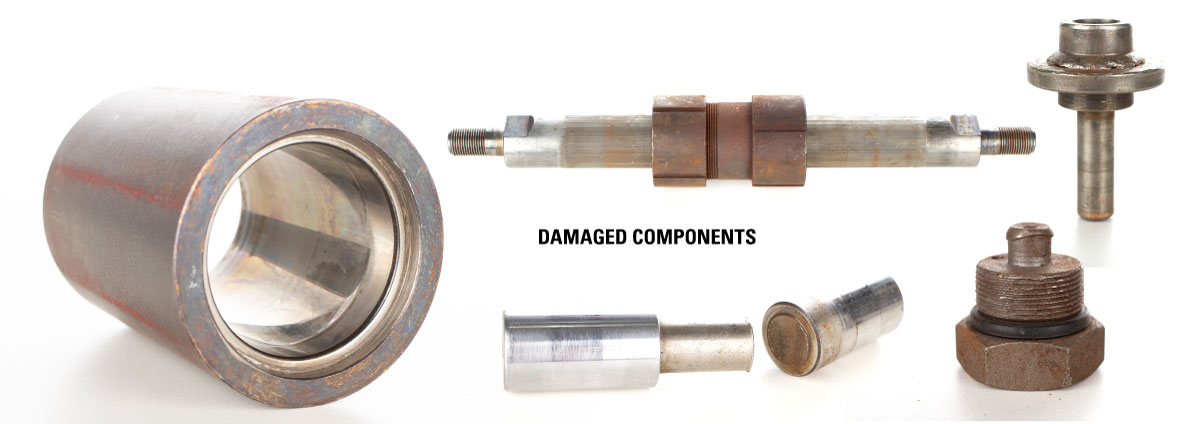
Regular maintenance and replacement of filters are essential for ensuring the long-term health of your dehydration system. Filters should be checked regularly for signs of wear or contamination and replaced as needed.
The frequency of replacement will depend on the specific conditions of your system, including the quality of the gas being processed and the amount of contaminants present.
It’s also important to monitor the differential pressure across the filters. If the differential pressure becomes too high, it can indicate that the filter is becoming clogged and needs to be replaced. High differential pressure can also increase the load on the pump, leading to increased wear and tear on the components.
Repair and Maintenance of the Energy Exchange Glycol Pump
Repair Options
When it comes time to repair your Energy Exchange Glycol Pump, you have a couple of repair options:
1. Send the pump to a Kimray store for repair.
Our stores are equipped with the tools and expertise needed to repair your pump and restore it to like-new condition. When you send your pump to us for repair, it comes with a new warranty, giving you peace of mind that the pump will operate reliably once it’s back in service.
2. Repair the pump yourself using a repair kit.
We offer repair kits for all of our Energy Exchange Glycol Pumps, which include the necessary seals, gaskets, and other components needed to complete the repair. If you choose to repair the pump yourself, be sure to follow the instructions provided with the kit and take care to properly align and install all components to ensure a successful repair.
Common Repair Issues
There are a few common issues that can arise with the Energy Exchange Glycol Pump that may require repair:
Seal Wear
Over time, the seals in the pump can wear out, leading to leaks and decreased efficiency. Replacing the seals is a common repair that can help restore the pump to full operation.
Valve Wear
The valves in the pump can also wear out over time, leading to uneven operation and decreased efficiency. Replacing the valves is another common repair that can help improve the performance of the pump.
Cylinder Wear
In some cases, the cylinders in the pump can become worn, leading to decreased efficiency and potential failure. If the cylinders are worn, they may need to be replaced to restore the pump to full operation.
Glycol Pump Exchange Program
In addition to repair services, many of our Kimray store locations offer an exchange program for glycol pumps. The exchange program is designed to minimize downtime and get you back in operation as quickly as possible. Here’s how it works:
Bring in Your Pump
If your pump needs repair, you can bring it to a participating Kimray store location. Instead of waiting for your pump to be repaired, you can exchange it for a repaired pump of the same size.
Immediate Service
The repaired pump is ready to go, so you can immediately take it back to your location and install it in your system. This eliminates the need to wait for repairs to be completed and allows you to get back in operation more quickly.
Warranty Coverage
The repaired pump comes with a new warranty, giving you peace of mind that it will operate reliably once it’s back in service.
The Electric Glycol Pump
Advantages of the Electric Glycol Pump
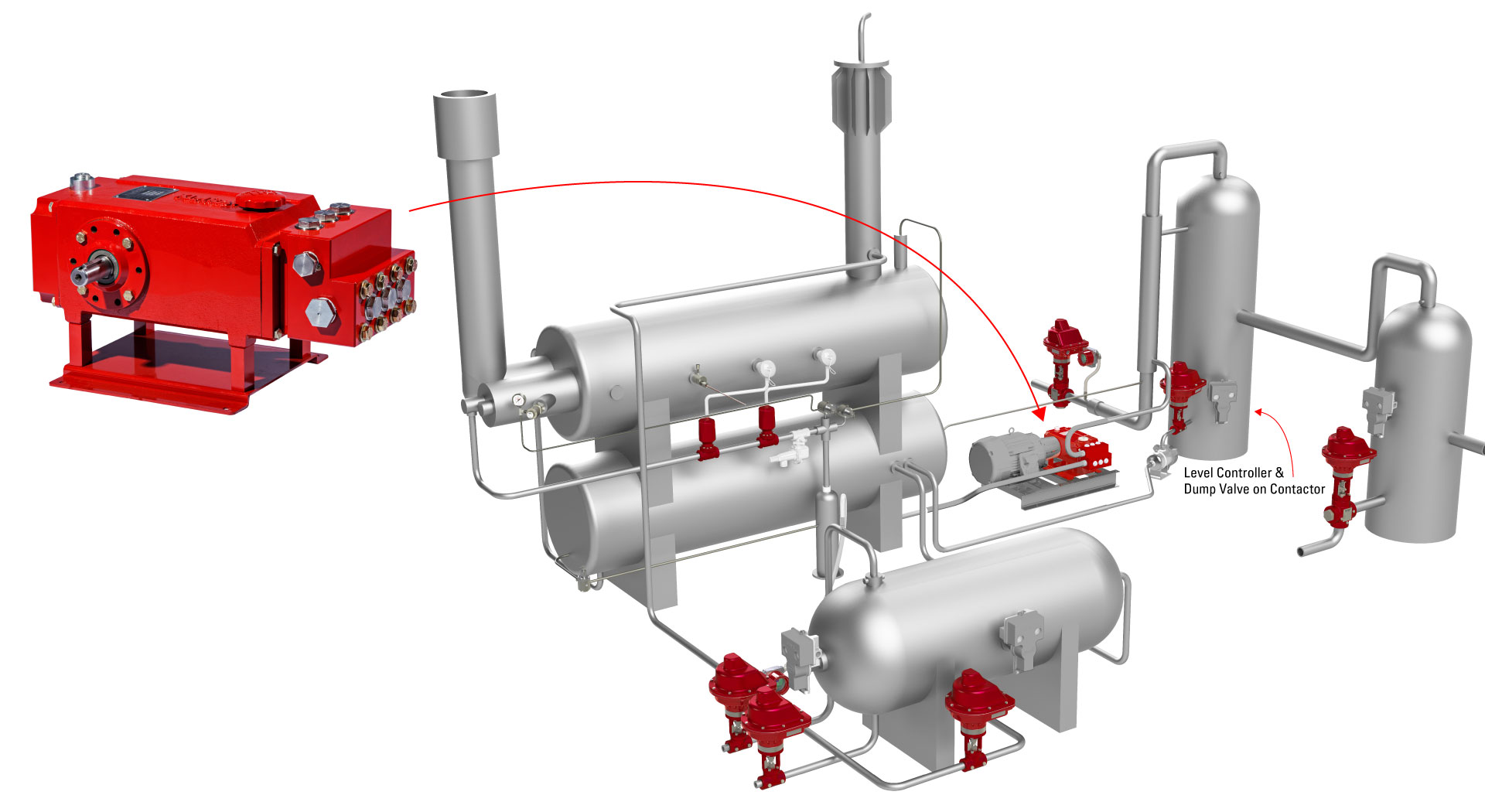
Energy Efficiency and Emissions
The Electric Glycol Pump offers several advantages over the Energy Exchange Glycol Pump, particularly in terms of energy efficiency and emissions. One of the most significant advantages is that the Electric Glycol Pump does not consume gas.
This means that there is no need to account for gas consumption in your emissions calculations, making it an attractive option for operators looking to minimize their environmental impact.
Improved Pump Life
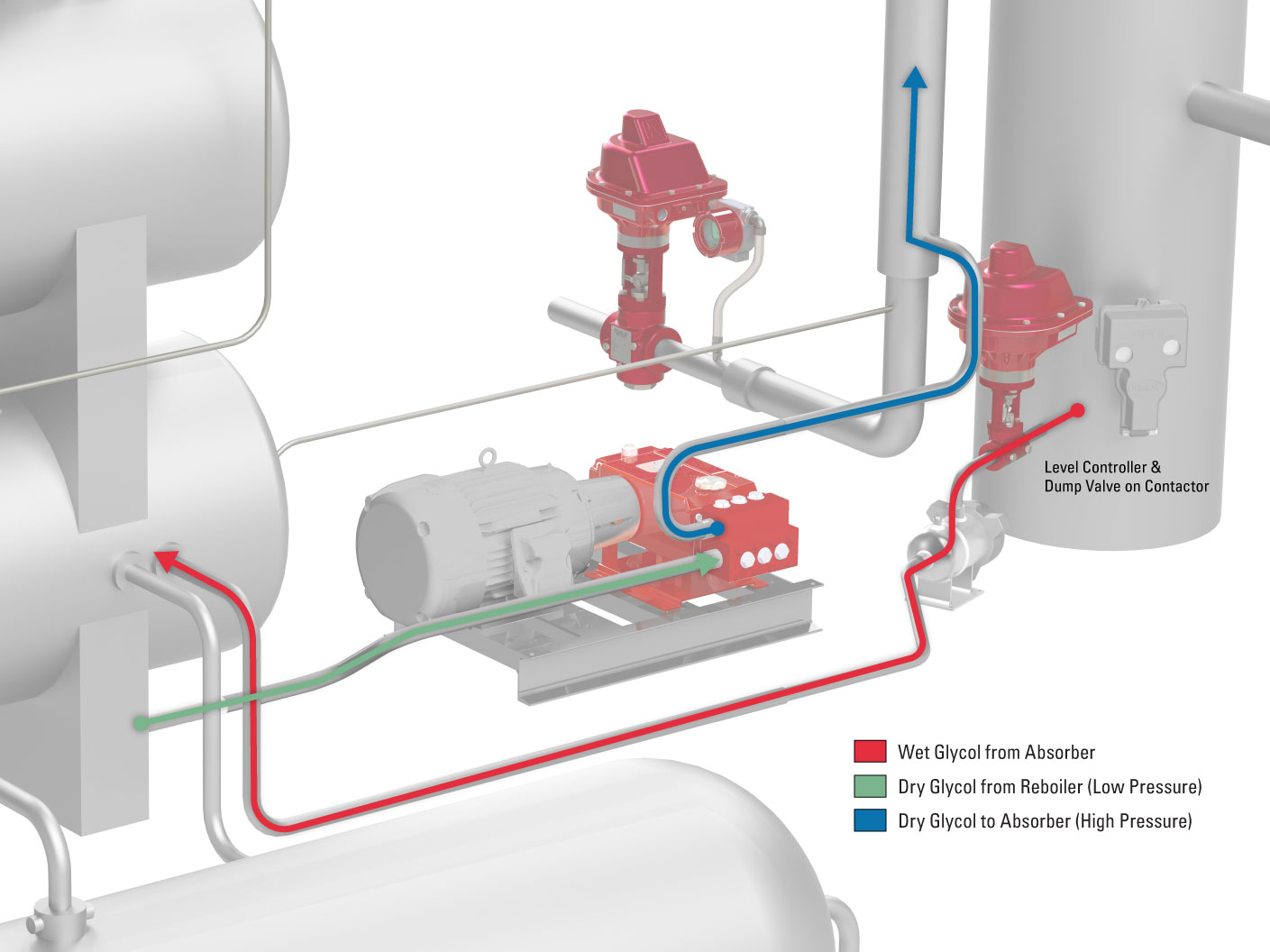
Another advantage of the Electric Glycol Pump is that only dry glycol passes through the pump. This reduces the amount of contamination that the pump is exposed to, which can significantly extend the life of the pump. By minimizing the exposure to contaminants, the Electric Glycol Pump can operate more efficiently and with less maintenance than the Energy Exchange Pump.
System Requirements and Configuration
Level Control and Dump Valve
An electric glycol system requires a level control and a dump valve on the contact tower. The level control is used to monitor the level of glycol in the tower and ensure that it remains within the desired range. The dump valve is used to remove the water-rich glycol from the tower and send it to the regenerator for processing.
Contamination Management
In an electric glycol system, the wet glycol, which contains most of the contaminants, does not pass through the pump. This helps to reduce the amount of contamination that the pump is exposed to, which can extend its life and improve its efficiency. However, it’s still important to use proper filtration to remove contaminants from the glycol before it enters the regenerator.
No Minimum Operating Pressure
Unlike the Energy Exchange Glycol Pump, which requires a minimum operating pressure to function, the Electric Glycol Pump can operate at any pressure, even down to 0 PSI. This makes it a versatile option for a wide range of applications, from low-pressure systems to high-pressure systems.
Sizing and Motor Selection
Sizing the Electric Glycol Pump
Just like with the Energy Exchange Glycol Pump, proper sizing of the Electric Glycol Pump is critical for ensuring efficient operation. The size of the pump should be based on the operating pressure of the system, the flow rate of the glycol, and the specific requirements of the application.
Motor Selection
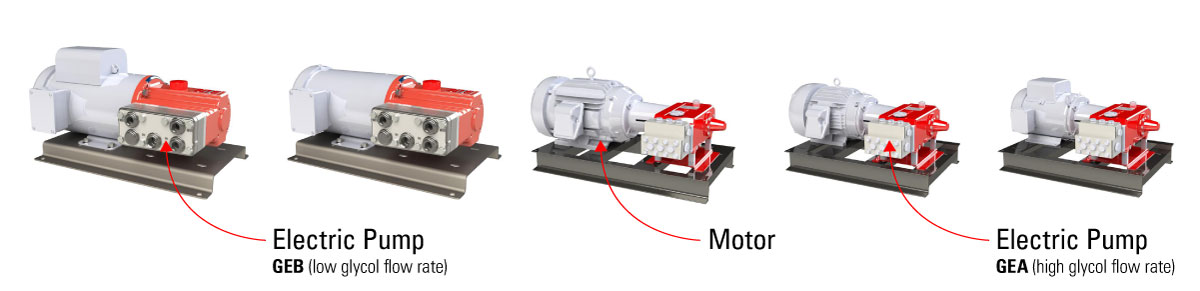
One of the most important considerations when installing an Electric Glycol Pump is selecting the appropriate motor. The motor must be sized to handle the flow rate and pressure of the system.
As the operating pressure increases, so does the required horsepower for the motor. It’s important to select a motor that is capable of handling the maximum operating pressure of the system to ensure reliable operation.
Monitoring and Maintenance
Once the Electric Glycol Pump is installed and operating, it’s important to monitor its performance regularly. This includes checking the pressure in the system, the flow rate of the glycol, and the condition of the motor.
If you notice any issues, such as a decrease in flow rate or an increase in noise from the motor, it may be necessary to make further adjustments or perform maintenance.
Whether you’re looking to reduce emissions, improve pump life, or optimize the efficiency of your dehydration system, understanding the operation and maintenance of these pumps is key.
To speak with an expert about your glycol pumps or glycol dehydration needs, contact your local Kimray store or authorized distributor.