In this article and video, we discuss Kimray low pressure control valves.
If you would like more training on this in person, please visit the training page on our website. There you can find more information about how we can come out to your place, or you can come to a Kimray store and receive training.
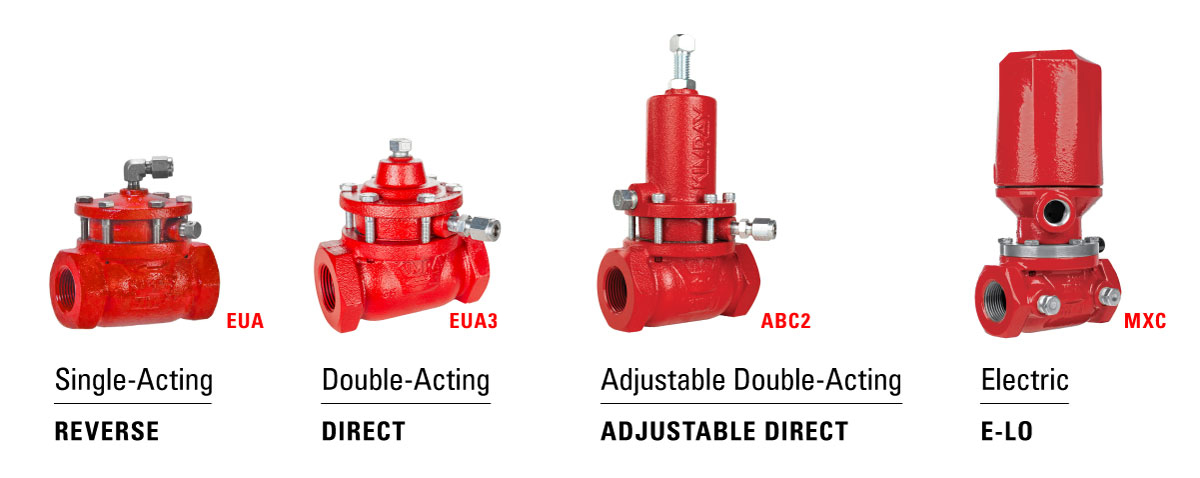
The four products we're going to talk about today are:
- Pneumatic Single Acting
- Pneumatic Double Acting
- Pneumatic Adjustable Double Acting
- Electric Low Pressure Control Valve (ELO)
Each one of the pneumatic low pressure control valves might be named something slightly different depending on the technical document you're looking at.
The language I've always used is single, double, and adjustable double acting. Single acting could be called reverse, double acting is sometimes known as direct, and adjustable double acting is sometimes known as adjustable direct. Just keep that in mind, but I always use the single, double, and adjustable double acting language.
Single-Acting (Reverse) Low Pressure Control Valve
The first one we're going to look at is the single-acting low pressure control valve.
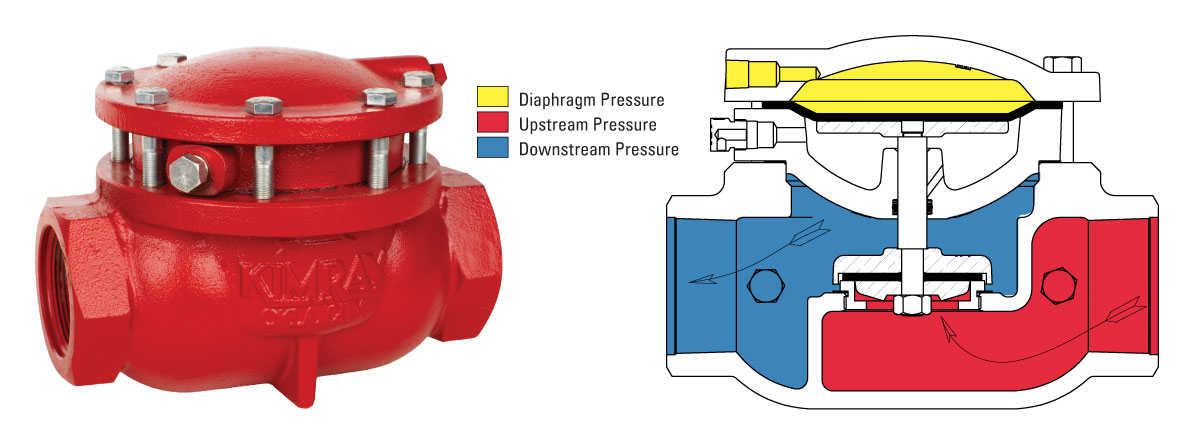
You would use this in applications where you want a fail-open valve or any time there is a pneumatic signal to the valve. You want that valve to be in the closed position. The pneumatic signal goes to the top of the valve actuator, and that pressure will hold the valve in the closed position.
By low pressure, I mean below 300 PSI. Normally, these first three products we're going to talk about are used in even lower pressures than that, usually below 30 PSI going through these valves. It's important to keep in mind that the operating pressure or the pressure inside of the valve cannot be more than double your supply pressure because the area of the actuator is twice that of the valve seat.
For example, let's say we have 10 PSI in the valve body. That means you need at least five pounds of pneumatic pressure to hold that valve in the closed position. If you had 20 lbs of pressure in the valve body going from upstream to downstream and only 5 PSI of pneumatic signal, that valve would not seal properly. With the single acting, you just need to make sure that your supply pressure is sufficient to hold that valve in the closed position. A possible cause for a leaking valve could be that your pneumatic signal is not strong enough to hold it in the closed position.
The single-acting valve should operate well for a long time as long as you don't have any acid gases like H2S or CO2, which can deteriorate the elastomers in the valve and cause premature failure. If you have those types of acid gases, make sure you're using the appropriate elastomer that will stand up to those conditions.
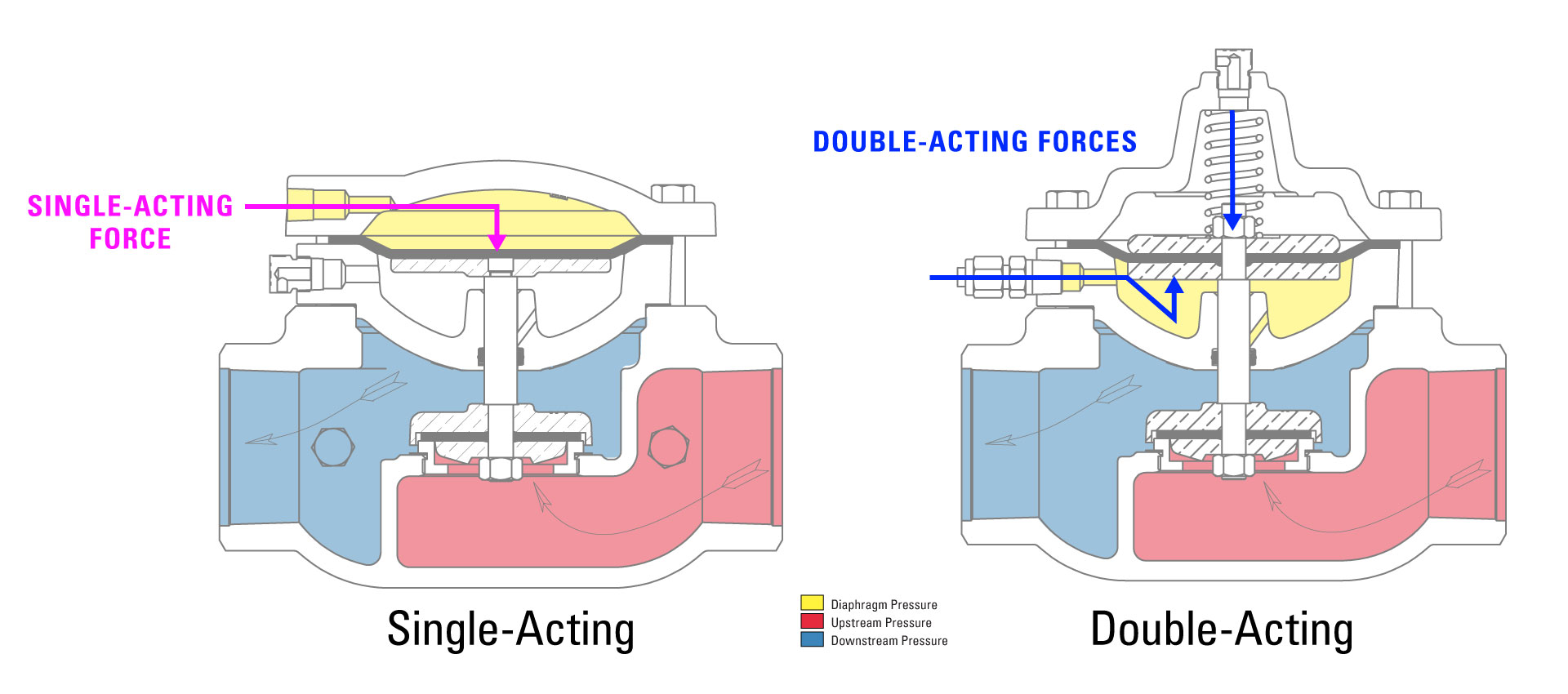
The single-acting valve is called single-acting because there is a single force put against this valve in comparison with the ones with the springs. There is one force on one side of the diaphragm, which is the pneumatic signal pushing it to a certain position.
Double-Acting (Direct) Low Pressure Control Valve
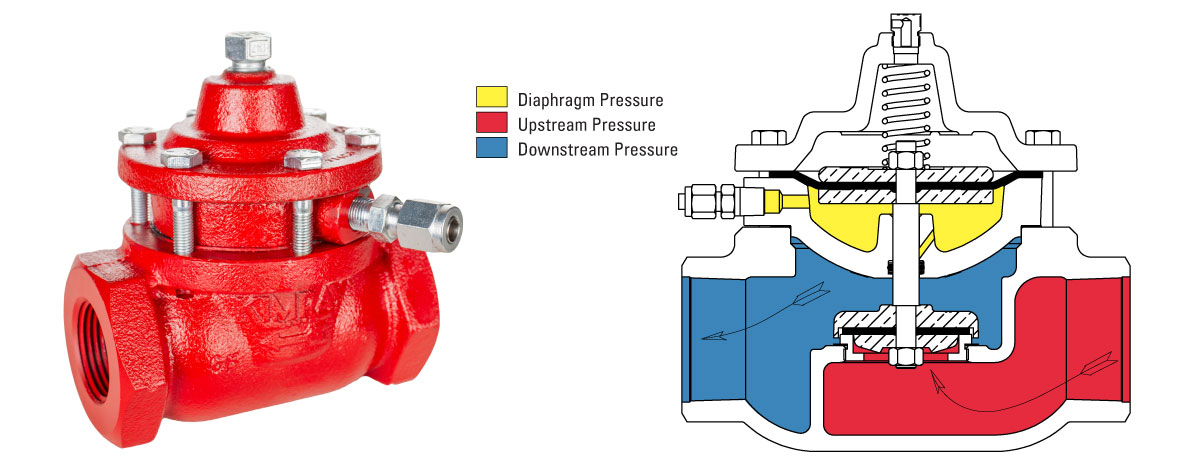
Next up, we have the double-acting valve.
This valve has a pneumatic signal that comes underneath the diaphragm, and it also has a spring on the opposite side of that diaphragm. There are two forces acting against one another, which is why we call it a double-acting valve.
You can use this valve in gas or liquid applications. The pneumatic signal coming to this valve could be from some kind of pilot, like a temperature controller, or a liquid level controller or switch. It just needs that pneumatic signal to actuate the valve.
In the rendering here, pressure opens the valve, and the valve spring makes it a fail-closed valve. Without a pneumatic signal on this valve, the spring would then force it closed.
There are a few different spring options for these valves, so depending on your operating pressure, you want to make sure you have the appropriate spring inside this valve. This way, it can close against that upstream pressure, whether you're operating on relatively low pressure like below 5 or 6 PSI, or up to 35 PSI. You want to make sure you have the correct spring in there.
The single acting is more or less fail-open because if you remove that pneumatic signal, the upstream pressure is going to push the valve open. If you want the failure position of the valve to be open, or you want the valve to remain closed as long as it has a pneumatic signal, go with a single-acting valve.
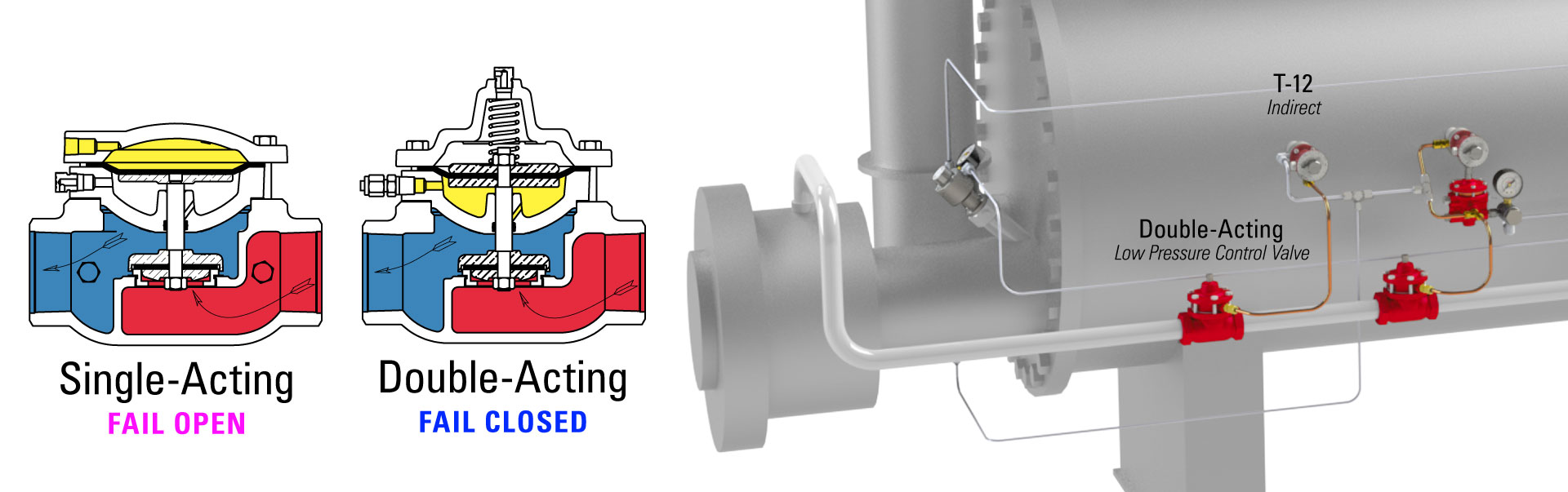
If you want the failure position to be closed, go with the double-acting valve because it has a spring in the actuator that will force it closed without a pneumatic signal.
For example, the double-acting valve can be used in burner valve applications. You might have a T12 thermostat monitoring vessel temperature, and when it gets below its set point, you need the vessel to heat back up. The output from the T12 goes to the burner valve, a low pressure control valve.
The pneumatic signal opens the burner valve, allowing fuel to go to the burner to increase the temperature. The T12 itself is indirect acting in that application, and it’s going to a double-acting burner valve, opening it up to allow the fuel through.
Adjustable Double-Acting Low Pressure Control Valve
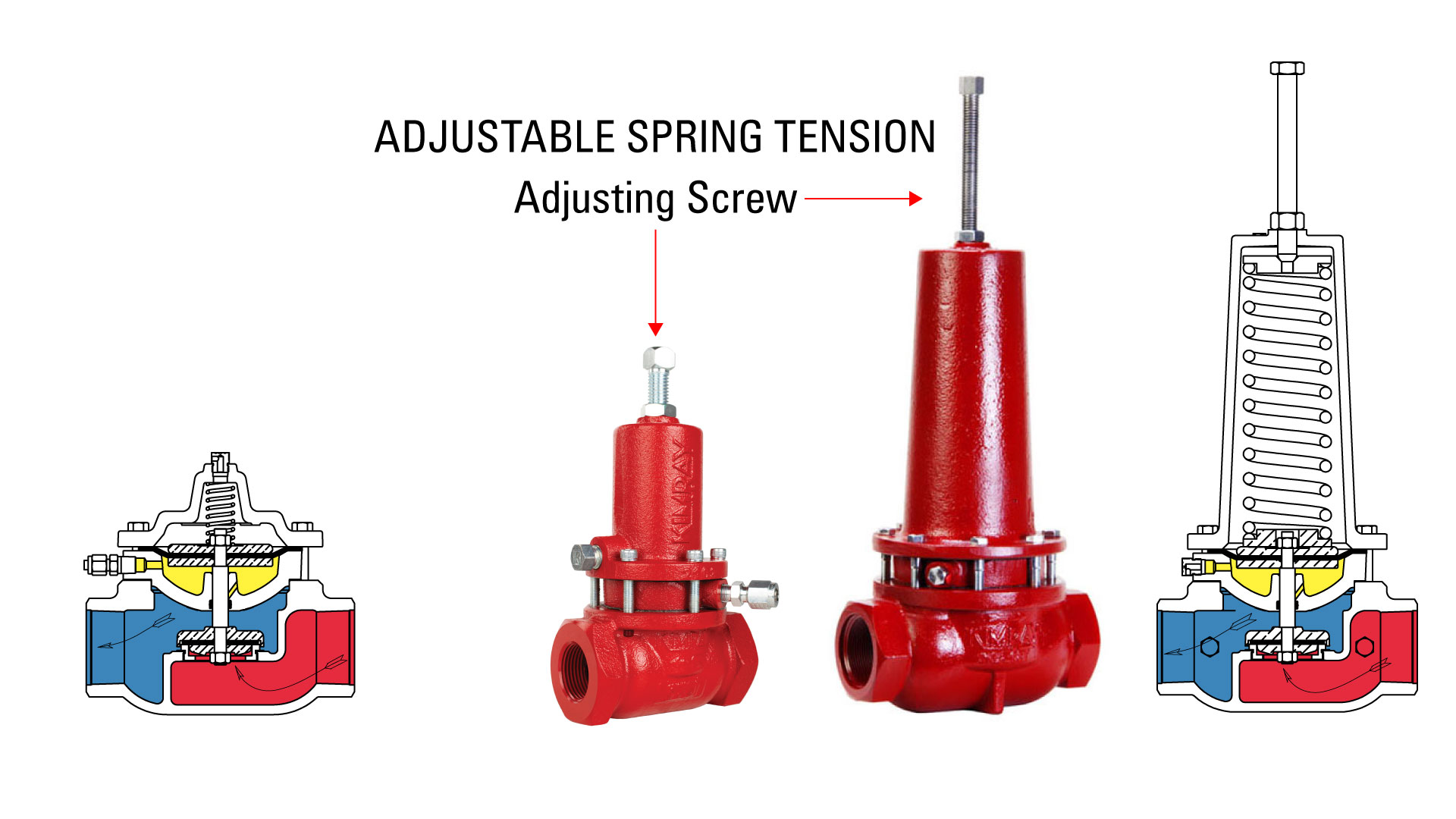
The reason you might need an adjustable double-acting valve is that you want the valve to have a failure position of closed, but you don't want to swap out springs. You want to change the spring tension or range without taking apart the valve.
This valve has an adjustment screw on top, so you can increase or decrease the spring tension, which will hold against different upstream pressures. It also allows you to turn this valve into a spring-loaded back pressure valve in some applications where you don't have to have a pneumatic signal going to the valve actuator. The spring on top acts against the upstream pressure pushing up on the seat.
If you need to repair the single-acting, double-acting, or adjustable double-acting valves, they are all similar valves. We have a repair video that covers all three.
Electric Low Pressure Control Valve (E-LO)
Next up, we're going to talk about the electric low pressure control valve (E-LO).
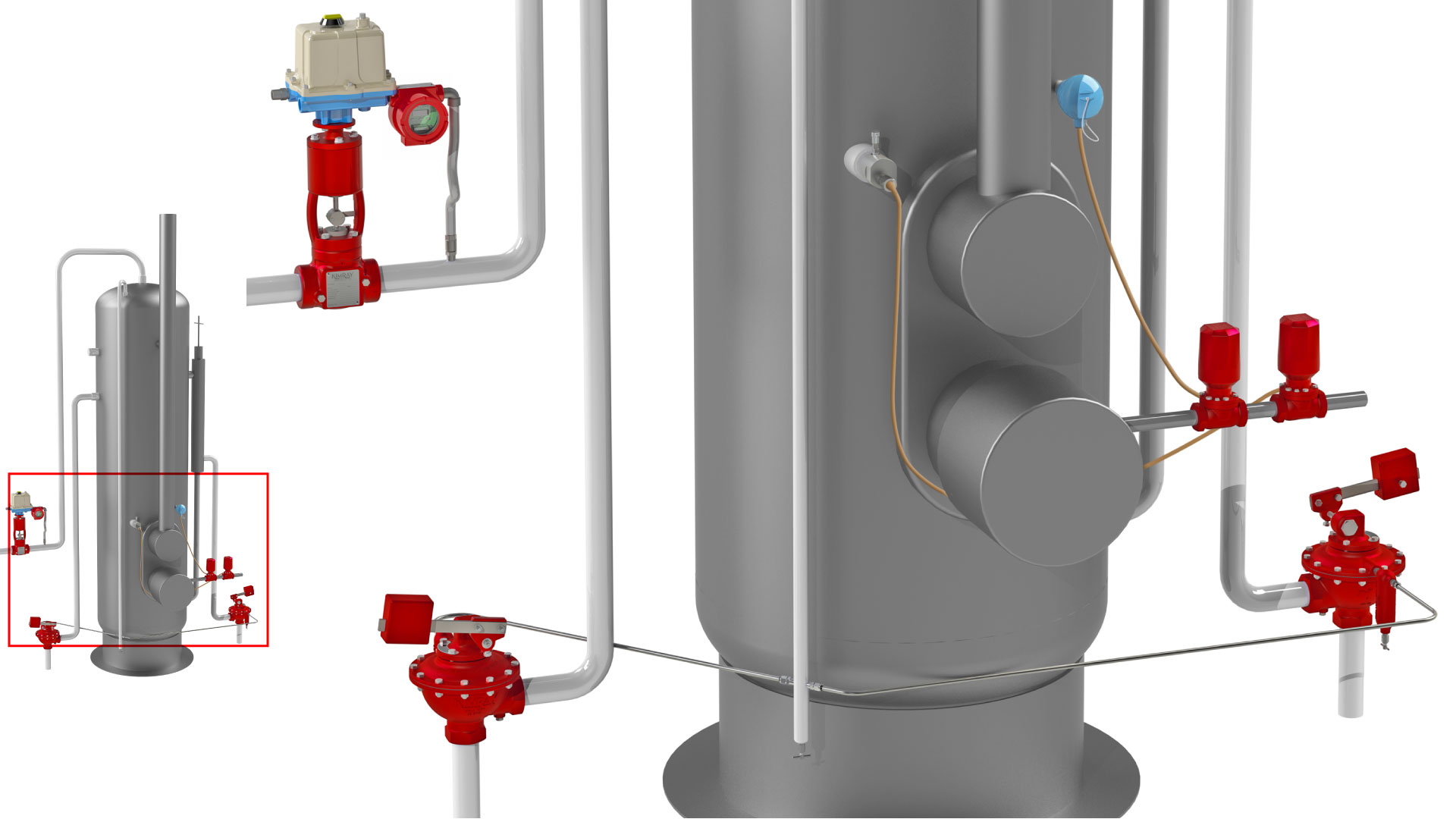
This is a 1-inch valve that can be used in either liquid or gas applications. Most commonly, it's used in BMS (burner management systems) to control the fuel going to a burner electronically. This allows you to automate your system if you're doing remote startups or shutdowns. You can also remotely monitor this valve. It has the same capabilities as its pneumatic counterparts but operates electrically.
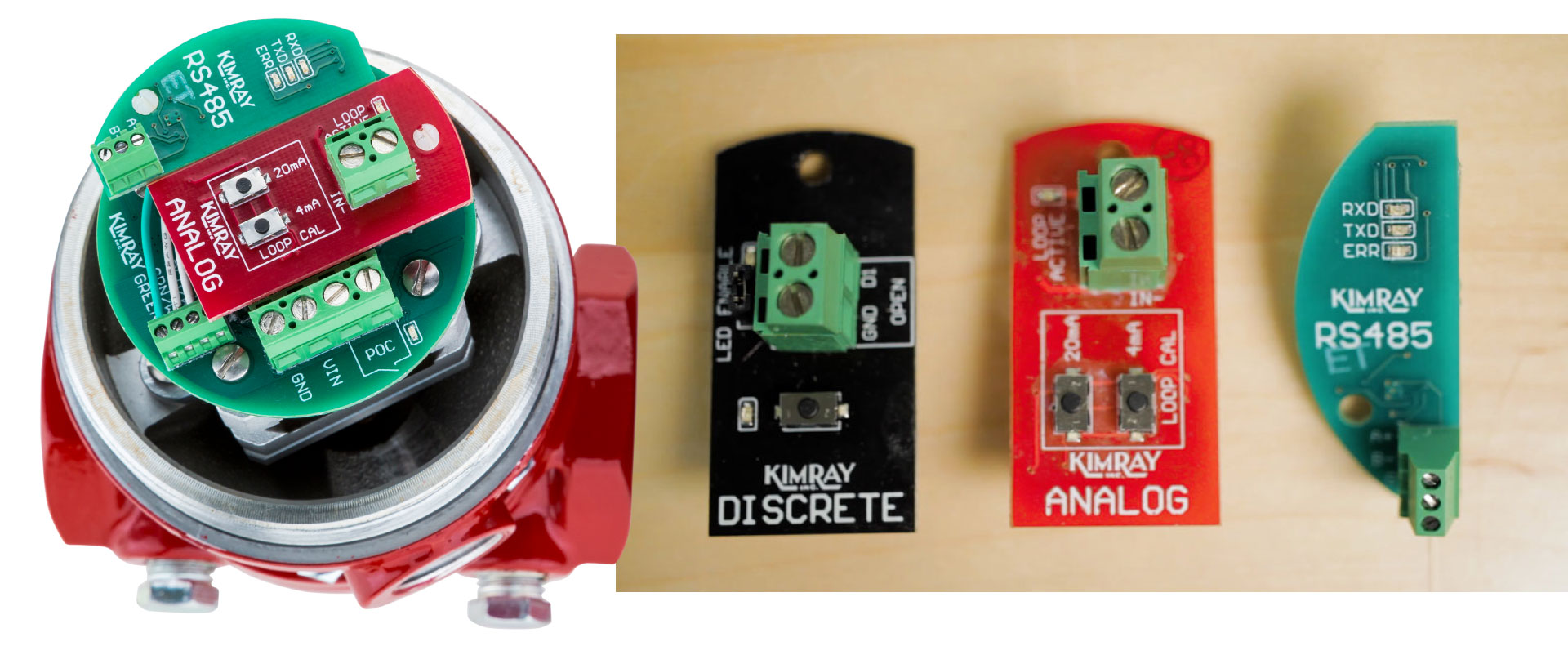
The ELO valve has a small electric actuator on top and uses a 4 to 20 milliamp signal or a discrete signal for on/off control. A 4-20 signal is modulating and analog, like a dimmer on a light switch where you can go between on and off.
Discrete signals are like a light switch where it's either on (valve opening) or off (valve closing).
There is also an optional Modbus card you can get for the ELO, but it is an extra piece you have to order.
Watch: How Does the E-LO Work?
Emissions Options
One of the big reasons people use the ELO valve instead of a pneumatic valve is for emissions and emissions reduction. This valve uses electricity to actuate, so there is no vented gas and no potential for vented gas. With the low pressure pneumatic control valves, the only options to make them emissions-free would be to use nitrogen or compressed air instead of gas.
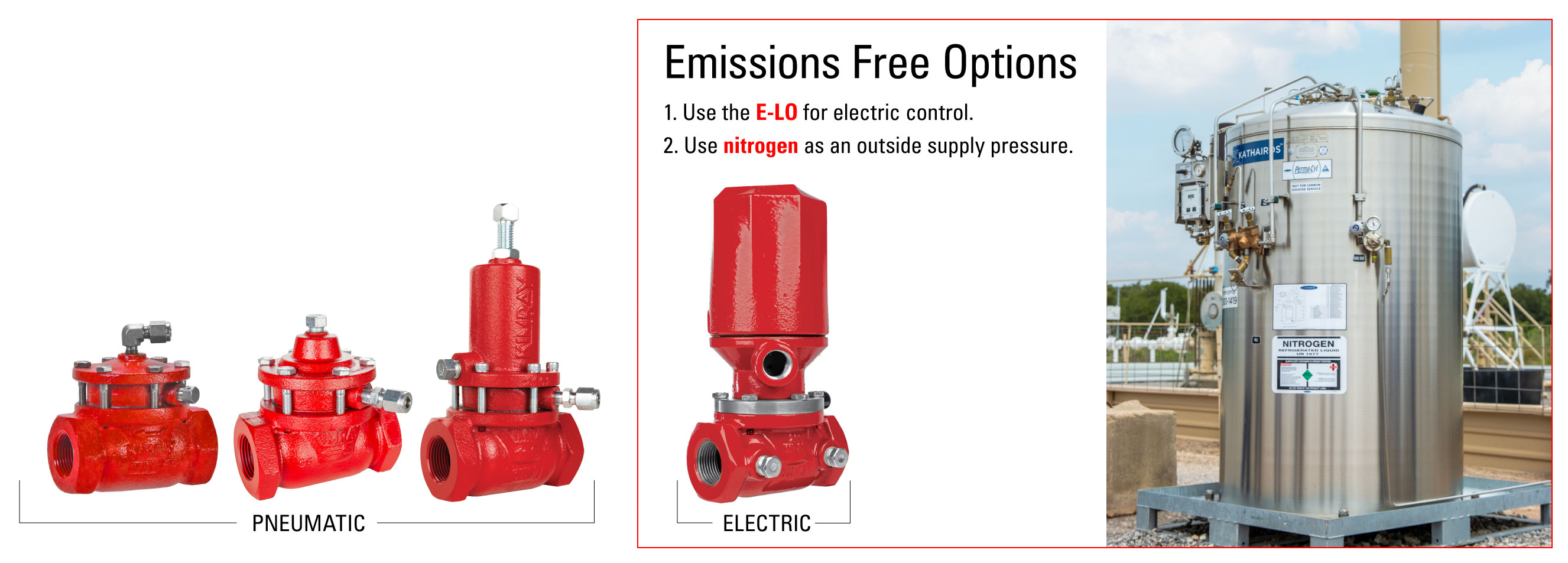
The products themselves do not vent, but the pneumatic signal is vented back through the pilot. If you supply that pilot with nitrogen, it sends the nitrogen to the valve, and the signal is vented back through the pilot. If it's nitrogen, you're emissions-free.
The reason we don't use compressed air with any of these low pressure pneumatic control valves is that there's only one point of failure between the oxygen in your compressed air and the flow stream. If the diaphragm or the O-ring fails, you have the potential to mix both oxygen and fuel, needing only heat or a spark to cause combustion.
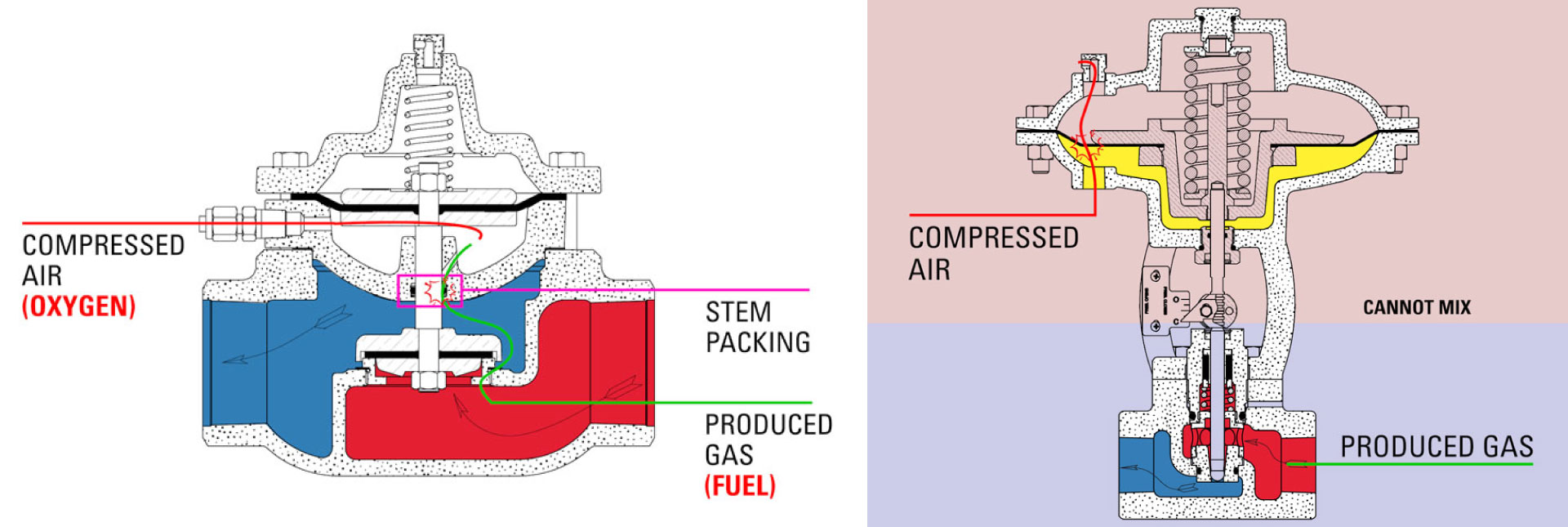
If you want to move towards compressed air to reduce emissions, you can in a burner valve application. We suggest going to a high-pressure control valve. You can still get small CVs or small flow rates that fit a wide application, but the valve actuator and the process flow are separated by an open yoke.
Even if the diaphragm where the compressed air is sent fails, the air is vented to the atmosphere and not introduced into the flow stream of the process. This way, you won't have oxygen and fuel mixing.
To learn more about which valves make sense for your operation, contact your local Kimray store or authorized distributor.