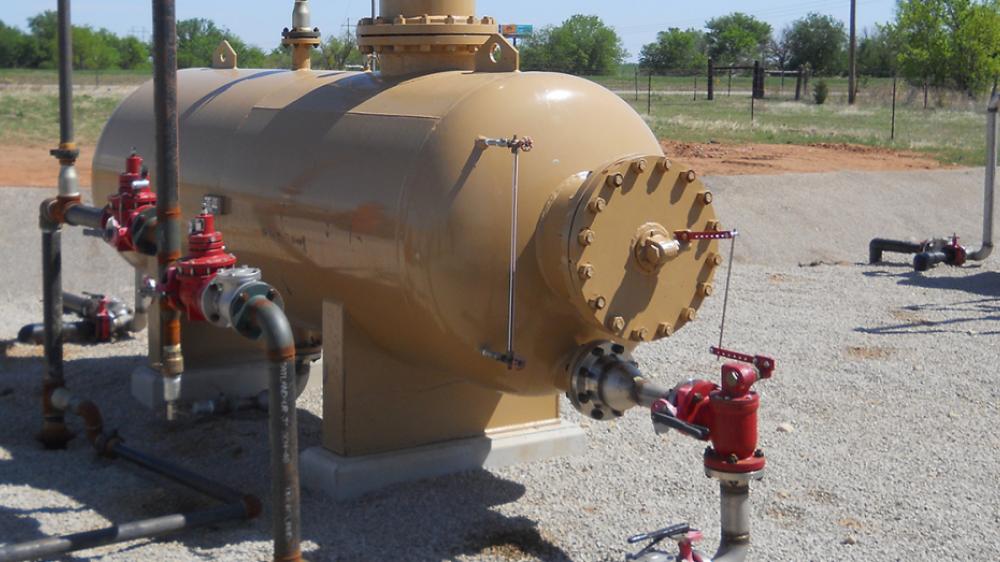
What are Fugitive Emissions?
As gas moves through valves to various production vessels, it is typically vented by pneumatic controllers. This venting, along with incidental emissions that occur during production and transportation, make up fugitive methane gas emissions.
Methane is the primary component of natural gas, making up around 80% of the gas produced from a well.
Due to a variety of pressures, fugitive emissions are regularly on the minds of oil and gas producers, and many larger producers are setting ESG Goals (Environmental, Social & Governance) and setting targets to reduce their natural gas emissions.
Regulations play a part as well, both at the federal and state level, in particular in more regulated areas like New Mexico and Colorado.
At Kimray, we are prepared to equip you for sustainable energy production long into the future, whatever your ESG goals.
That’s why we offer several options for zero-emission production to help you keep ahead of regulations. These options include:
- Lever-Operated Liquid Dump Valves
- Non-Venting Regulators
- Electric Actuators, Controllers and Pilots
Lever-Operated Liquid Dump Valves
Lever-Operated Liquid Dump Valves work in conjunction with a trunnion and linkage rod to provide emissions-free liquid level control in separation vessels.
This simple design is reliable, easy to set up, and will stand up to harsh environments.
Non-venting Pneumatic Regulators*
Kimray pneumatic high pressure control valves and low pressure regulators can be used in common applications including back pressure regulation and pressure reducing regulation.
While our standard regulators and pneumatic control valves currently come tubed to vent, we also offer many non-venting versions.
These non-venting valves use process natural gas to supply the diaphragm and actuate the valve. Then, rather than venting the gas to atmosphere, they send the gas back into the production line.
*Note: If you already have standard regulators, you can convert them from vent to non-vent by changing the tubing. Watch our step-by-step video below.
Pneumatics with Compressed Air
Another way to avoid fugitive methane gas emissions is by using compressed air rather than supply gas to power your valves and control instruments.
With compressed air, you can continue to use pneumatic controls without emitting fugitive gasses.
Electric controllers
1. Electric Level Switch
For high or low level shut down in your separator, you can use an electric level switch.
An electric level switch controls a small span of liquid of about 2”. This switch operates just like our pneumatic switch, except the output signal is electric rather than pneumatic.
This signal is a discrete output, which is used for on/off control. An analog signal, which we’ll discuss a little later, is used to provide modulating control.
The electric level switch covers a range of 0W to 25W of power, pairing nicely with the demands of today’s automation equipment.
Here’s how it works:
As the liquid level increases, the float is lifted, and the magnet located in the float lever moves downward and closer to the reed switch. The reed switch is in the enclosure of the body and is isolated from the process conditions. When the magnet gets close enough to the reed switch it will close it. When liquid level decreases, the magnet will move away from the reed switch causing it to open.
This level switch can be used to shut down incoming production if the liquid level is higher or lower than the float output signal position. To prevent liquid carryover the level switch is used by many producers for a high level shutdown. If a dump valve or liquid level controller fails, the rising liquid will trip the high level switch that’s positioned near the top of the vessel, shutting the inlet flow to the vessel and/or signaling an alarm.
2. Electric Actuator /Valvcon Electric Valve Actuator
An Electric Actuator replaces the pneumatic actuator on control valves. It provides accurate, zero-emission control and can tie into a Programmable Logic Controller or Remote Terminal Unit for remote control/monitoring.
The actuator features an on-board OLED screen, providing operators with push-button set up and calibration. And with its real-time two-way communication capabilities, the actuator allows producers to minimize travel time, increase ability to pump by exception, and greatly improve their process monitoring.
Paired with a Kimray valve body, the Electric Actuator can be used anywhere your control valves are, including in liquid dump, gas regulation, and artificial lift applications.
The Electric Actuator has 3 key advantages over pneumatic actuators:
- Low Maintenance Operation—Because it doesn't rely on process gas, which can potentially cause corrosion, this long-lasting valve actuator can operate maintenance free for an extended period.
Zero Emissions—Because these actuators use electric power, they require no gas supply and do not vent any gas to the atmosphere.
Remote Communication—These actuators can tie directly into your SCADA system to provide remote monitoring and communication.
3. Electric Pilot
Currently, if you want to electrically control and remotely monitor your production processes, you need to use an RTU or PLC. These devices allow you to connect electric actuators to their microprocessor-controlled system via SCADA or another communications control network.
However, for sites or applications where only one or two valves need monitoring, the Kimray Electric Pilot is an ideal, cost-effective solution.
The Electric Pilot is a stand-alone electric controller that can control pressure, flow, temperature, or level. It can also be used in gap control and timer applications. It features an interactive screen and allows you to control process conditions without the use of computing hardware.
Here’s how it works:
The internal pilot receives a raw 4-20mA signal from a sensor, which represents a process condition. This signal could be from a pressure transducer or resistance temperature detector (RTD). That signal is then conditioned and sent to an electrically controlled valve via a proportional 4-20mA output signal.
The pilot shares a common input power source with the electric actuator and does not need a dedicated power source.
___
To speak with an expert about how our zero-emissions solutions can help your operation, contact your local Kimray store or authorized distributor.