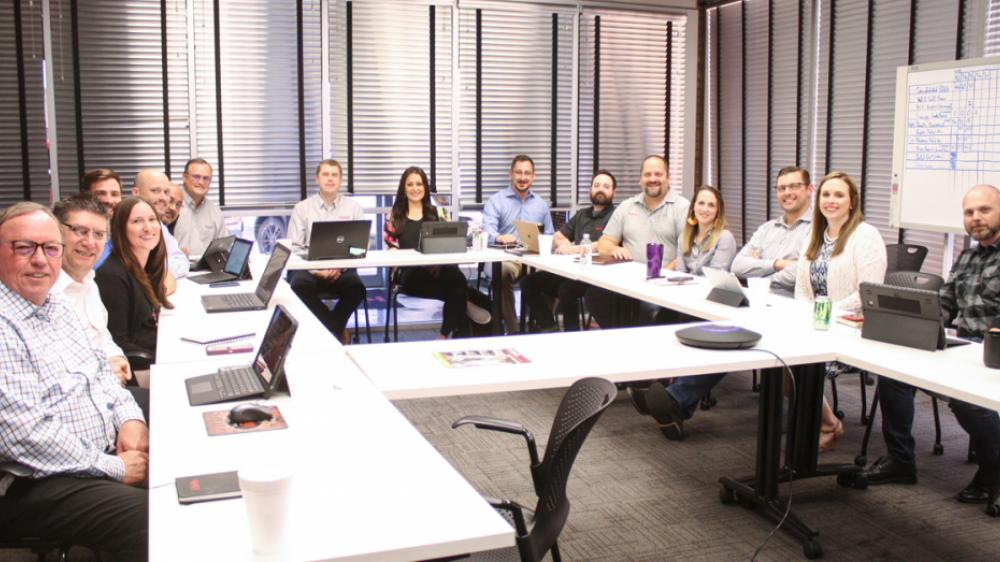
Lead Time
Since the rapid bounce back of the oil and gas industry in 2017, “Lead Time” has been a central concern for Kimray and our customers. We know how crucial it is to have product available when you are ready to produce a well.
In order to get our valves and control equipment produced as efficiently as possible, our team has identified and prioritized two key opportunities for lead time improvement: processes and infrastructure.
Processes: SIOP
The Kimray SIOP group (Sales, Inventory, Operations, Planning) is a cross-departmental team hard at work fulfilling Kimray’s Extreme Customer Service promise.
Customer satisfaction requires careful management of supply and demand. Kimray is focusing on both producing timely products and lowering overall costs by stocking the right inventory.
The SIOP leadership team consists of Zack Tallon (Director of Customer Experience), Erin Shipp (Director of Supply Chain), and Josh Grantham (Director of Manufacturing). The process has a 4-meeting cycle each month. In these meetings the the team does the following:
- Gauges the real-time market demand for our products
- Runs simulations from demand to get visibility on any material or capacity constraints
- Makes appropriate adjustments based on simulations and finalizes the production plan
This process has helped us get better visibility on what our customers need. In addition, it eliminates the time and resources spent on products that they don’t.
Infrastructure: Distribution Center
The current Kimray campus has grown organically over six decades and includes several buildings just north of downtown Oklahoma City. As such, it presents some unique physical constraints and efficiency challenges.
One primary example is that up until now our inventory and shipping departments have shared space with our manufacturing department.
That will soon change.
In the spring of 2019, Kimray will be officially unveiling our brand new Distribution Center on the Oklahoma City campus!
This dedicated building will provide more efficiency, flexibility and space to have our high-volume items crated and ready to ship.
- Efficiency: The layout of the new center will allow fork lift drivers to more quickly get from aisle to aisle, making the flow of outbound orders more efficient.
- Flexibility: It will feature two additional wrap machines and one additional jib crane, which will prevent bottle-necking during times of peak demand.
- High-Volume Items: At 25,000 square feet, this new center will have the space and ability to stock Kimray’s most popular products.
You Spoke. We Listened.
In May of 2018 nearly 10% of our orders were behind schedule. In March 2019, with the efforts of our SIOP team and growth in inventory, that number was down to .2%.
We hope you’ll join us as we celebrate this improvement while renewing our efforts to serve you better moving forward.
Thank you for providing us with the honest feedback and forecasts that made this progress possible.
Onward!