One of the ways energy producers are reducing their emissions footprint is by converting their gas regulators to non-vent.
In this video, we show you an animation of what’s actually going on inside both the non-venting back pressure and non-venting pressure reducing regulators.
Non-Vent Back Pressure Regulators
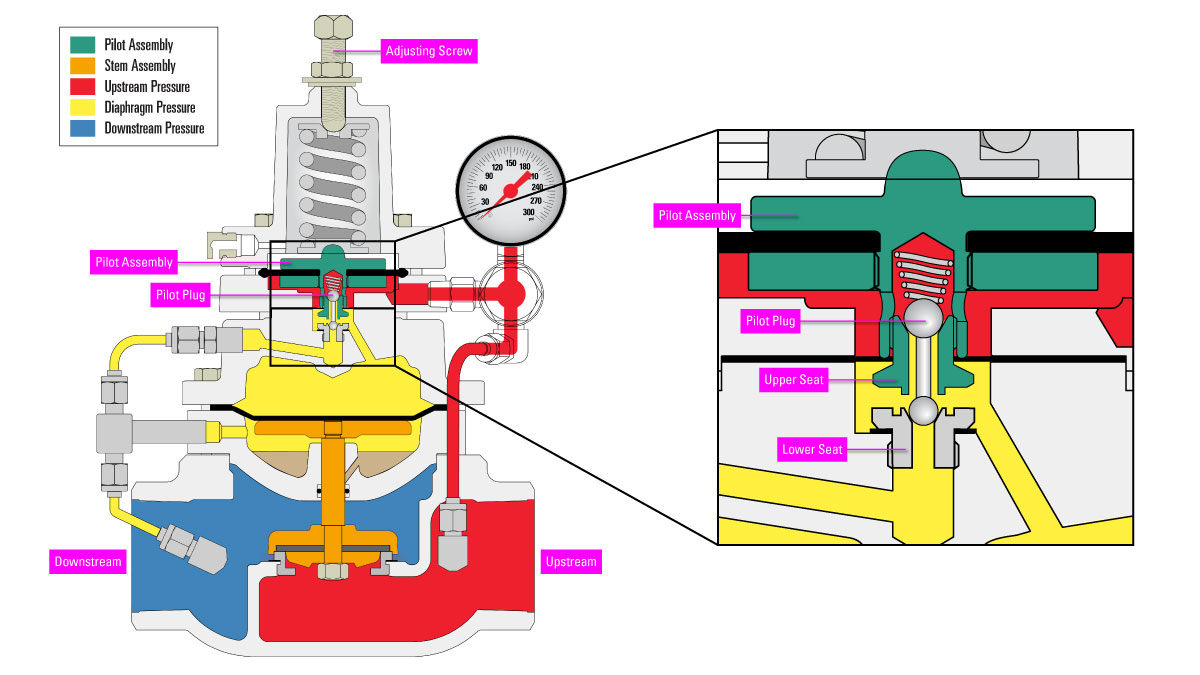
Upstream pressure flows into the valve inlet and travels through the valve body, exiting through the downstream side.
With the adjusting screw unthreaded, there is no tension on the pilot assembly to move the valve to a closed position.
Upstream pressure also travels through the tubing, flowing into a filter housing where debris and trash are caught to prevent malfunction before entering the pilot and underneath the sensing diaphragm.
.gif)
The pilot plug upper seat is closed, blocking upstream pressure.
The pilot plug lower seat, which is the pressure vent, is open, allowing the valve seat to be in the open position.
When the adjusting screw is tightened and the spring tension is greater than the upstream pressure, it forces the pilot assembly to move down.
.gif)
This positions the pilot plug to open the upper seat and allows full upstream pressure to now push down on the motor valve diaphragm.
The pilot plug movement adjusts the amount of pressure on the diaphragm, repositioning the stem and seat assembly.
The flow through this regulator is from underneath the valve seat.
The upstream flow pushes up on the valve seat as the gas is pushing down on the motor valve diaphragm. Because the motor valve diaphragm area is twice that of the seat, the regulator can be held in a closed position with equal pressure on both surfaces.
.jpg)
If upstream pressure exceeds the spring tension, which is your set point, it pushes against the pilot assembly, closing off the supply side of the pilot plug and unseating the lower seat, which is the pressure vent.
.gif)
Gas holding the valve closed then vents from the top of the motor valve diaphragm to the lower housing and downstream side of the valve, allowing the valve to open and the upstream pressure regulated.
.gif)
The regulator will begin controlling upstream pressure as it increases or decreases, maintaining a constant back pressure set point.
With the upstream pressure neither above nor below the set point, the pilot assembly assumes a position in which both seats of the pilot plug are closed.
Non-Vent Pressure Reducing Regulators
The Kimray Non-Vent Pressure Reducing Regulator monitors and controls downstream pressure.
With the adjusting screw unthreaded, there is no tension on the pilot assembly to move the valve to an open position.
Upstream pressure flows into the inlet and is blocked by the closed seat in the valve body.
Upstream pressure also travels through the tubing into a filter housing where debris and trash are caught to prevent malfunction.
The flow continues underneath the pilot plug and fills the cavity of the motor valve diaphragm. This pushes down on the diaphragm, diaphragm plate, stem, and seat, keeping the valve in the closed position.
Because the motor valve diaphragm area is twice that of the seat, the regulator can be held in a closed position with equal pressure on both surfaces.
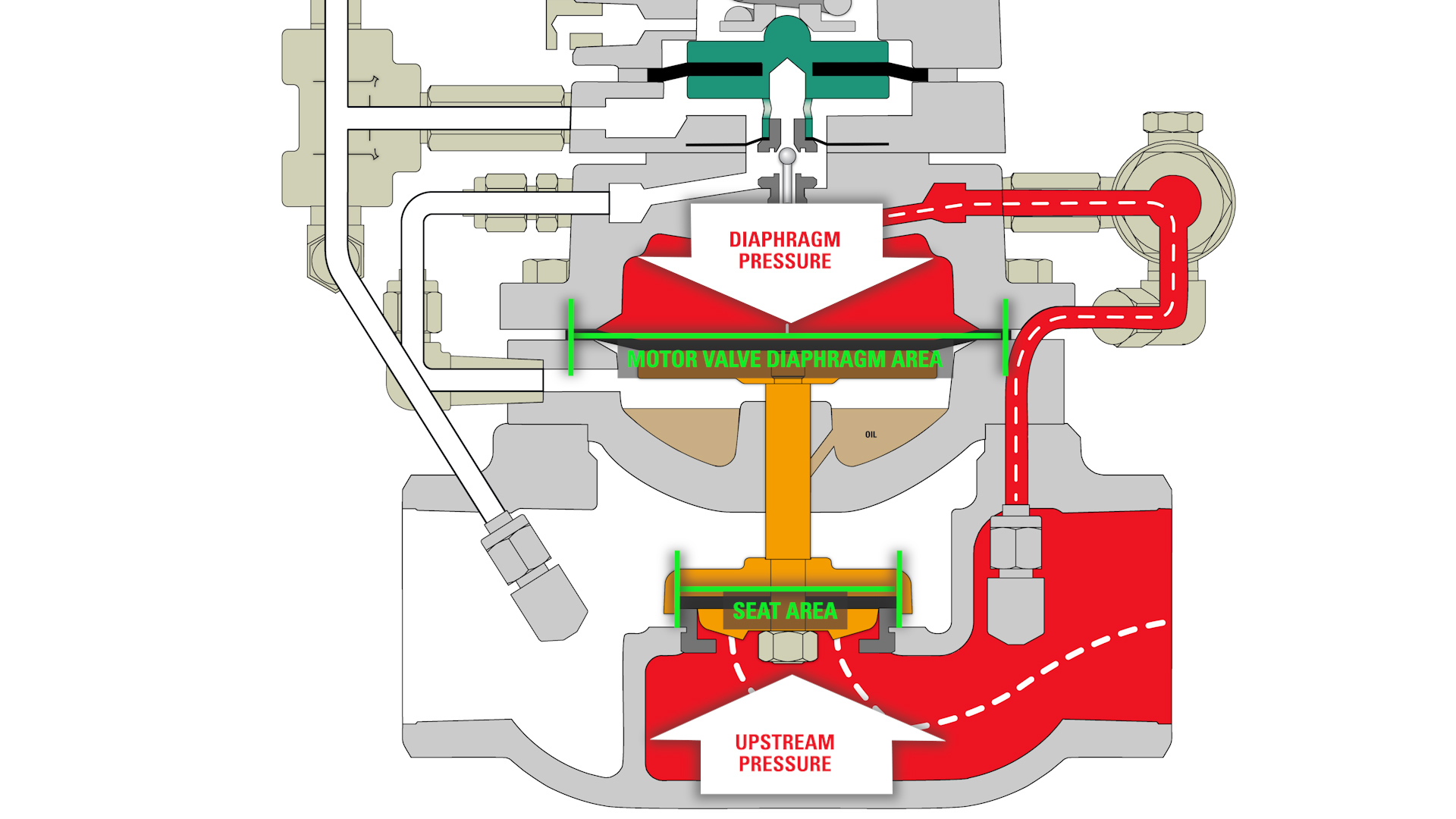
The pilot plug lower seat is closed, blocking upstream pressure.
The pilot plug upper seat, which is the pressure vent, is open, allowing diaphragm pressure to vent from underneath the motor valve diaphragm and the valve seat to be in the closed position.
When the adjusting screw is tightened and the pilot spring tension is greater than the downstream pressure, it forces the pilot assembly to move down.
.gif)
This positions the pilot plug to open the lower seat and allows full upstream pressure to now flow into the cavity of the motor valve diaphragm.
Now the pressures are equalized on both sides of the diaphragm and the upstream pressure can push open the valve seat.
The pilot plug movement adjusts the amount of pressure in this cavity, repositioning the stem and seat assembly to control the downstream setpoint.
If downstream pressure exceeds the spring tension, which is your set point, it pushes against the pilot assembly, closing off the lower seat and unseating the upper seat, which is the pressure vent.
Gas holding the valve open is vented from underneath the motor valve diaphragm to the downstream side of the valve, allowing the valve to close and the downstream pressure to be regulated.
.gif)
With the downstream pressure neither above nor below the set point, the pilot assembly assumes a position in which both seats of the pilot plug are closed.
The regulator will maintain and control a constant downstream pressure set point.