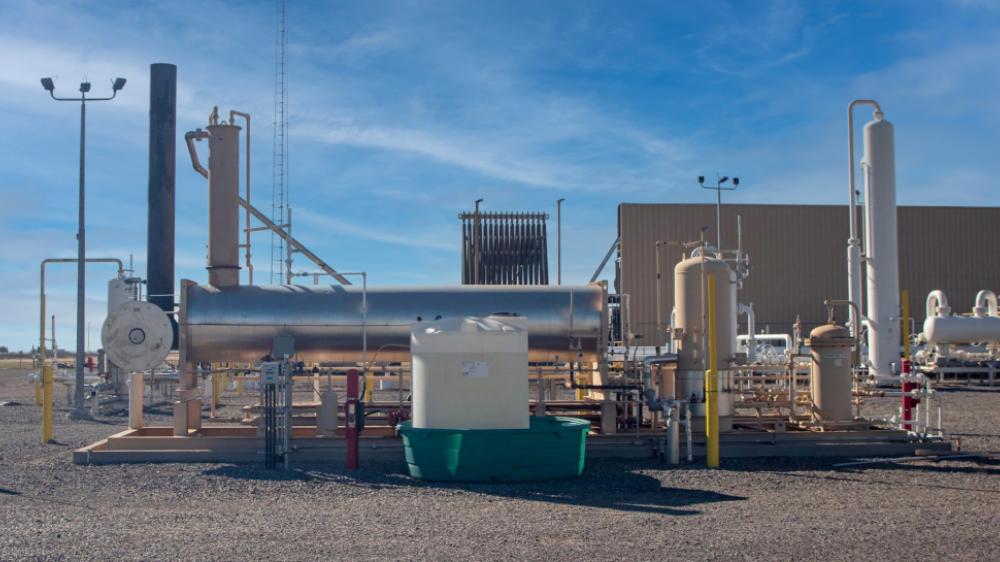
In this blog, we are going to answer a wide array of questions we have received from gas producers about operating a natural gas dehydration system.
1. What is dehydration in gas production?
Dehydration is the process of removing water from a gas stream.
2. Why is dehydration needed?
Dehydration will prevent gas freeze-ups, gas transmission problems and pipeline corrosion. It is also required to meet sales contracts.
Installation, Startup & Shutdown
3. What precaution should be taken in erecting a new glycol unit?
The absorber must be vertical to ensure the proper flow of glycol in the vessel and adequate contact of gas and glycol.
New, reconditioned and used equipment may at times not have proper sealing at the trays and bubble caps. These should be inspected if very high glycol losses exist. Inspection ports at the trays can be very useful when inspecting or cleaning the vessel.
4. When I start my glycol unit, the glycol will not return to the base of the absorber. Why not?
During a plant startup, the pressure on the absorber should be brought up to operating range and then the glycol should be circulated to establish a liquid level on all the trays. The reboiler temperature should also be brought up to the operating range. Then the gas rate should slowly be increased to the desired gas flow rate.
If the gas enters the absorber before the trays are sealed with liquid, it will pass up through the downcomers. When this condition exists and glycol is pumped into the absorber, the liquid has difficulty flowing down through the downcomers. The glycol will then be carried out with the gas stream rather than flow to the bottom of the absorber.
5. How slowly should a glycol unit be shut down?
To take a glycol unit out of service, first close the gas outlet from contactor. Then the fuel to the reboiler should be shut off. The pump should run until the reboiler temperature is lowered to approximately 200°F. This will prevent glycol decomposition caused by overheating.
When the reboiler temperature is at 200F or below then the plant should be depressurized slowly to prevent a loss of glycol.
You will need to close the upstream feed valve to isolate the tower before depressurizing the tower. If you do not isolate the tower then upstream feed gas will continue to flow while trying to blow down the tower.
Also, there should be a valve on the downstream side of the tower, though there is not always. The meter run does have a check valve to prevent backflow from the pipeline, but if the meter is some distance away then you have to blow the sales line down, which could be a large amount of gas.
How to Minimize Rising Costs in Gas Dehydration
6. Our operating expenses are rapidly rising. What can we do to improve the situation?
The field supervisor and operators need both on-the-job and classroom training to help them fully understand the process principles and equipment. The training materials must be thorough and understandable.
7. Our gas-glycol pump maintenance costs have been very high. What can we do?
Keep the lean glycol moving through the pumps below 180° to 200°F range and improve the glycol filtration process.
One company found it helpful to add a high pressure filter on the rich glycol side between the absorber and the pump. This filter cost is very low. They also use Teflon darts and slides in the pumps. These changes cut the pump maintenance costs by 98%.
8. The cost of glycol for our dehydrators has tripled over the past few years. We also faced a serious glycol shortage several years ago. Our company is making a concerted effort to improve our glycol plant operations. What can we do to conserve glycol consumption in our plants?
Many people do not realize that the feedstock for manufacturing glycol is supplied by the glycol consumers.
Normally, ethane and propane, extracted in a gasoline plant, are used as the feedstocks for manufacturing glycols. We all know how the prices for hydrocarbons have sharply increased, so it is easy to see why glycol prices are rising.
Since the petrochemical industry is not on the top priority list for hydrocarbon feedstocks, you are very wise to seek ways to conserve glycol consumption. As a general rule, a glycol dehydration system (contact type) can lose about 1 lb of glycol or 0.1 gallons of glycol per mmscf of gas.
Here are some causes of excessive glycol consumption.
I. Excess glycol carryover from absorber.
A damaged demist pad in the top of the absorber and high gas velocities can sharply increase glycol losses. The demister is usually designed for a maximum pressure drop of 15 to 35 lbs, depending on the basic design. Higher pressure drops will start tearing up the demister, allowing more entrained glycol to leave the top of the absorber with the sales gas. Here are 3 ways a higher pressure drop can be achieved.
Flowing more gas through the absorber than it is designed to handle will give a higher vapor velocity and a higher pressure drop. One company is currently flowing 120 mmscfd of gas through a glycol unit designed for 60 mmscfd.
As long as the same volume of gas is fed to an absorber, the gas velocity will increase as the absorber pressure is lowered below the design pressure. This will increase the pressure drop and the glycol losses.
As the contact trays in the absorber get coated with gummy deposits, some of the bubble caps or valve trays will get plugged. This plugging problem forces the gas velocity through the absorber to increase as long as the same volume of gas is fed to the absorber. This will increase the pressure drop and also the glycol losses.
A demist pad plugged with paraffin and heavy oils can also increase glycol losses.
A demist pad, with the wrong thickness, composition or location in the absorber, can also increase glycol losses. One company, after suffering for years with glycol losses of several gallons per mmscf, redesigned and relocated the demist pad in the absorber and cut the glycol consumption back to a reasonable level.
Line separators on the sales gas leaving the absorber can sometimes be effectively used. One company installed a line separator and the recovered glycol paid for the separator cost in less than 45 days.
Glycol foaming problems in the absorber will increase glycol losses.
The glycol circulation rate should be optimized to minimize glycol losses leaving with the sales gas. Three gallons of glycol for every pound of water to be removed should be circulated. Excessively high circulation rates will increase glycol losses.
II. Excess Glycol carryover from still column.
The ceramic saddles in the distillation column powdered and plugged like a chunk of concrete. The rich glycol could no longer penetrate through the plugged still tower packing, so it was flowing out of the still column vent piping rather than to the reboiler. Glycol is saved by replacing tower packing. It is imperative that the right type and size of tower packing be used for the replacement. The tower packing should be carefully loaded to prevent breakage.
Liquid hydrocarbons that get into the reboiler will usually flash out through the still column carrying large quantities of glycol with them.
Gas Conditions
9. I have some oxygen and H2S in my gas stream. Can this cause any special problems?
Yes, the oxygen will oxidize the glycol and form corrosive acids. The H2S will lower the glycol pH and turn the glycol black. Sometimes, the metal in the absorber will act as a catalyst and convert the H2S and oxygen into elemental sulfur, a very corrosive compound.
Flow Rates, Pressures, and Temperature
10. Why should the gas rates through the absorber be changed slowly from a low rate to a higher one?
Rapid surges of gas through the absorber may cause sufficient velocity increase through the trays to break the liquid seals, or it can lift the glycol off the trays, flood the mist extractors and increase glycol losses.
11. Are there any limitations to changing pressure on the absorber?
Yes. At constant temperature, the water content of the inlet gas increases as the pressure is lowered. At constant gas volumes, the gas velocity through the absorber increases as the pressure is lowered. This could increase glycol losses and create dehydration problems if the gas velocity gets too high.
12. How can I tell how much glycol is being circulated?
Most units do not have liquid flow recorders. For Kimray pumps, the glycol rate can be determined by counting the number of strokes per minute and then using the pump chart supplied by the manufacturer. It is necessary to know the model of the pump in service to use the chart.
For electric pumps, the rate can be calculated by shutting off the manual valve on the absorber glycol discharge line and measuring the height of the buildup per unit time. This height multiplied by the inside cross-sectional area of the absorber will give the volume of glycol pumped after converting the volume of the absorber to gallons. Or a flow meter could be installed.
13. What happens if my glycol circulation rate is too high?
The glycol can overload the reboiler and prevent good glycol regeneration. It can also prevent inadequate glycol-gas contact in the absorber and increase pump maintenance problems.
The end result may be poor dehydration, high glycol losses, and excessive fuel consumption in reboiler.
14. Do I need to monitor the pressure in the reboiler?
This would be a good safety feature and could save glycol. Normally, the reboiler is operated at atmospheric pressure. When the pressure starts building up, glycol losses may increase sharply.
15. What should be the maximum reboiler temperature to avoid glycol decomposition?
For triethylene glycol, less than 404°F.
16. What should the lean glycol temperature be?
It should be held 10°F hotter than the incoming gas to the absorber.
Glycol Condition
17. What happens when glycol is thermally decomposed?
Corrosive acids are formed.
18. Should I throw the glycol away when it gets black?
Discoloration of the glycol indicates contamination. With better gas cleaning, filtration and carbon filtration the glycol may clean up to an acceptable state.
If desired dew point is met then no change of the glycol is needed. If continued desired outlet dewpoint is not met then new glycol is recommended.
19. I threw away the glycol when it went black, but within 24 hours the new glycol was also black. What happened?
It is important the glycol unit be thoroughly cleaned to ensure the contaminates have been removed from the system. Sludge collects throughout the glycol system and the new glycol will quickly absorb the sludge if it is not removed by cleaning. Apparently the unit was not cleaned before the new glycol was added.
20. If I have iron corrosive products in the glycol, what should I do?
Monitor the glycol pH and try to determine if the corrosion is coming from the pipeline or from within the glycol system. Keep the glycol alkaline and remove the iron compounds. Use corrosion inhibitors in the wells and pipeline if needed.
21. Why is the lean glycol concentration important?
The degree of dehydration which can be attained with glycol primarily depends upon the amount of water removed in the reboiler. The leaner the glycol going to the absorber, the more efficient its dehydrating power will be.
For example, when the contact temperature in the absorber is 95°F, a lean glycol concentration of 99% will provide a sales gas dewpoint of -2°F, while a 95% concentration will yield a 43°F dewpoint, if equilibrium conditions are reached.
22. Can glycol decompose even though the reboiler is designed and operated properly?
Yes. Hot spots, caused by deposits on the firetube, can decompose your glycol.
23. What is the safe glycol pH? Maximum pH?
A safe pH for glycol is 7.3. The maximum glycol pH recommended is 8.5.
Glycol with a higher pH tends to saponify any hydrocarbons present to create foaming problems.
24. Should I add something to the glycol when the pH is very high?
Some people add glacial acetic acid or vinegar to lower the pH. This is usually not recommended because the side effects can be detrimental.
25. What can I add to raise the glycol pH?
Triethanolamine, borax, or NACAP are three popular neutralizers.
26. How much neutralizer should be used to raise the glycol pH?
Chemical titration can be used to determine the exact amount of neutralizer needed. When titration is not available, a dosage of 1/4 pound of triethanolamine per 100 gallons of glycol in the system can be used.
27. Are there any other precautions that should be taken when neutralizers are added?
Yes, the filter elements may need to be changed frequently as the neutralizer is being added.
28. Will analyzing my glycol help?
Yes. Glycol analyses help pinpoint high glycol losses, foaming, corrosion, and other problems. This analytical information can enable the operator to evaluate the plant performance and make operating changes to get maximum drying efficiency.
29. How can iron corrosion products be detected in the glycol?
By chemical analysis.
30. Many times you can detect it by looking for finely divided black particles in the glycol. How can the iron compounds be removed?
Good filtration.
31. What can be done to combat paraffin problems in a glycol unit?
Paraffin usually carries in the gas stream in the vapor phase. The paraffin will usually pass right through the inlet separator. Sometimes, a coalescer or demister, designed to remove small vapor droplets, can be placed between the inlet separator and the absorber to remove paraffin vapors before they contaminate the glycol.
If the paraffin gets into the glycol system, a three-phase liquid hydrocarbon separator can be placed on the rich glycol side to remove the paraffin before it enters the reboiler. This separator should be properly sized and should contain the right internals to quickly separate the paraffin.
Generally, the paraffin solidifies at about 150°F. Therefore, the filter should be placed downstream from the hydrocarbon separator. The paraffin would quickly plug the filter elements. The hydrocarbon separator should normally be located downstream from the glycol-glycol heat exchanger so the solution will be above the paraffin solidification point. Solid paraffin would plug the separator.
32. What happens if too much salt gets in the glycol system?
The salt will collect on the firetube in the reboiler to restrict heat transfer and cause corrosion problems. Salt could also cause a firetube failure.
33. Can salt be removed from the glycol?
Yes, using either a reclaimer or iron exchange resin system. Either salt removal method can be portable.
34. If these salt removal systems are not available, what should we do?
When the salt content reaches one weight percent in the glycol, it should usually be drained from the system and saved for reclamation or discarded, depending upon the quantity.
Equipment
35. Can the use of a flash tank be helpful?
Yes, a flash tank can be used on the rich glycol side to recover gaseous hydrocarbons before they flash in the still column. The flashing hydrocarbons can increase glycol losses and break the ceramic tower packing in the still column. The gaseous hydrocarbons can be recovered and used as fuel for the reboiler.
36. How big should the flash tank be for gas dehydration?
A three-phase separator with a retention time of 15-20 minutes is usually sufficient.
37. What is a rectifier?
A rectifier is used to refine or purify by distillation, especially by distilling again and again.
In a glycol unit, the rectifying is accomplished by special design of the still column. Many still columns are designed where the rich glycol is fed into the vessel above the tower packing layer.
In this case, the tower packing is used to allow thorough mixing of the rich glycol and the hot vapors coming from the reboiler. By fractional distillation, since the water boils at 212°F and the glycol in excess of 300°F, the water vapor is separated from the rich glycol.
The rectifier, used to minimize the amount of glycol losses leaving overhead with the water vapor, is added by having several feet of tower packing in the still column above the rich glycol feed point to help scrub back the glycol.
38. What should the condenser temperature in the top of the still be?
Depending on the amount of reflux required, the condenser temperature should normally be held to about 215°F.
39. Why is the condenser temperature in the top of the still column important?
Glycol losses with the water vapor leaving the top of the still column can sharply increase if the condenser temperature is too low or high.
If too low, the water vapor will recondense, wash back into the still column, flood the tower packing, overfill the reboiler, and build the reboiler pressure, and then the excess liquids (glycol and water) are blown out the top of the still.
If too high, the glycol vaporization losses with the water vapor will increase.
40. How is the condenser temperature in the top of the still controlled?
The most common method is to use a finned atmospheric condenser to cool the hot vapors and recover the entrained glycol. This type of condenser depends upon air circulation to cool the hot vapors.
Sometimes this condensation method does not offer enough control and flexibility. Increased glycol losses can occur on extremely hot days when insufficient cooling in the condenser causes poor condensation. High glycol losses can also occur on extremely cold, windy days when excessive condensation (water and glycol) overloads the reboiler. The excess liquids will blow out the top of the still column as the reboiler pressure increases.
Sometimes protective windshields and/or still column insulation is used to prevent excessive cooling. The shields and insulation may not be needed on hot, calm days.
Another condensation method is to use an internal reflux coil in the top of the still column. Cool, rich glycol is used to flow through the coil to cool the hot vapors. A manual valve in the piping is often furnished to bypass the reflux coil, but a 3-way bypass valve operated by a temperature controller is preferred.
In a cold weather operation, with extreme low ambient temperatures, this could produce too much reflux and the reboiler could become overloaded. In this case the reboiler may not be able to maintain the required temperature.
With these conditions, the ambient air may be providing part or all of the reflux required. Therefore, a portion or all of the rich glycol should bypass the reflux coil. This is accomplished by opening the manual valve until the reboiler can hold the temperature. This lowers the amount of reflux produced by the coil and reduces the load on the reboiler.
This adjustment can also hold the condenser temperature at the desired level. If properly adjusted, the reflux coil can provide uniform condensation throughout the year.
41. How can I tell if excess glycol is leaving the top of the still column?
If a vent line is tied into the top of the still column, some of the condensed water can be collected and analyzed to see how much glycol it contains.
42. Why does the lean glycol contain 8% or 9% water even though the reboiler temperature is held to about 390°F?
The reboiler temperature should be verified for accuracy, using a test thermometer. Many times the dial gauge thermometer, if not kept calibrated, will start giving faulty temperature readings. The true glycol temperature in the reboiler may vary as much as 150°F from the recorded temperature on the dial gauge.
If the 390°F reboiler temperature is accurate, then look for other sources of water entry in the lean glycol. For example, if the glycol-glycol heat exchanger is located in the accumulator, look for corrosion leaks. If there are holes in the heat exchanger coil, then the water rich glycol could leak back into the lean glycol, contaminating it with excess water. This problem could also occur in a shell and tube heat exchanger.
43. What should the reboiler temperature be?
The reboiler temperature and pressure control the concentration of the water in glycol. With a constant pressure, the glycol concentration increases with higher reboiler temperatures. The temperature range in the reboiler should be 350°F to 400°F for triethylene glycol.
44. What causes the glycol to be held up in the reboiler instead of flowing into the accumulator?
Here are several reasons:
- Foaming in the reboiler could occur.
- The downcomer between the reboiler and accumulator may be plugged. This could especially be true if the downcomer is a packed column to aid in gas stripping. This tower packing could get plugged.
- Hydrocarbons flashing out of the reboiler could cause disturbances. Too much stripping gas could cause disturbances. If sweet gas is used in the accumulator to prevent oxidation, the vent line could be improperly connected.
- Many time the accumulator is vented to the atmosphere, especially if sweet gas is used to prevent oxidation. The vent line may be plugged.
- The pump may have stopped circulating the glycol.
45. How can hot spots be detected?
By inspecting the firetube or by shutting off the burner on the reboiler at night and looking down the firebox. A bright, red glowing hot spot will be visible at spots on the tube where deposits have collected.
46. Do the hot spots cause any additional problems other than glycol decomposition?
Yes, heat transfer is restricted and rapid firetube burnouts are possible.
47. How big a deposit have you seen?
Cakes of salt more than one foot thick are common.
48. What else causes firetube failures?
The reboiler must be horizontal when erected. A non-horizontal position can cause a firetube burnout.
49. How can liquid hydrocarbons get into the glycol system?
The hydrocarbons can carry in with the incoming gas if the inlet separator is overloaded or damaged. Some glycol units have no inlet separator, and this condition is nearly always bad.
Another way hydrocarbons get into the glycol system is when lean glycol enters the absorber colder than the incoming gas. When the gas and colder glycol co-mingle in the absorber, the gas will be cooled and this can create hydrocarbon condensation.
50. As the salt content in the glycol system builds up, firetube failure becomes frequent. How can I keep oxygen out of the accumulator?
A small amount of sweet blanket gas can be passed through the accumulator to keep oxygen out.
51. If sweet gas is used to prevent oxidation in the accumulator, how should it be hooked up?
It is usually not necessary to hook up a separator vent on the accumulator. The blanket gas is normally piped to the regular vent connection on the top of the accumulator. It may be necessary to see that the blanket gas valve, piping, and flow control orifice are open to pass gas.
52. Where does sweet blanket gas come from?
It is commonly taken from the fuel gas line.
53. How much blanket gas is needed?
Only a very slight flow of gas is required to prevent oxygen from entering the accumulator and to prevent steam generated in the reboiler from contaminating the regenerated glycol.
Glycol Foaming & Loss
54. During the recent cold weather our glycol unit suddenly started losing lots of glycol. What happened?
Some glycol absorbers have an integral scrubber built into the base of the vessel. This scrubber is used to remove liquids from incoming gas stream.
In very cold weather, the free water in the dump line on the scrubber can freeze. The additional incoming water gets trapped in the scrubber. This water can also freeze.
The resulting ice sometimes pushes up into the absorber, damaging the chimney tray. This allows the rich glycol in the base of the absorber to leak through the inlet scrubber rather than return to the pump when the ice thaws.
55. What types of foam are there?
Mechanical and chemical.
56. What causes mechanical foaming problems?
Turbulence, like high gas velocities through the absorber.
57. What causes chemical foaming problems?
Contaminants like hydrocarbons, corrosion inhibitors, salt and solids.
58. Can foaming problems be easily detected?
Yes. One easy way is to monitor the pressure drop in the absorber. If the pressure drop suddenly increases across the absorber from 2 lbs up to 25 lbs, foaming may be the problem.
59. Can we tell whether the foaming problem is the mechanical or chemical type?
Yes. If the pressure drop across the absorber suddenly rises about 20 lbs and the glycol removed from the system does not foam, the foam problem is usually a mechanical type.
60. Can chemical foaming problems be detected by trying to shake the glycol foam in a bottle?
Yes.
61. What does glycol foaming cause?
Poor dehydration and high glycol losses.
62. Should I use a defoamer to fight foam?
Every other means to eliminate the foam should be tried before defoamers are used. Defoamers can be temporarily used until the source of foam is eliminated.
63. Can I use any type of defoamers?
No. Some defoamers are totally incompatible with glycol and should never be used.
64. What about silicone defoamers?
They are very expensive and tend to break down in the reboiler, thus becoming another foam promoter.
65. Is a glycol reclaimer helpful?
Yes, many companies have portable reclaimers to help purify the glycol in all the units. A surplus reboiler can even be used, if properly operated.
Absorber
66. How many trays should the absorber have?
Normally the absorber contains 4 to 10 trays, depending upon the dehydration requirements.
67. How can we control the lean glycol temperature?
Here are 5 ways:
- Be sure the surge tank accumulator is not insulated. This will allow the lean glycol to start cooling quickly.
- Keep the glycol-glycol and gas-glycol heat exchange surfaces clean so maximum heat transfer can be obtained.
- Keep the reboiler temperature set at the optimum level.
- The pump speed should be adjusted to the optimum level and checked regularly.
- Additional heat exchangers can be added if needed.
68. How do the glycol and gas mix in the absorber?
The mixing is achieved by using trays containing usually bubble caps or valves or by filling the vessel with a tower packing.
The glycol and gas also travel counter-currently through the vessel. The gas moves up through the vessel and the glycol moves downward through the vessel.
69. What precautions are needed in using a tower packing in the absorber?
The tower packing manufacturer should be consulted for design information. The proper gas and glycol flow rates should be established for good mixing.
The glycol should be brought into the absorber through a good liquid distributor to prevent channeling. A piece of pipe running through the center of the vessel, with a series of holes in the pipe, usually does not provide good mixing.
Sometimes a good spray nozzle to spray the glycol over the tower packing is very beneficial.
70. Does the absorber ever need to be insulated?
Insulation can help when light hydrocarbons collect on the vessel walls due to excessive condensation. This often occurs when dehydrating rich, warm gases in cold climates. These very light hydrocarbons can cause tray flooding or foaming in the absorber and excessive glycol losses from the absorber and reboiler.
71. What precautions are needed with the mist pad at the top of the absorber?
The type and thickness of the mist pad should be carefully studied to minimize glycol losses. It should be located with adequate spacing above the top tray to avoid flooding and high glycol losses. It should be kept clean to avoid paraffin plugging and other damage.
Gas Stripping
72. What is gas stripping?
Maximum heat in the reboiler can reconcentrate the lean glycol back to about 99.6%.
Very high glycol concentrations up to about 99% can be achieved by removing the additional water with stripping gas. There are several methods of introducing stripping gas (dry fuel gas) into the system.
One method is to use a vertical tray or packed system (using tower packing) in the downcomer between the reboiler and accumulator. Dry fuel gas enters the accumulator and moves up into the downcomer where it mixes with the glycol leaving the reboiler. The dry fuel gas will remove the additional water. The glycol flows into the accumulator and the water-laden stripping gas passes out through the still column. This method is used with an over/under design style glycol regeneration unit.
Another method is to use glycol stripping gas spargers in the reboiler beneath the firetube. As the glycol flows through the reboiler, gas is injected into this vessel and is heated by the glycol. The stripping gas mixes with the glycol, removes some of the water and passes out the still column. The lean glycol flows from the reboiler into the accumulator.
73. How much stripping gas should be used?
The stripping gas rate will vary according to the lean glycol concentration desired and the method of glycol-gas contact. The amount of stripping gas required will usually be about 2 to 10 scf per gallon of glycol circulated.
Normally the glycol unit manufacturer provides a stripping gas chart in the instructional manual when stripping gas is used.
74. Can too much stripping gas be used?
Yes! The stripping gas rate can get high enough to flood the still column and blow glycol out the top.
As the overall process conditions change, it is important to see that stripping gas is still needed. If stripping gas is no longer needed, several thousand dollars per year may be saved. The stripping gas is normally not recovered.
Glycol Filtration & System Cleaning
75. I used water and high detergent soaps to clean my system and really got into trouble. Why?
Water and soap have little cleaning action on the types of deposits found in the glycol system. Even small quantities of soap left in the system will make the new glycol foam.
76. I steam cleaned an absorber and could not get it to take any gas after the cleaning procedure. Why?
Steam many times only bakes on the impurities that were already on the trays. This plugs the bubble caps or valves so they can no longer take gas. Steam cleaning is not very desirable.
77. I acidized a large glycol unit and eventually spent $250,000. This unit still did not work right. What happened?
Acid cleaning is good for removing inorganic deposits. However, since most deposits in the glycol are organic, acid cleaning is not very effective. Many times, the acid reacts with the organic deposits to form abrasive, gooey compounds, or spongy compounds that plug the system everywhere.
78. Can I use the glycol pump to move cleaning chemicals through the system?
It is not desirable. Some cleaning chemicals damage the pump. Most glycol pumps do not have an adequate circulation rate to help much anyway.
79. What type of cleaning chemicals are preferred?
Heavy-duty alkaline chemicals.
80. Does heating the cleaning chemicals help?
Yes. A temperature in the range of 140°F can be beneficial.
81. What type of filter should be used?
Normally, a good element made from cloth fabrics is best. Paper and fiberglass elements are not recommended.
82. What is the recommended filtration level?
The solids content in the glycol should be held below 0.01 weight % or 100 ppm.
83. What happens to the glycol system if poor filtration is maintained?
High solids will increase pump wear, plug the contact trays, plug the tower packing, and collect on the firetube in the reboiler.
84. Should the filter treat the full circulatory stream or be used as a side stream filter?
It is a matter of economics. Full stream or side stream filters can work well, if designed and operated properly.
85. How frequently should the filter elements be changed?
This depends entirely on how dirty the circulating glycol is. If the incoming gas and the circulating glycol are kept clean, the filter elements will last a long time.
86. How can we tell when the filter elements need to be changed?
By using a pressure differential across the filter and changing the elements when the pressure reaches 15 lbs.
87. What is carbon purification?
It is the use of activated carbon to remove glycol impurities.
88. What are the types of carbon purifiers?
One type uses a vessel filled with activated carbon. Another type uses carbon in a metal canister. This method works similar to a solid filter.
89. What is the best type of carbon?
Coal-based carbons are hard and dense. They are the most widely used. Wood-based carbons are soft and light. They usually create excessive dusting problems.
90. Should the carbon purifier be used as a full stream or side stream treater?
This is governed by economics. Either method works well.
91. What are some of the problems with carbon purifiers?
A well-designed purifier can solve a great number of problems. A poorly built purifier can create many problems. The carbon-packed vessel should have a liquid distributor to avoid channeling. It should have provisions for back flushing with water to remove loose dust.
The right type of screens are needed in the bottom to prevent plugging or carbon loss. If carbon gets out of the vessel and into the glycol circulating system, it can become a foam promoter. The liquid flow through the vessel should be optimized to provide good contact between the glycol and carbon.
92. How frequently should the carbon be changed?
This depends upon how clean the glycol is. The carbon in a purifier, installed on a new glycol unit, can last 2 years if the incoming gas is kept clean.
93. How can we tell when the carbon filter needs changing?
The carbon should be changed when the glycol starts getting dark or when the pressure drops across the carbon purifier reaches 10 to 20 lbs. Lab analysis and excessive foaming will also indicate hydrocarbon contamination.
94. What mesh size carbon should be used?
That depends upon the vessel design. The two most popular sizes are 4 x 10 and 8 x 30.
95. If the vessel has no provision for back flushing with water to remove loose dirt, what can be done to remove the dust?
Saturated steam can be put down through the bed to help remove the dust.
96. Does the carbon in the metal canister, which works like a solid, need to be washed?
No.
97. After the carbon has picked up a great deal of hydrocarbons, can steam be used to rejuvenate the carbon while it is still in the purifier?
Sometimes steam offers no help, but there is no harm in trying steam if it is available.
98. Will carbon in the purifier remove solids?
Yes, but not as efficiently as a solid filter.
99. Where should the carbon purifier be located in the circulating stream?
It should be located downstream of the sock filter, if one is used.
100. Can the carbon purifier be used in the high temperature service, e.g., between the glycol-glycol heater exchanger and the still column on the rich glycol side?
Yes.
101. We were losing carbon from our carbon purifier, and the manufacturer recommended we put a solid filter downstream. Is this necessary?
No. The carbon purifier simply has to be built properly so carbon cannot get out of the vessel.
102. If a carbon-packed column is used, what shape vessel is desired?
The vessel should have a length/diameter (L/D) ratio of 5:1 or better. The smaller diameter vessels should have a 10:1 L/D ratio. Maximum contact between the glycol and carbon is desired.