Producers use a natural gas filter separator to separate solids and liquids from natural gas.
Specifically, a filter separator removes impurities from natural gas, such as:
- Water
- Pipe Scale
- Iron Sulfide
- Liquid Hydrocarbons
- Compressor Lube Oil
- Sulfur Products
A filter separator differs from a standard oil and gas separator in that it uses a natural gas filter element to remove contaminants rather than mechanical devices.
Below, we'll explain:
- Why and Where Filter Separators are Used
- Main Types of Filter Separators
- Flow Path Through a Filter Separator
Why is a Natural Gas Filter Separator Used?
We are removing contaminants from the flow stream to meet quality and safety requirements set by the purchaser, which must be removed before it can be sold.
Producers install filter separators where contaminants are present and must be removed. This may be after compressors or prior to dehydration units or the delivery point.
In dry gas fields, this may be the only equipment required for separation.
Where is a Filter Separator Used?
Producers use filter separators at tank batteries as well as gas gathering and processing stations.
Every sector of our industry—upstream, midstream, and downstream—uses some type of filter separator.
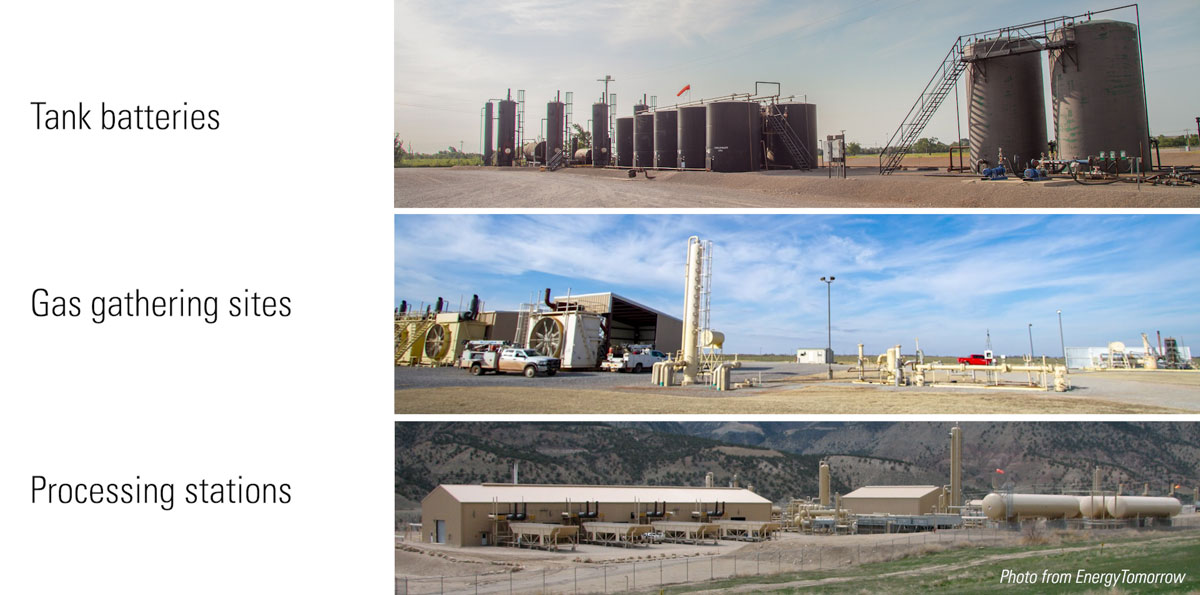
Types of Filter Separators
Horizontal filter separators are common for gas conditioning. They can handle higher concentrations of liquids and solids compared to vertical models.
Vertical filter separators are ideal for when ground space is limited.
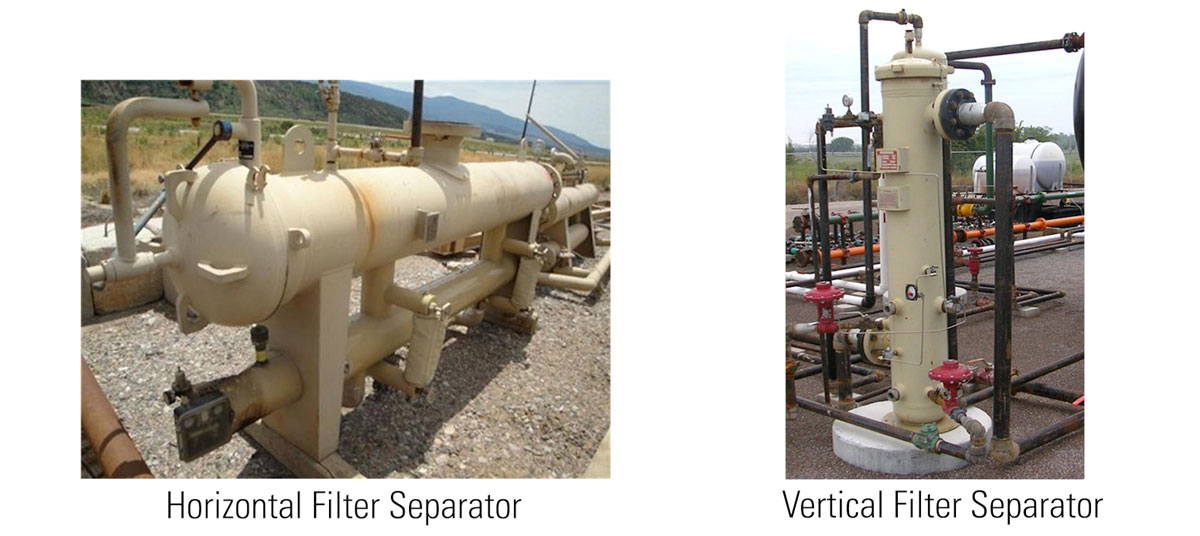
Types of Filters
Inside the filter separator canister are filter elements—either replaceable socks or coalescing filters.
Replaceable Sock Natural Gas Filter
In a replaceable sock filter, the entire gas stream flows through the sock filter, trapping solids and condensing liquids.
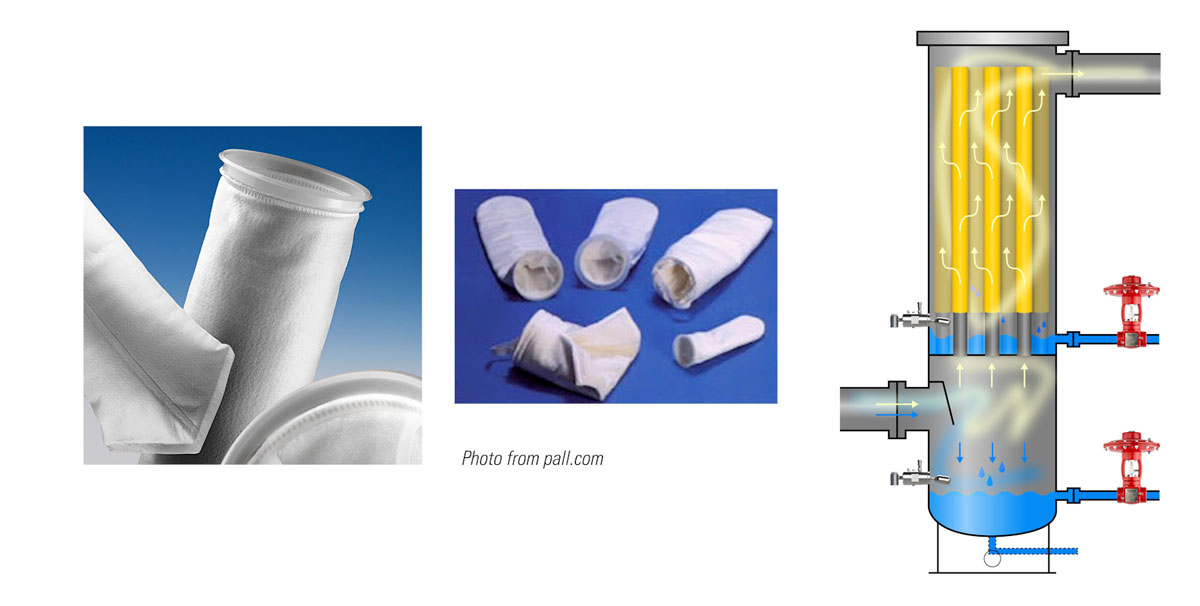
Coalescing Natural Gas Filter
Coalescing natural gas filters separate liquid particles from a gas stream.
Coalescence occurs when the entrapped liquid particles either combine with other nearby droplets and/or are struck by additional droplets trying to go through the filter.
Natural gas coalescing filters contain materials that repel many elements. Manufacturers coat the filter's fibrous surface with a very low-energy polymer such as a fluoropolymer or a silicone. This keeps the droplets from sticking to the filter and helps it shed the liquids.
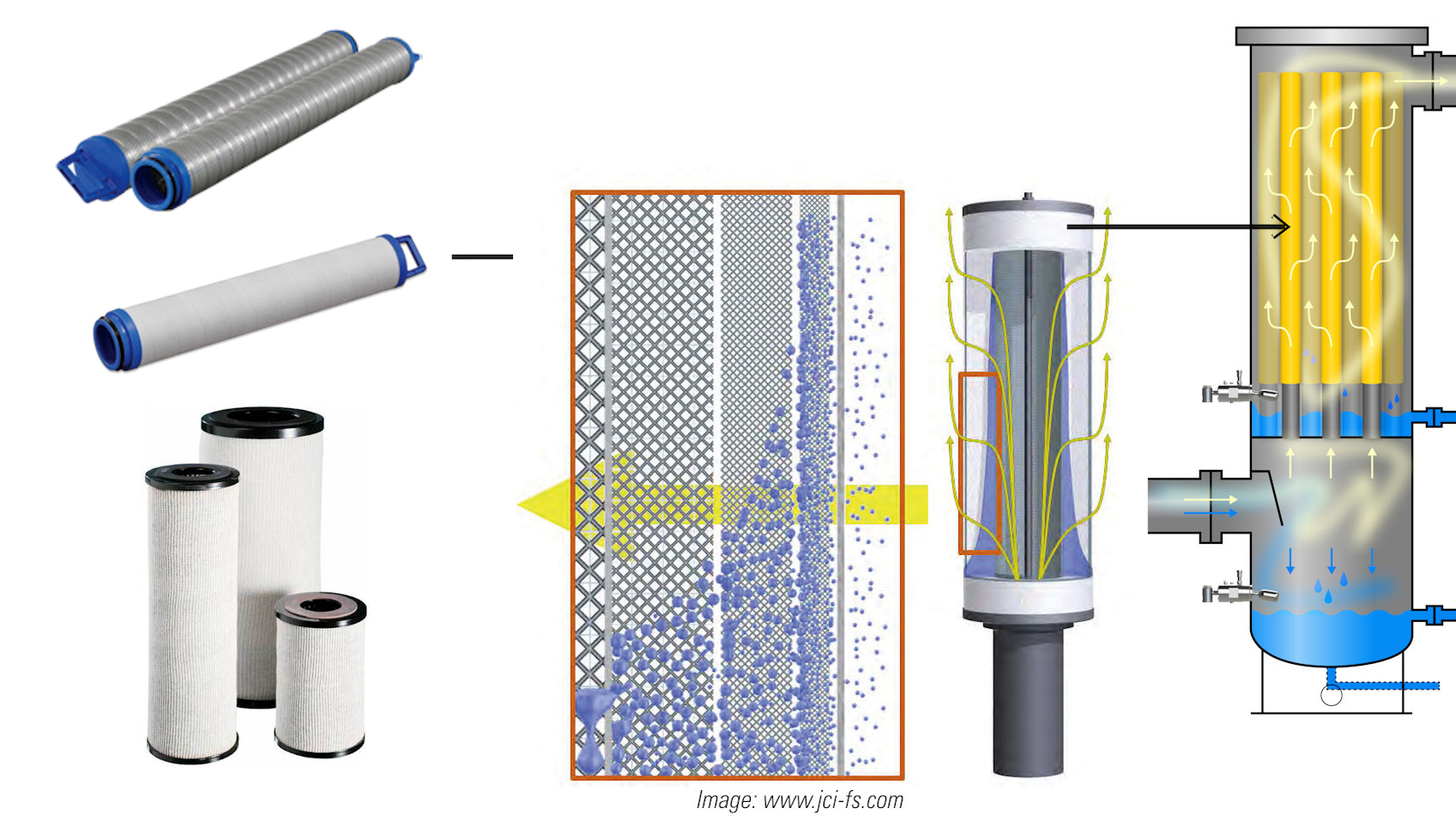
1- and 2- Stage Vessels
Filter separators have one or two stages, depending on the need of filtration. This is not the same concept as when we talk about a vessel having 2 or 3 phases.
On most production vessels, the number of level controls and control valves can help determine if a vessel is a 2 or 3 phase. However, on filter separators this can be a misleading because there can be one or two separate chambers combined into one vessel shell. We call these stages, rather than phases.
In a two-stage vessel there is a plate that divides the two stages and allows 2-phase separation to take place in each side of the vessel.
In a single-stage vessel there is only one type of filter element used. Some producers call this a single-element filter separator.
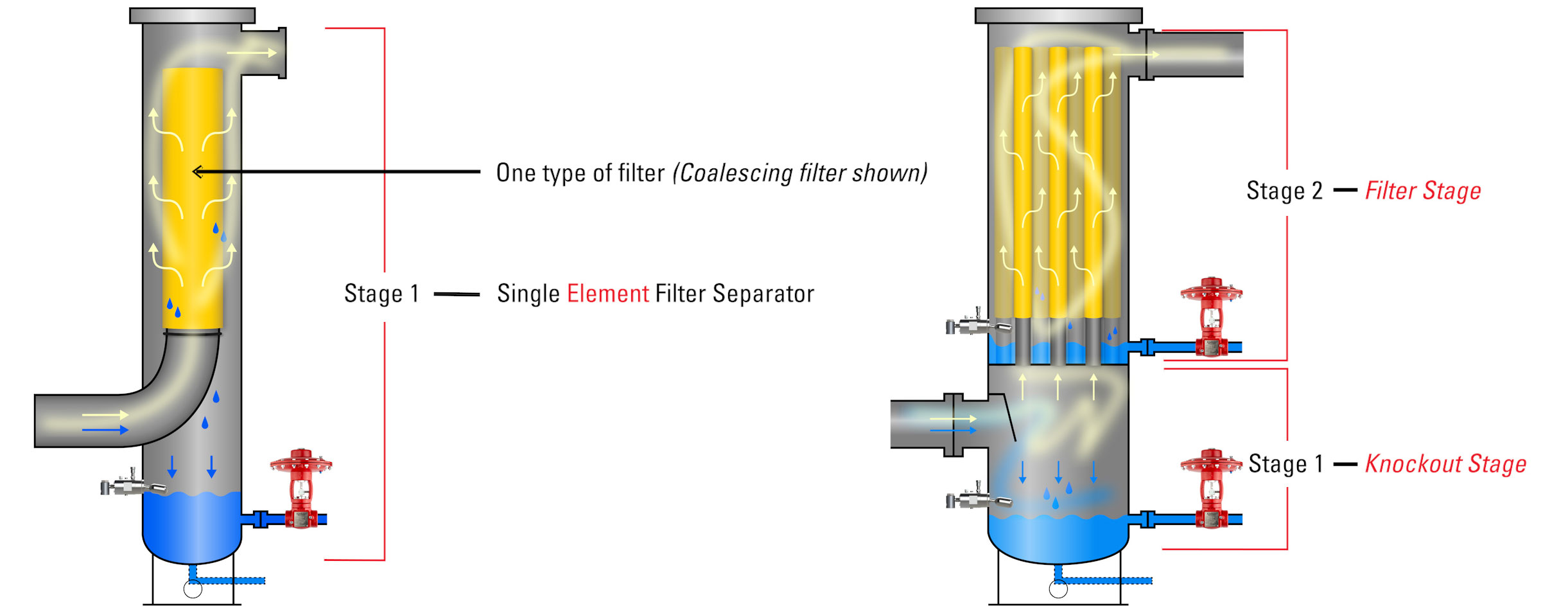
Low Pressure and High Pressure Filter Separators
Filter separator vessels are either high pressure, which is anything over 500 PSI, or low pressure, which is anything lower than 500 PSI. The vessel type will depend on the process conditions and application.
Controllers for Filter Separators
Pneumatic level switches are ideal for filter separators because they take up less space. The volume of liquid in the vessel is relatively small, and most of the space contains filter elements. This leaves no room for a standard level controller or a trunnion assembly for mechanical operation.
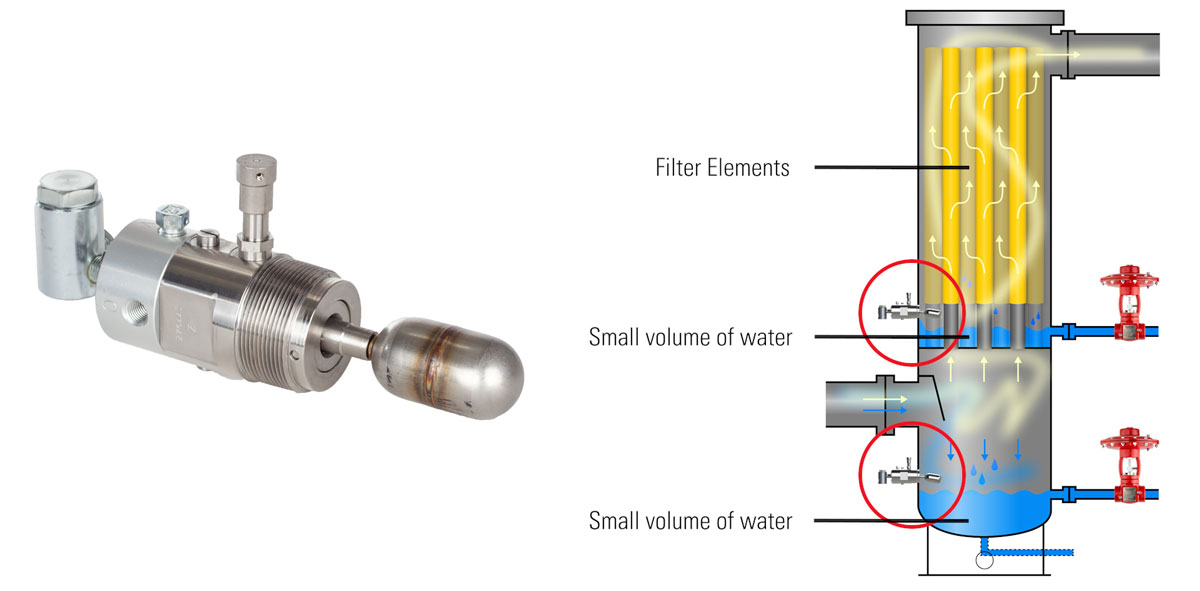
In a horizontal model, however, a Kimray Gen 3 Liquid Level Controller is an option because of the available space in the sump chamber part of the vessel.
On a single-stage vessel, producers may use a trunnion and float as an alternative.
Flow Through a Filter Separator
The rendering in the video shows the flow of natural gas through a horizontal, 2-stage filter separator.
As natural gas enters the unit, the first stage of filter elements captures solid particles. Coalescing filters allow any liquids present in the gas stream to coalesce into larger droplets. The gas moves through the tubes and into the second stage while the liquids drop out the bottom of the tank.
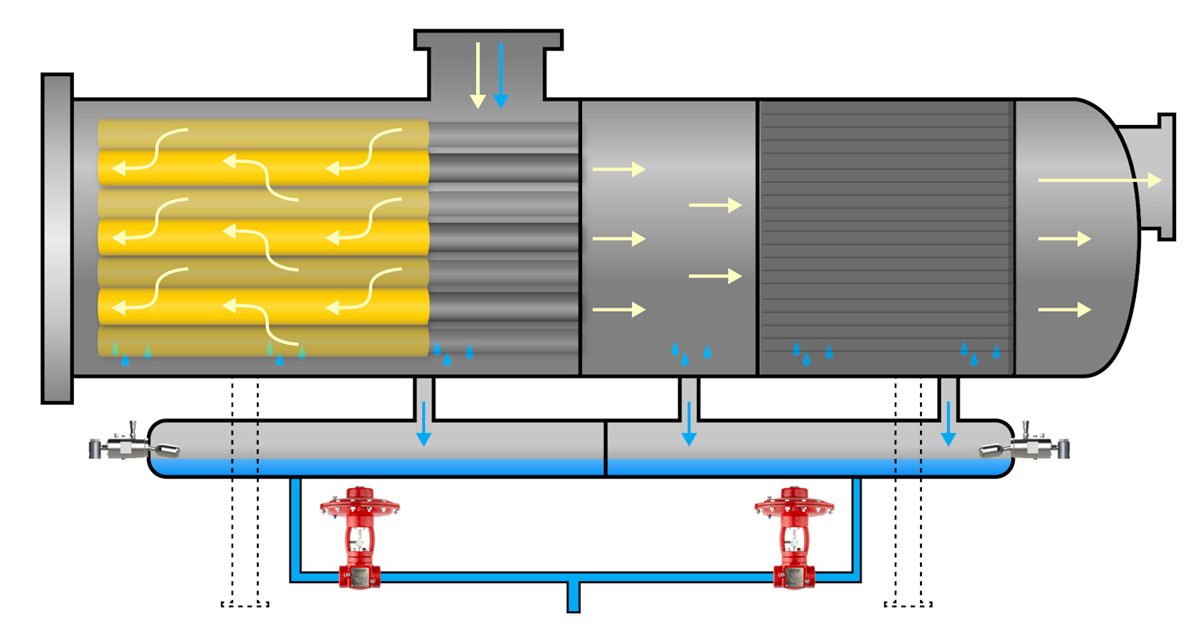
In the second stage, the wire mesh or vane mist extractor captures any remaining liquid droplets. The resulting gas stream is then virtually free of all particles no larger than the micro filter that's being used.
The liquid that has dropped out falls to the bottom of the vessel and is removed with a dump valve controlled by either a liquid level switch or a Gen 3 liquid level controller.
The principles of separation are the same for a vertical separator; only the arrangement of components differs.
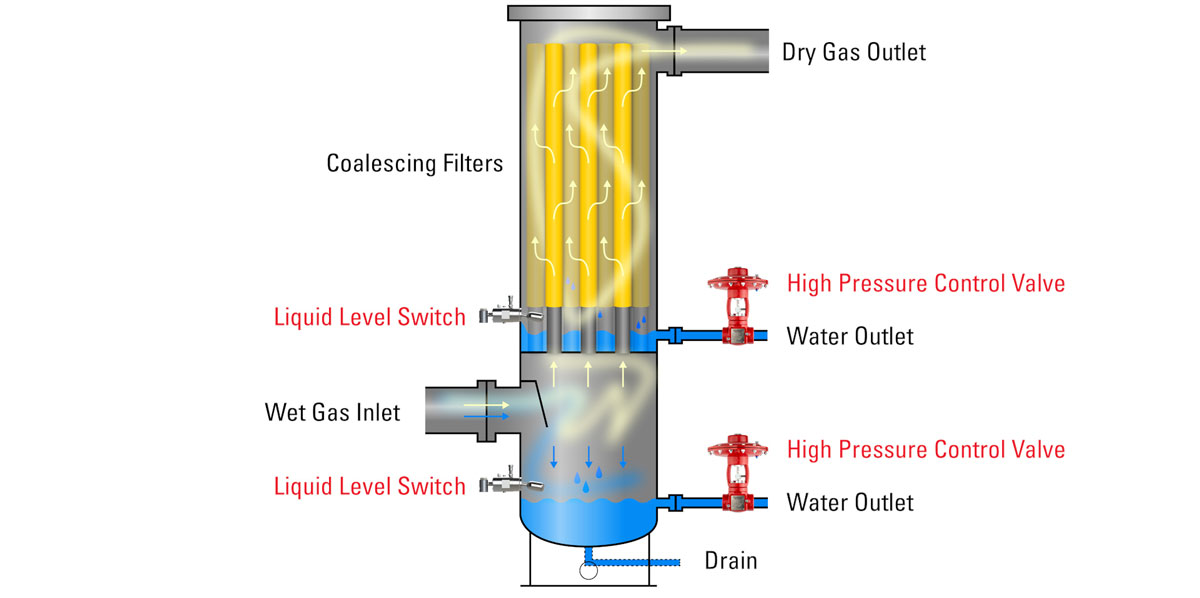