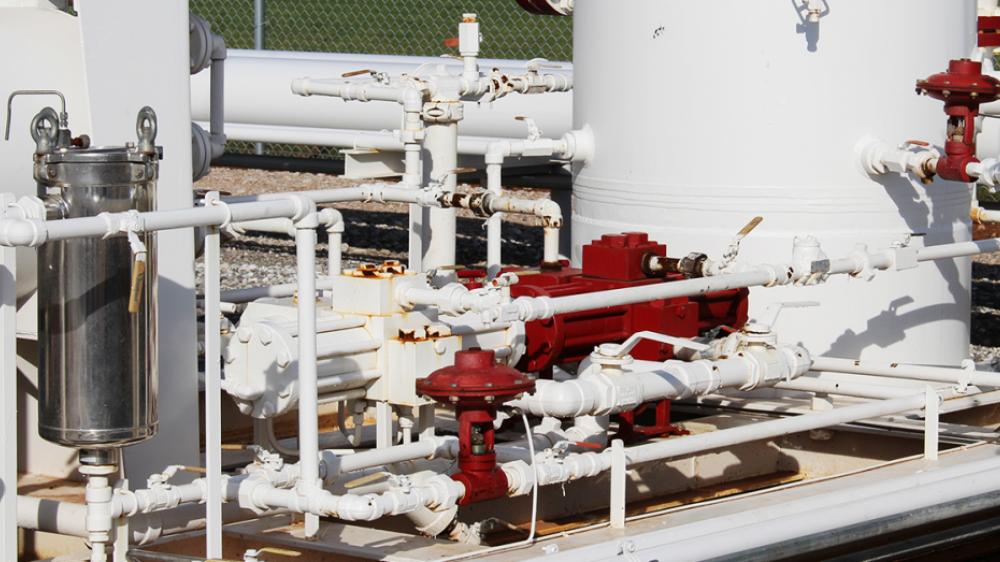
One of the biggest challenges in operating a glycol gas dehydration system is addressing glycol loss.
Most dehydration units are designed with a margin of 0.1 gallons of glycol per million feet of natural gas treated. If the system loses more than this it affects processes.
One of the most common ways glycol is lost is through foaming.
What is Glycol Foaming?
Glycol foaming happens most often when entrained hydrocarbons from production enter the glycol fluid.
As the entrained glycol processes through the contactor tower (or “absorber”) it will carry over the top of the tower with the sales gas when stable foam builds up on the trays.
Foaming also causes poor contact between the gas and the glycol, significantly reducing the drying of the gas.
Glycol Gas Dehydration System
4 causes of glycol Foaming
Temperature
Excessive temperatures can lead to a loss of glycol in the glycol reboilers. Temperatures above 400 F cause the vaporization and/or thermal decomposition of glycol. In particular, excessive top temperatures in the still column of the reboiler can allow vaporized glycol to escape to the atmosphere with the water vapor.
High temperature differentials between the gas and glycol in the contactor can also cause foaming and glycol loss.
The dry glycol inlet temperature should be no more than 20 degrees F greater than the temperature of the gas. A drastic temperature differential tends to emulsify the glycol with any contamination it may contain. This causes excessive glycol foaming, and high gas velocities through the tower can carry the glycol foam downstream.
Adequate heat exchange will lower the temperature of the hot glycol coming from the reboiler so that it does not cause foaming in the contactor. Over time, heat exchangers can become plugged with build up from contaminates in the glycol causing them to not operate efficiently. Good filtration will help mitigate these issues.
Turbulence
Excessive turbulence and high liquid-to-vapor contacting velocities can also cause the glycol to foam. This condition may point to underlying mechanical or chemical issues.
Lowering the velocity of the gas through the contactor and removing chemical contaminates through good filtration can help prevent glycol foaming.
Contaminants
Other causes of foam that may be present in the process fluid include field corrosion inhibitors, salt, or finely-divided suspended solids.
Contaminants like these present in the gas flow stream that were introduced upstream of the dehydration system need to be removed using different kinds of filtration.
Carbon filters can be used to remove hydrocarbon liquids from glycol to help prevent glycol foaming. These are typically installed downstream of the flash separator. Carbon or charcoal filters remove liquid hydrocarbons, compressor oils, degradation compounds and other carbon impurities from the glycol flow stream by catching these molecules in the charcoal's pores.
Field corrosion inhibitors, salt and finely divided suspended solids need to be filtered through solid particle filters such as sock or horsehair filters. These will remove these small particles from the glycol flow stream and are found throughout the dehydration system.
High pH Levels in Glycol
High pH levels in glycol cause foaming, which leads to glycol being swept out by the high velocity of the gas.
pH is a measurement of alkalinity or acidity of a fluid on a scale from 1-14. A pH rating from 0-7 means the fluid is considered acidic or corrosive, ratings of 7-14 indicate the fluid is alkaline. A rating of 7 is considered a neutral pH.
Often, a glycol analysis can be performed and will reveal high pH levels. Glycol with a pH level above 8.5 will tend to saponify hydrocarbons and cause foaming. Saponify is to turn fat or oil into soap, by reaction with an alkali. Alkaline neutralizers can be added to the glycol to help control high pH levels.
Optimum operating pH levels of glycol should remain between 7 - 7.5 to keep the glycol from foaming, emulsifying, or becoming corrosive.
How To Address Glycol Loss Due to Glycol Foaming
To dehydrate natural gas properly, your system needs clean glycol that is free from hydrocarbons and any other impurities. If you encounter foaming, your first step is to lower pressure and use an anti-foaming agent. This temporarily reduces the foam and continue processing gas.
However, this is a temporary fix.
To address the underlying issue, the best solution is to examine your filtration system and consider adding a carbon filter. Carbon filters are designed to remove dissolved impurities from the glycol solution.
Kimray manufactures products to support your glycol dehydration system, including our Energy Exchange Glycol Pump, Electric Glycol Pump, and versatile line of High Pressure Control Valves.
To speak with an expert about glycol dehydration, contact your local Kimray store or authorized distributor.