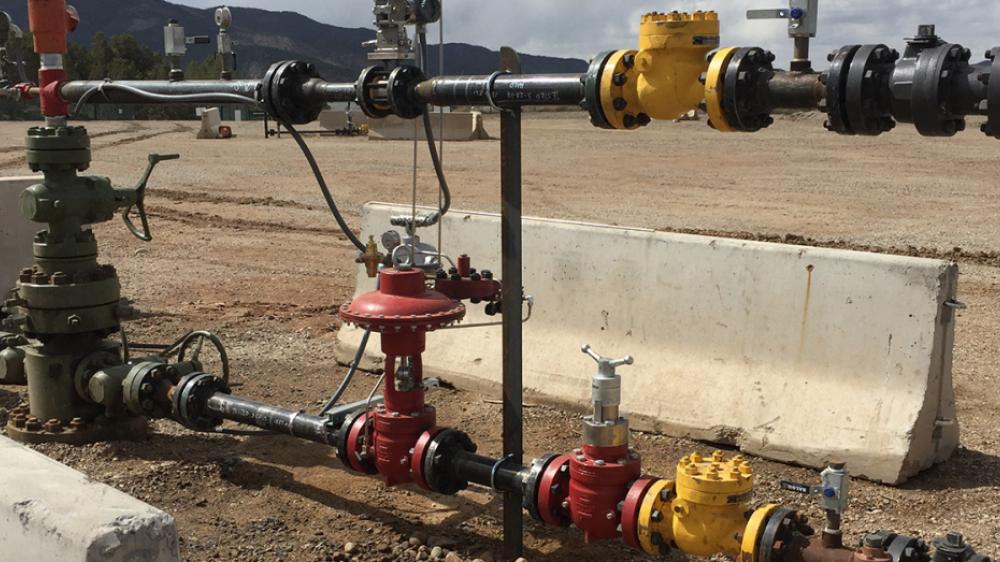
A Pressure Differential Controller on a Coal Gas Well
A pressure differential controller (PDC) acts as a pilot for a control valve, allowing it to maintain a span of pressure. Recently, a member of Kimray’s authorized distribution team met with a producer in New Mexico about production in his coal gas well.
It was low-flow well, only producing about 50-100 barrels of liquid a day, and flowing about 4mmcf a day through the tubing. He was using a high pressure control valve and a PDC, which was acting as the pilot.
The well had a good pressure differential between the casing and the tubing. The question he approached us with was this: How can we produce the casing while maintaining the volume and the flow rate in the tubing to keep the well from logging off?
The Flow Rate Challenge
When liquid entered the tubing and started to rise up the column, the flow rate gradually decreased. He was using the control valve and PDC to monitor and control the flow rate.
In this case, when the flow rate dropped as liquid entered the tubing, the casing valve closed. Then, when the well unloaded the liquid and the flow rate increased, the casing valve opened. This added the casing gas to the sales line.
Optimizing the Pressure Differential Controller
To maintain the pressure differential between the casing and the tubing, we made two adjustments to the pressure differential controller:
- Installed a heavier spring to provide a larger differential
- Reversed the output of the controller from Indirect to Direct
Reversing the output of the PDC to direct acting allowed the casing valve to open when the pressure differential was above the set point, and close when the differential was below the set point.
By making this change and selling the excess casing gas, this producer’s gas production volume increased by approximately 50%.