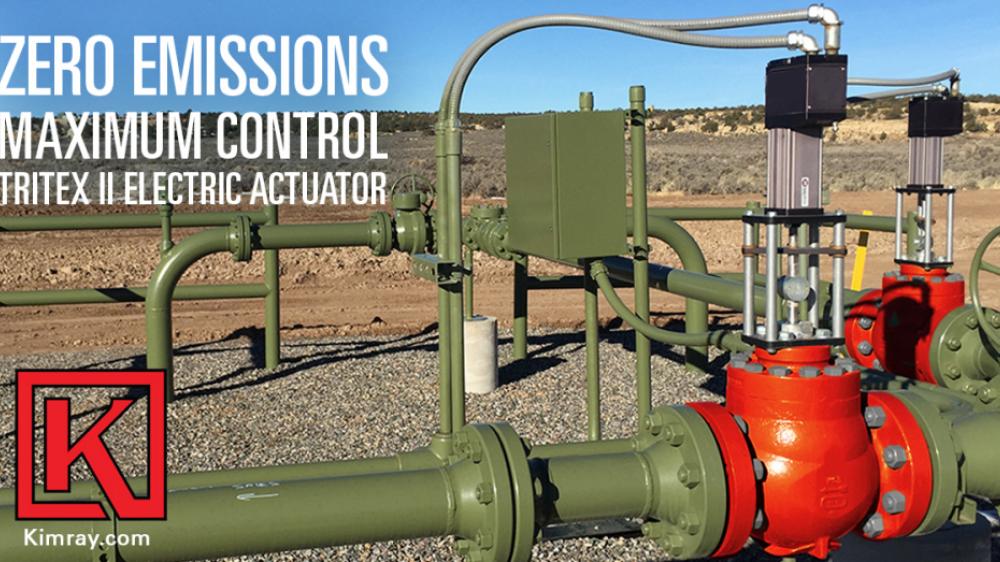
Plunger Lift
Plunger lift has provided our industry with secondary recovery for many years. It has taken on a more prominent role with the recommendation of the EPA that plunger lift be used instead of gas blow down as a way to alleviate bottom-hole pressure and remove liquids from the wellbore.
The purpose of this piece is to walk through is what role control valves play in this application and how Kimray enables accurate and repeatable control to prolong the life of wells.
A plunger lift system uses a piston as a mechanical interface between formation gas and produced liquids. During high flow rate the plunger rests in the lubricator. As production decreases, liquids accumulate and the well begins to load.
When the Kimray valve closes this stops the flow and the plunger drops through emulsion from its starting position to rest on the bumper. With the well shut in, the pressure builds in the annulus. When the casing pressure reaches its optimum pressure, the plunger lift controller tells the valve to open, allowing the plunger to return to the lubricator while removing the liquid from the tubing.
Pneumatic Actuators
Pneumatic valves use 30 PSI of either gas or air to open and close the “plunger lift” valve. When the valve opens the actuator fills with the gas or air, and when the valve needs to close it vents that element into the atmosphere.
The issue with pneumatic options is the venting. While it is possible to use air compressor to power the valve, most operations use supply gas coming out of the well. This gas is then vented when the valve closes, releasing gas into the atmosphere. Because of the increasing regulations on gas emissions, more and more operations are shifting away from pneumatic valves.
Electric Actuators
The R2L-Valvcon Package couples with a quarter-turn electric actuator to open Kimray valves. In Class 1 Div 1 areas you can use a 4-20mA signal or a 0-10V signal to open and close the valve. This is solution is 100% electric and does require supply gas, therefore emitting no gas into the atmosphere.
The Tritex II Electric Actuator is another option for zero-emission actuation. In Class 1 Div 2 areas you can use an analog, digital, or MODBUS signal to open and close the valve quickly, remotely, and with very fine accuracy.
The Challenge
An oil and gas producer in the Permian was looking for a solution to optimize and automate their plunger lift control valves. The producer approached Kimray with three primary challenges that needed solving:
- Eliminate the use of supply gas due to the large amount of hydrocarbons emitted from their current system.
- Remotely monitor and control their well site.
- Make these upgrades without increasing operating costs.
The Solution
After assessment of the site and discussion of the producer’s required specifications, Kimray recommended a 45-day trial of the Tritex Valve Actuator. During the testing period, Kimray proved that we could meet each one of their challenges.
- The Tritex is a completely electric, zero-emission actuator. No pneumatics are needed, eliminating the need for supply gas, so their first challenge was met.
- The Tritex’s communication feature allows the valve to be controlled remotely. The producer had an automation system already in place, so we helped them connect the Tritex to this system, making effective remote communication possible.
- The Tritex required an ostensibly higher investment upfront. However, the producer catalogued the parts and completed a cost analysis in order to get a complete picture. The results were positive. Because the Tritex eliminated the need for all the pneumatic devices, regulators, scrubbers, gauges, tubing and even the valve topworks, this option was a much closer comparison than originally thought. After taking into account the lower operating and maintenance expenses as well, this proved to be a cost-effective option for this producer moving forward.
Benefits of the Solution
- Elimination of supply gas venting, which will led to lower gas loss and an improved environmental situation.
- Elimination of supply gas control issues such as wet gas, sour gas, freezing moisture or contaminants in the valve actuator.
- Remotely controlled valve settings and feedback received through SCADA or Signet.
- Accurate measurements received by precisely controlling the flow rates and differential pressures.